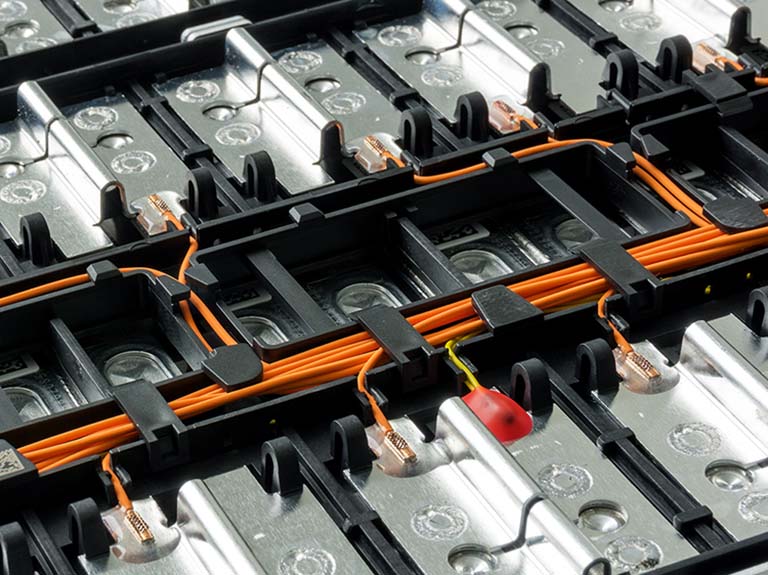
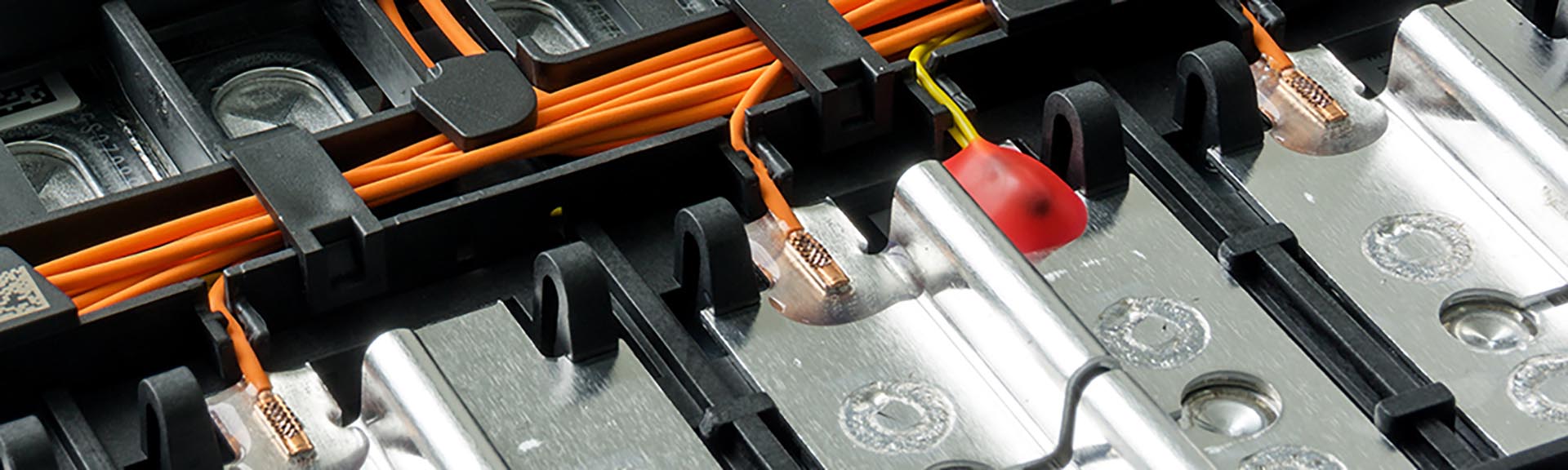
Sichere und zuverlässige Zellkontaktierung: Innovative Lösungen für die Batteriemodulherstellung
Ausgehend von einzelnen Batteriezellen geht die Prozesskette weiter zur Herstellung der Batteriemodule. Nachfolgend werden diese in einen Metallrahmen aus Aluminium oder Stahl gruppiert, den sogenannten Packs zusammengefasst, um dann anschließend mit der Batteriewanne verklebt zu werden.
