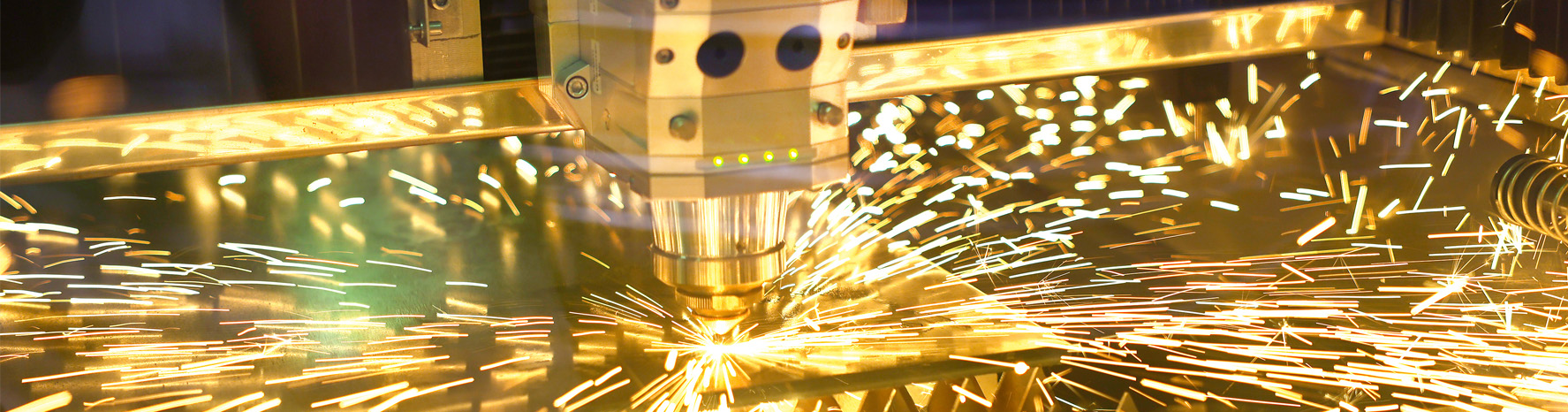
Die Zukunft der Metallverarbeitung: Wie Hochleistungs-Laserschneiden neue Maßstäbe setzt
Stellen Sie sich ein Werkzeug vor, das so präzise ist, dass es Metall mit der Finesse eines erfahrenen Handwerkers schneiden kann – und das mit der Kraft von Tausenden von Watt. Dies ist keine Szene aus einem futuristischen Film, sondern die Realität der Faserlasertechnologie im heutigen Metallschneiden. Die Entwicklung begann mit Faserlasern, die zunächst in der Lage waren, bescheidene 3 mm dicke Metallbleche zu durchtrennen – ein Fortschritt, der eine neue Ära der Effizienz und Vielseitigkeit in der Fertigung einläutete.
Mit dem technologischen Fortschritt war es nur logisch, die Leistung weiter zu steigern. Der Sprung von Hunderten von Watt auf mehrere Kilowatt war nicht nur eine numerische Veränderung, sondern eine Revolution im Metallschneiden. Anfangs ermöglichten Maschinen mit 1 bis 2 kW Leistung bereits das Schneiden dickerer Metalle, was eine direkte Korrelation zwischen Leistung und Produktivität zu bestätigen schien. Doch als die Grenze von 20 kW überschritten wurde, trat ein faszinierendes Phänomen auf: Eine höhere Leistung führte nicht mehr automatisch zu größerer Effizienz oder der Fähigkeit, noch dickere Materialien zu schneiden.
Es ist entscheidend zu verstehen, dass die reine Laserleistung nicht der einzige Faktor für die Schneidfähigkeit ist. Anwendungen in der Praxis – von Laborbedingungen bis hin zu den rauen Gegebenheiten industrieller Produktionsstätten – zeigen, dass es auf ein fein abgestimmtes Zusammenspiel zwischen Leistungsausgabe und Schnittqualität ankommt. Die Wahl eines Lasers für die Metallbearbeitung erfordert die Berücksichtigung einer sogenannten „Leistungsreserve“ – das bedeutet, mehr Leistung zu wählen, als auf den ersten Blick notwendig erscheint. Diese Reserve dient nicht dem Übermaß, sondern der Flexibilität, um hochwertige Schnitte für unterschiedlichste Materialien und Bedingungen zu gewährleisten.
Die Wahl des Gases – Stickstoff, Sauerstoff oder ein Gasgemisch – spielt eine entscheidende Rolle im Schneidprozess, insbesondere bei verschiedenen Metallen wie Nichteisenmetallen, Edelstahl oder schwarzem Eisenblech.
