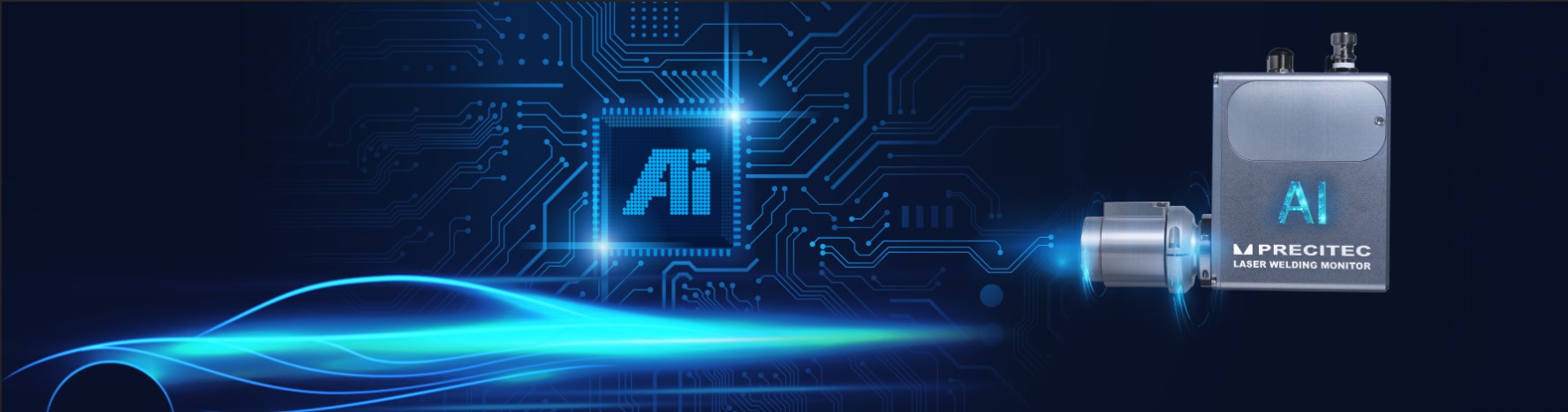
Optimierte Qualitätsüberwachung für Ihren Laserprozess mit künstlicher Intelligenz
Produktionsprozesse sind einem ständigen Wandel unterworfen, der neue und innovative Lösungen erfordert. Durch den Einsatz von künstlicher Intelligenz haben Hersteller nun die Möglichkeit, ihre Produktionsprozesse noch weiter zu optimieren.
Der Laser Welding Monitor LWM mit seiner neuesten KI-Funktion stellt einen Durchbruch bei der Analyse von Laserschweißemissionen dar. Mit dieser Technologie können physikalische Eigenschaften wie die maximale Kraft, die die Schweißnaht aushalten kann, einfach vorhergesagt werden. Dies ermöglicht eine Berechnung und erhöht die Objektivität bei der Analyse der Schweißnaht.
Der Laser Welding Monitor, LWM, erkennt Prozessunregelmäßigkeiten in einer vollautomatischen Produktionsumgebung und ist das passende Arbeitsgerät, um Ihre Qualitätsanforderungen zu erfüllen. Jede einzelne Laserschweißung wird überwacht, analysiert und dokumentiert, um eine vollumfängliche Rückverfolgbarkeit und Konsistenz in der Serienproduktion zu gewährleisten.

Vorhersage und schlanke Prozesse
LWM KI sieht Schlüsseleigenschaften für präzise angemessene Schweißgrenzen vor
Rationalisierung von Prozessen mit einem einzigen Wert, der akzeptable Grenzen definiert

Bewertung und Berechnung
LWM KI bietet quantifizierbare Ergebnisse und erhöht die Objektivität

Anpassungsfähigkeit und Analyse
Erhalten Sie gültige Ergebnisse ohne Nachschulung, während Sie die Prozessparameter in einem bestimmten Bereich ändern
LWM KI identifiziert die Grundursachen und unterstützt so die Fehlerklassifizierung und Nacharbeitsstrategien
Batteriekontaktierung und Hairpin-Schweißen mit künstlicher Intelligenz
Mit dem LWM mit künstlicher Intelligenz werden Emissionen dazu genutzt, Daten über die physikalischen Eigenschaften der Laserschweißnaht zu gewinnen.
Die Funktion wurde erfolgreich für die Anwendungen Batteriekontaktierung und Hairpin-Schweißen getestet. Bei der Batteriekontaktierung kann die maximale Kraft der Schweißnaht erfolgreich vorhergesagt werden.
Beim Hairpin-Schweißen kann der effektive Querschnitt vorhergesagt werden. Bis zu einem gewissen Grad kann sogar die Ursache für eine minderwertige Schweißnaht, wie z. B. mangelnde Laserleistung oder falsche Fokusposition, vorhergesagt werden (Klassifizierung). Wenn die Grundursache identifiziert ist, kann der Endanwender eine fortschrittliche und angepasste Nachbearbeitungsstrategie anwenden. Aufgrund des fortgeschrittenen Trainings des Modells kann der Benutzer die vortrainierten Prozessparameter innerhalb eines bestimmten Bereichs, wie z. B. die Laserleistung, variieren, während das Modell weiterhin gültig ist.