Unter den oben genannte Prozessschritten gibt es einen kritischen, da sicherheitsrelevanten Prozess: das Kontaktieren der einzelnen Batteriezellen. Hierbei ist es wichtig, dass der Zellverbinder sicher auf die einzelnen Zellen aufgeschweißt wird. Dabei handelt es sich um eine I-Naht am Überlappstoß. Tückisch ist diese Verbindung deshalb, da visuell nicht nachgewiesen werden kann, ob beide Bleche miteinander verbunden sind. Man spricht hierbei vom Fehlertyp des „Falschen Freundes“.

Lösungen für Ihre Fertigungsschritte in der Batteriemodulherstellung
Um ein qualitativ hochwertiges Bauteil zu liefern, das mechanischen Belastungen standhält, die Anforderungen der Schweißnahtnorm erfüllt, das Brechen von Schweißnähten oder das Auftreten von Rissen vermeidet und den Produktspezifikationen entspricht, müssen mehrere Merkmale der Schweißnähte überprüft werden. Etwaige Pinholes müssen aufgespürt werden, da die Dichtheit entscheidend ist, die Nahtunterfüllung muss auf ihre Widerstandsfähigkeit gegenüber mechanischen Belastungen geprüft werden, der Nahtunterschnitt muss zur Vermeidung von Kerbwirkungen und Rissen geprüft werden, und die Nahtbreite muss zur Kontrolle der Fokuslage geprüft werden.
Die Lösung für all diese Herausforderungen ist unser Zeilensensor CHRocodile CLS 2, der mit hoher Messgeschwindigkeit die gesamte Topografie in einer Zeile messen kann - selbst bei Merkmalen, die kleiner als 5 µm sind.
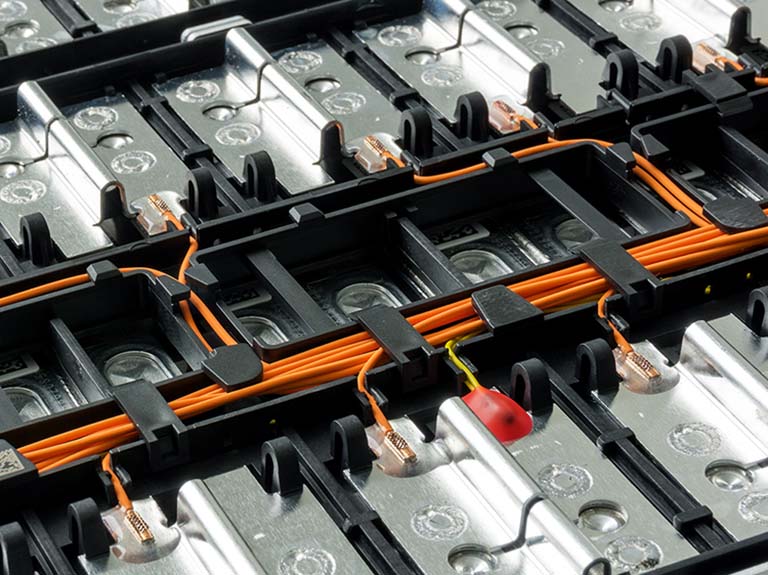
Ob zylindrisch, prismatisch oder als Pouch – die präzise und punktgenaue Fertigung der Batteriezellen ist ein entscheidender Faktor für ihre Leistung und Qualität. Der Laser arbeitet berührungslos und stellt dafür ein sicheres Werkzeug dar. Beim Kontaktieren der Batteriezellen untereinander entstehen verzugsfreie Nähte mit geringem und lokal begrenztem Wärmeeintrag. Jede einzelne, geschweißte Kontaktierung kann online überwacht, bewertet und dokumentiert werden. Unsere Systeme erkennen Unregelmäßigkeiten und fehlerhafte Schweißungen. Nicht konforme Teile können nachgeschweißt werden. So ist eine 100%ige Rückverfolgbarkeit und Transparenz Ihrer Prozesse möglich. Kosten und Qualität Ihrer Zellproduktion lassen sich dadurch optimieren.
Ein kritischer Fehler bei der Kontaktierung von Batteriezellen zu Zellmodulen ist der sogenannte „Falsche Freund“: Rein visuell betrachtet sieht die Schweißnaht gut aus, allerdings besteht kein elektrischer Kontakt. Die Detektion dieser Fehler mit Qualitätsüberwachungssystemen ist daher essenziell.