- Stickstoff ermöglicht schnelle, saubere Schnitte bei dünneren Metallen und übertrifft Sauerstoff sowohl in Geschwindigkeit als auch in Effizienz deutlich. Dies liegt daran, dass die Verwendung von Sauerstoff beim Schneiden eine deutlich breitere Schnittfuge erzeugt, was die Schneidgeschwindigkeit verringert.
- Die langsamere Schneidgeschwindigkeit von Sauerstoff hingegen eignet sich besser für dickeres schwarzes Eisen, da die geringeren Kosten des Gases die reduzierte Geschwindigkeit ausgleichen können.
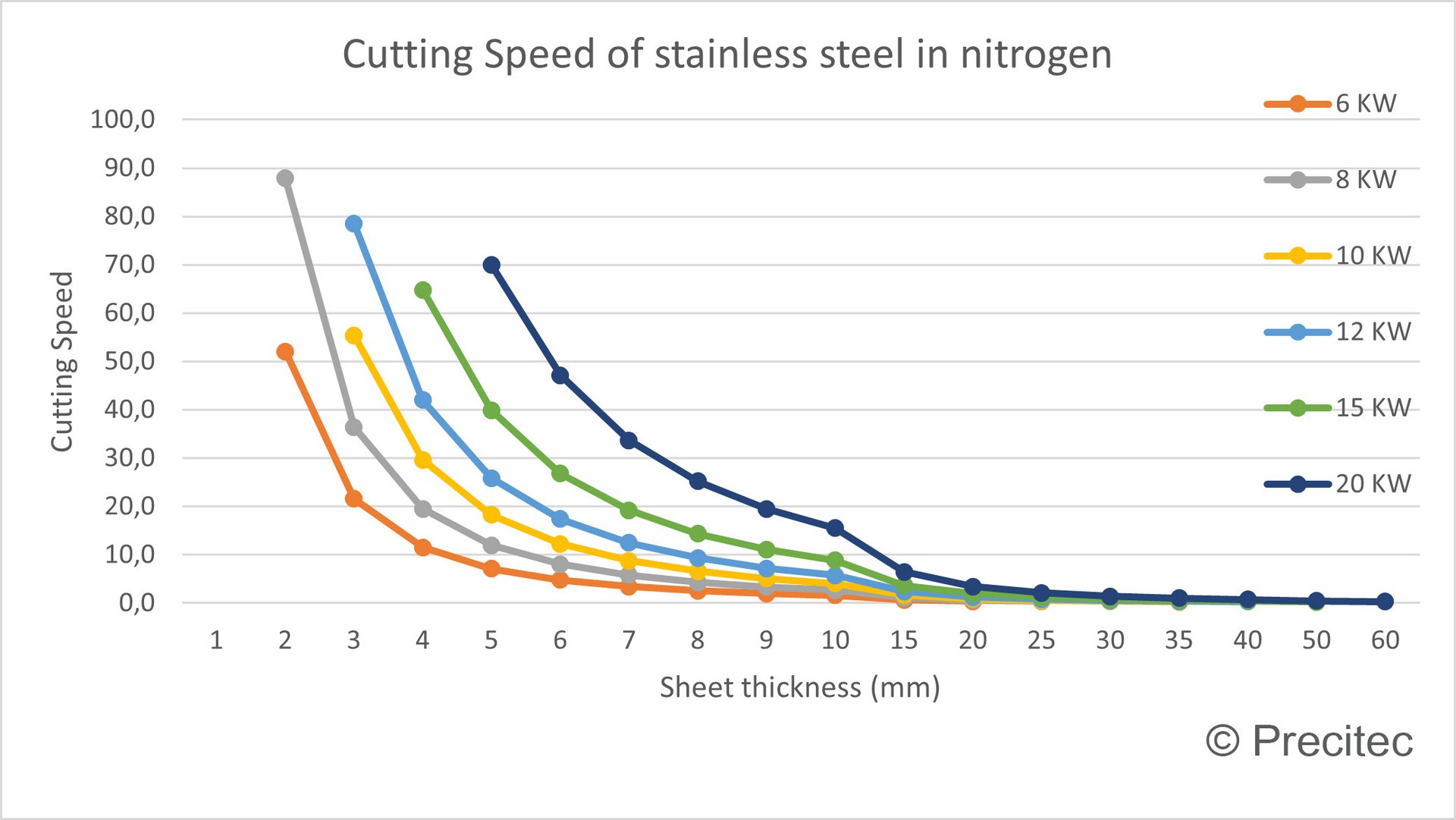
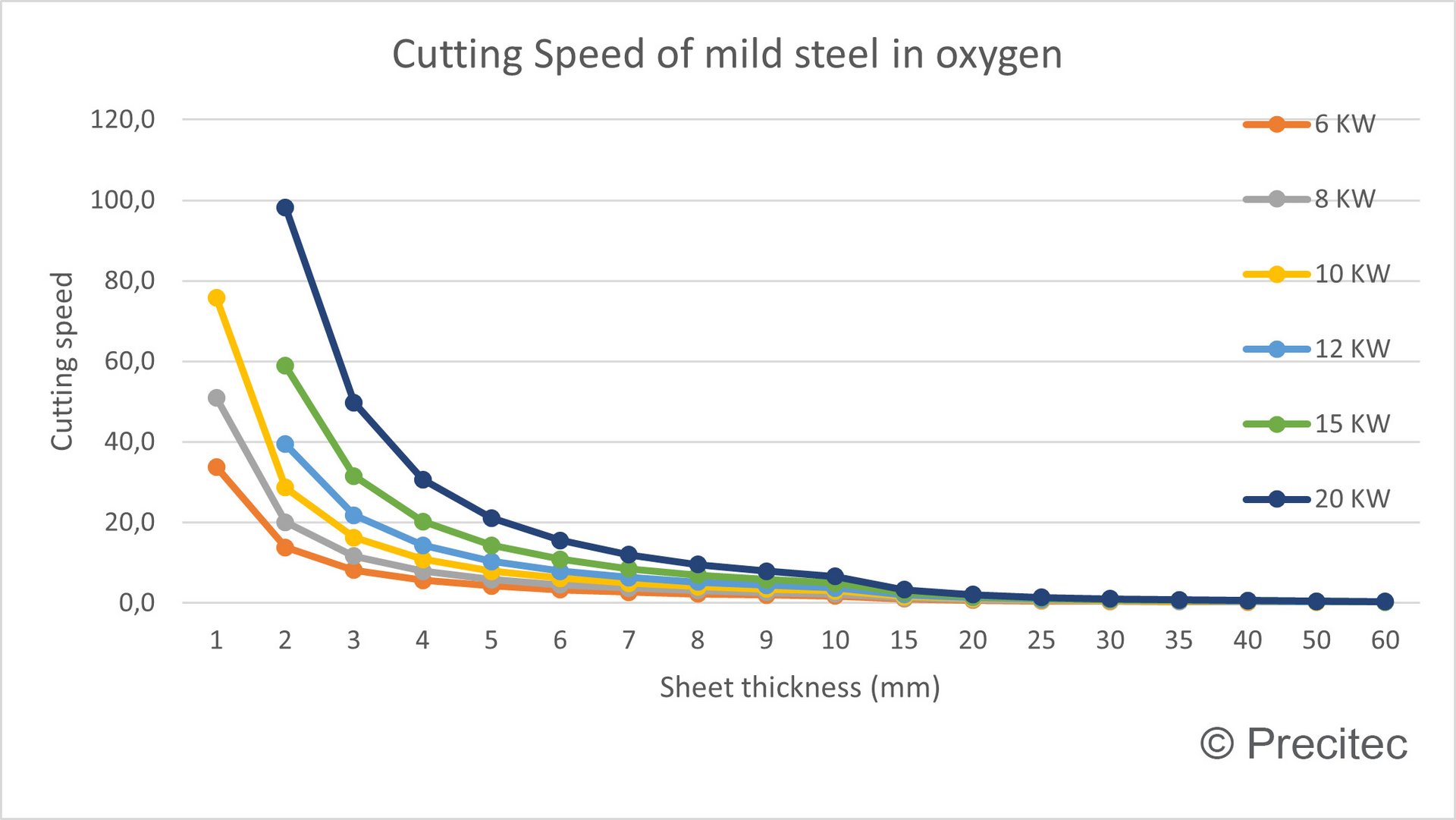
Die Grafik zeigt, dass die Erhöhung der Laserleistung sowohl bei Edelstahl mit Stickstoff als auch bei Baustahl mit Sauerstoff zu einer deutlichen Steigerung der Schneidgeschwindigkeit bei bestimmten Materialdicken führt und gleichzeitig das Schneiden dickerer Materialien ermöglicht.