In klassischen Rundzellen, den zylindrischen Batteriezellen, werden Elektrodenfolien aufgerollt und in einem Metallgehäuse verschlossen. Die Zellen werden im nachgelagerten Schritt miteinander kontaktiert, um später die volle Leistung ausspielen zu können. Beim Kontaktieren zylindrischer Zellen verschweißt der Laser sehr dünne Schichten zwischen 100 und 400 µm. Die punktgenaue und reproduzierbare Bearbeitung dieser ist essenziell und erhöht in Kombination mit einer Online-Prozessüberwachung die Prozesssicherheit Ihrer Fertigungsanlage. Kosten, Qualität sowie Durchsatz Ihrer Zellproduktion lassen sich somit optimieren.
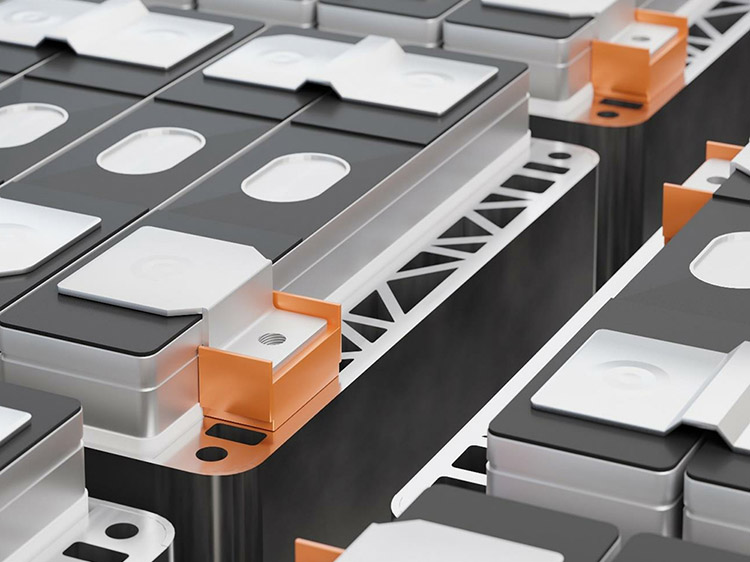
Akkupacks für die Elektromobilität werden zunehmend mit UV-härtenden Lacken oder Epoxidlacken lackiert. Die Dicke dieser Lackierung muss gemessen werden, da sie eine zwingende Voraussetzung ist und besonders in kritischen Bereichen wie z. B. an den Ecken der Akkus wichtig ist. Leider bieten die vorhandenen Kontaktmesstechniken nur eine geringe Wiederholgenauigkeit und sind stark bedienerabhängig.
Die ideale Lösung für die Messung der Lackschichtdicke auf Batteriezellen ist die laserphotothermische Technologie von Precitec Enovasense, die es ermöglicht, ganze Oberflächen mit einer hervorragenden Präzision zu messen. Diese Technologie ermöglicht eine berührungslose, zerstörungsfreie, eingriffsfreie, strahlungsfreie Messung der Lackschichtdicke mit hervorragender Wiederholgenauigkeit in einem schnellen und kostengünstigen Verfahren. Sie profitieren von einer verbesserten Prozessqualität durch In- oder Offline-Messungen mit einem kompakten, leichten Gerät, das sich leicht in Ihre Produktionsprozesse integrieren lässt. Mehrere Messpunkte können durch vorprogrammierte Zyklen in Sekundenschnelle abgedeckt werden, wenn der Sensor in den vollautomatischen 3-Achsen-Leitstand HKL2 eingebettet ist.
Detaillierte Informationen können durch Ausfüllen des Formulars heruntergeladen werden.