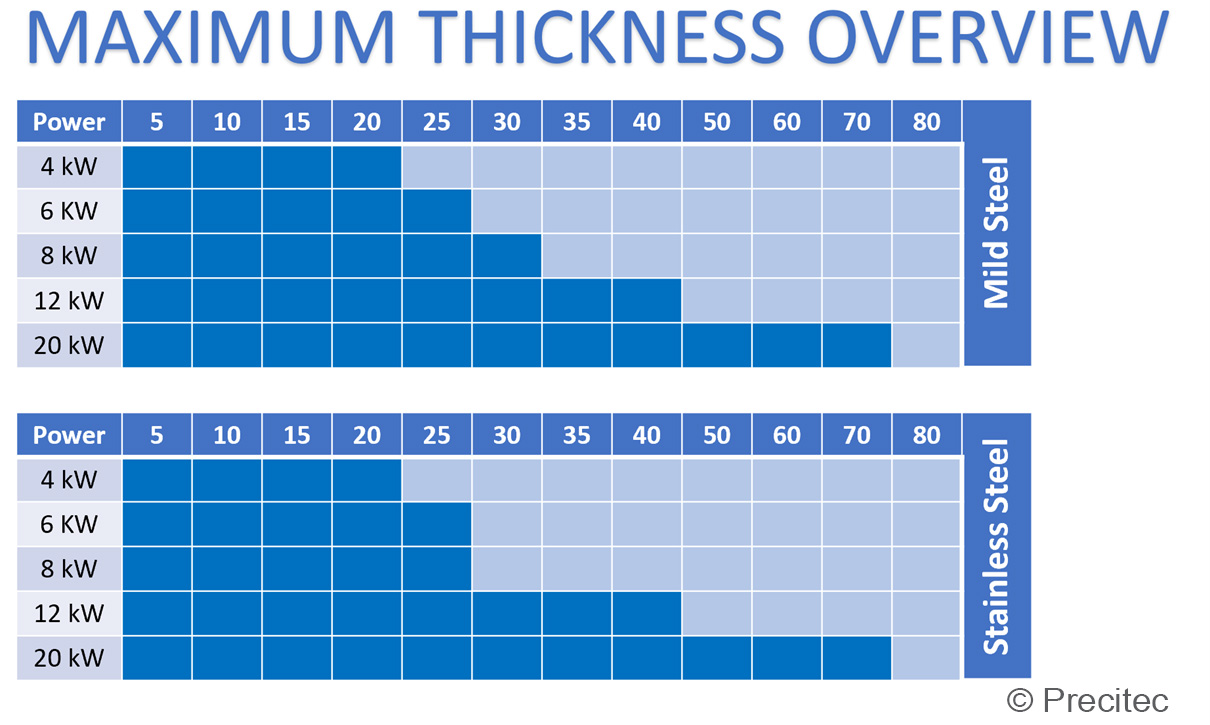
Die Tabelle unterstreicht die entscheidende Rolle der Auswahl des geeigneten Stützgases für das Laserschneiden: Sauerstoff verbessert die Schnittgeschwindigkeit und -fähigkeit von Baustahl, während Stickstoff für oxidationsfreie, saubere Schnitte in Edelstahl sorgt. Die Wahl zwischen Stickstoff und Sauerstoff geht über die bloße Schnittgeschwindigkeit hinaus und verkörpert ein Gleichgewicht zwischen Effizienz, Kosten und Umweltaspekten.
Obwohl das Schneiden mit Stickstoff höhere Geschwindigkeiten und sauberere Kanten bietet, erfordert es einen höheren Gasdruck, was zu höheren Betriebskosten führt. Dennoch können die Vorteile der verbesserten Effizienz und die relativ geringeren Kosten von Stickstoff diese Kosten überwiegen, was ihn zur bevorzugten Option für ein breites Anwendungsspektrum macht.
Die Grafik erinnert an die vielfältigen Faktoren, die für einen effizienten und qualitativ hochwertigen Laserschnitt berücksichtigt werden müssen, wie zum Beispiel:
- die Art des Stahls
- die Dicke
- die Laserleistung
- die Wahl des Stützgases
Die Daten zeigen eindeutig, dass höhere Ausgangsleistungen erhebliche Vorteile mit sich bringen - vom Schneiden dickerer Materialien bis hin zum Erreichen von Geschwindigkeiten - die zuvor als unmöglich galten. Ein 3-kW-Laser kann durch eine 15 mm dicke Platte navigieren, aber eine Verdoppelung der Leistung auf 6 kW kann diese Fähigkeit weiter ausbauen und sowohl die Dicke als auch die Schnittgeschwindigkeit verbessern. Ein ähnliches Phänomen kann bei einer weiteren Leistungssteigerung beobachtet werden.
Da wir an der Schwelle zu weiteren Fortschritten in der Lasertechnologie stehen, liegt der Fokus nicht nur auf Leistung. Es geht darum, das gesamte Ökosystem des Laserschneidens zu verstehen, von Materialeigenschaften und Schneidgasen bis hin zu Betriebseffizienz und Umweltauswirkungen. Die Zukunft der Metallverarbeitung liegt in Investitionen nicht nur in höhere Leistungsausbeuten, sondern auch in intelligentere, nachhaltigere Technologien, die die Grenzen des Möglichen verschieben.