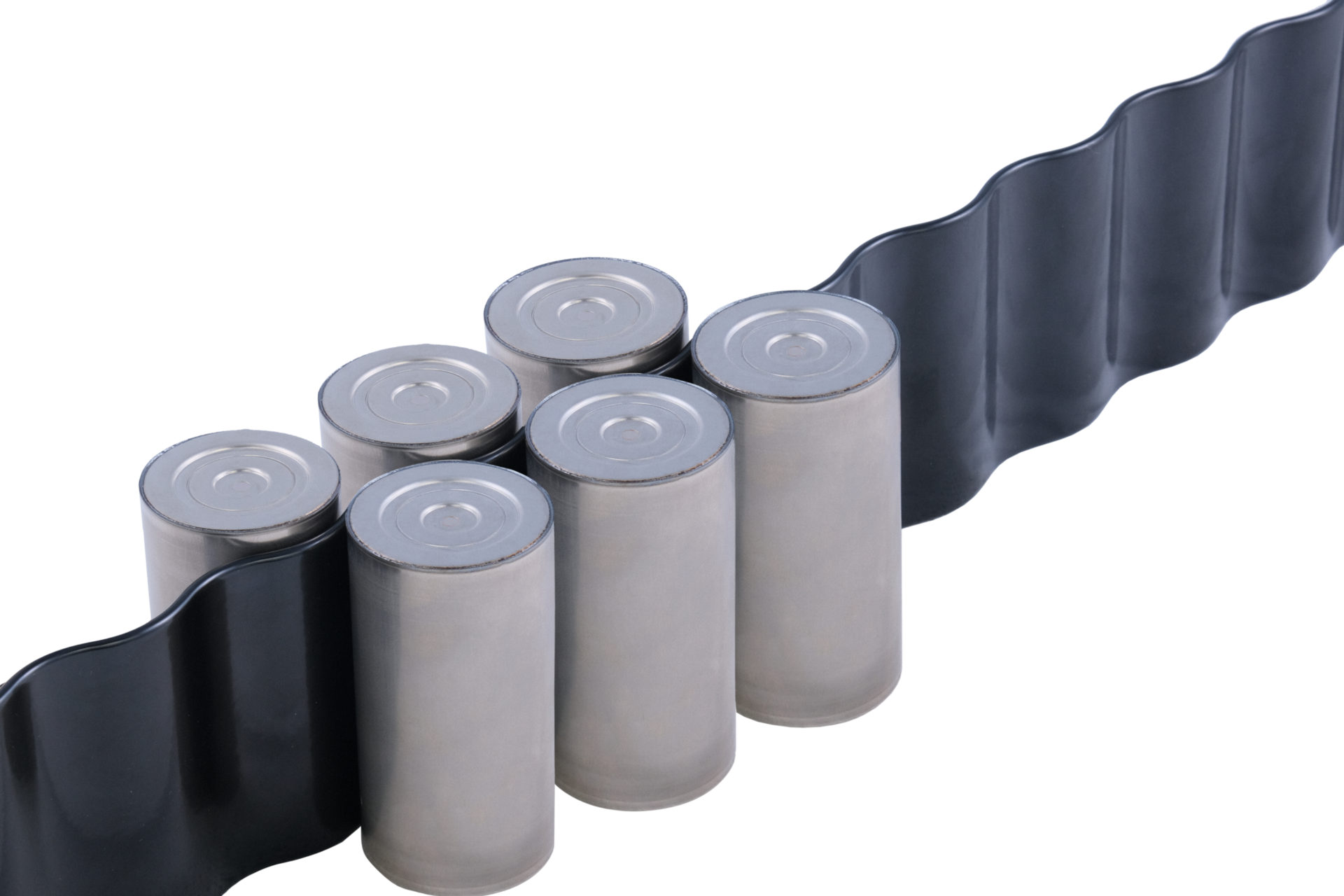
Die Leistung und Lebensdauer von Batteriezellen hängen stark von der Betriebstemperatur ab. So ist ein effizientes Thermomanagement erforderlich. Sogenannte Kühlungsplatten oder Kühlkanälen helfen die Betriebstemperatur der Batterien im optimalen Bereich zu halten.
Die meist aus Aluminium hergestellten Kühlungsplatten enthalten Kühlmittelkanäle, in denen die Kühlflüssigkeit zirkuliert und Wärme abtransportiert wird. Ein gleichmäßiger und vollflächiger Kontakt ist hierbei wichtig. Isolationsschichten werden genutzt, um die Batterie und Kühlplatte elektrisch voneinander zu isolieren und dadurch Kurzschlüsse zu vermeiden und die Sicherheit zu gewährleisten.
Egal ob die Schichten transparent oder intransparent sind – die Precitec Punktsensoren bieten die Möglichkeit, diese Schichten zu vermessen.
Sie möchten mehr über die Vermessung von transparenten Schichten erfahren? Klicken Sie hier
Sie möchten mehr über die Vermessung von intransparenten Schichten erfahren? Klicken Sie hier
Einzelne Batteriemodule werden im anschließenden Schritt in Batterieboxen zusammengefasst. Diese bestehen aufgrund von gewünschten Gewichtsreduzierungen von Karosserien aus hochfesten Aluminiumlegierungen der 5xxx-er und 6xxx-er Serie. Heißrisse und Spritzer sind an dieser Stelle als größte Herausforderung zu nennen. Daher ist für das riss- und porenarme Laserschweißen von Aluminiumstrukturen der Einsatz hochgenauer Qualitätsüberwachungssysteme unumgänglich.
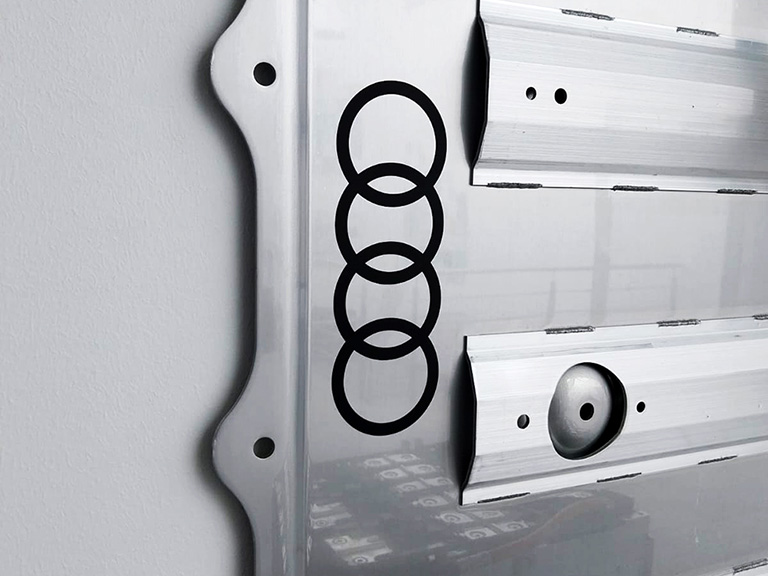
Die Batterieboxen werden im Fertigungsprozess vollflächig auf den Unterfahrschutz gesetzt. Ein partielles Verstärken durch das Aufschweißen hochfester Materialien sorgt für einen dauerhaften Halt und widerstandsfähigen Schutz der Batteriemodule. Intelligente und automatisierte Laserschweißsysteme überzeugen hier durch die hochdynamische Strahlführung, die gezielte Reduzierung der Wärmeeinbringung und damit der optimalen Ausformung Ihrer Schweißnaht. Die Bewertung der Fügenaht erfolgt im unmittelbaren Anschluss an die Laserschweißung.
Weitere Anwendungsfelder in der e-Mobility
Batteriezelle
Batteriezellen sind das Herzstück der Elektromobilität und damit entscheidend für die Sicherheit, Lebensdauer und Performance von E-Fahrzeugen. Unsere Produkte zur Lasertechnik und 3D-Messtechnik ermöglichen kontinuierliche Innovationen in der Batterieproduktion wodurch Kosten gesenkt werden und die Leistungsfähigkeit der Batteriezellen zunehmen.
Brennstoffzelle
Eine Brennstoffzelle besteht aus zahlreichen Bipolarplatten, die gasdicht verschweißt werden müssen. Meistens sind dabei die Schweißgeschwindigkeiten sehr hoch - ähnlich wie der Qualitätsanspruch an die Schweißnaht. Des Weiteren müssen für eine hohe Performance der Brennstoffzellen geometrische Kenngrößen der Bipolarplatten exakt eingehalten werden. Diese vermessen wir mit unseren Sensoren der 3D-Messtechnik.
Antriebsstrang
Der elektrische Antriebsstrang besteht u.a. aus Stator, Rotor und der Leistungselektronik. Für hochwertige Laserschweißungen bei Statoren (Hairpin-Schweißungen) sind gut abisolierte Hairpin-Drähte entscheidend. Wir können sowohl Lackrückstände an Drähten detektieren als auch adaptive Laserschweißprozesse ermöglichen.