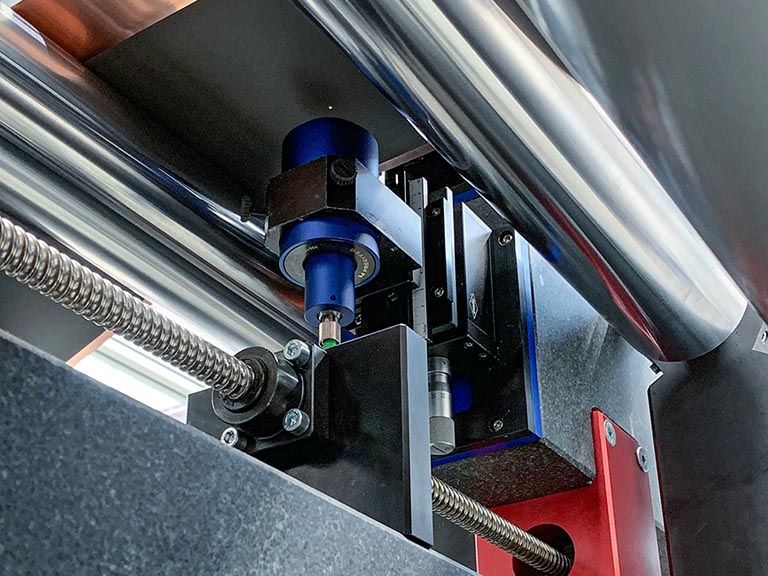
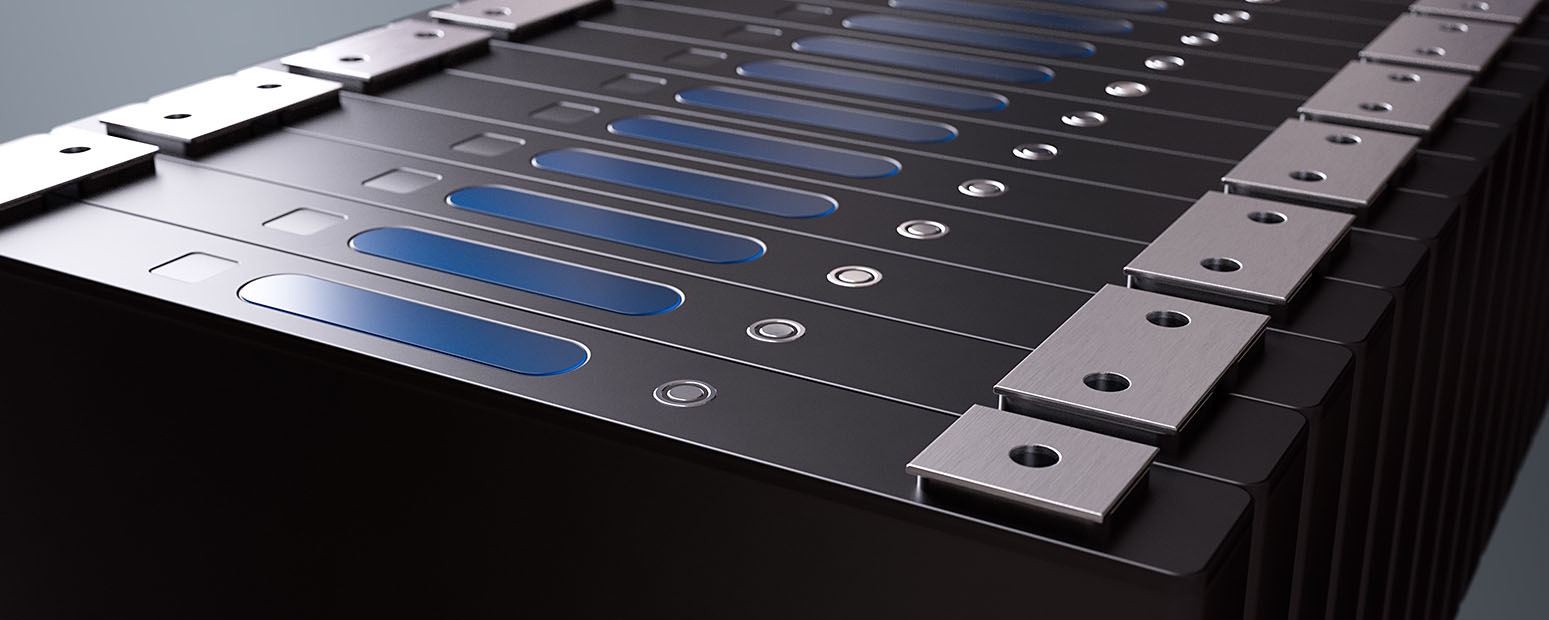
Soluciones eficientes para la producción de pilas de iones de litio
En la fabricación de electrodos, las pilas están formadas por capas alternas de láminas anódicas y catódicas. Están separadas por el llamado separador. A continuación, la pila de láminas se enrolla, se empaqueta en una carcasa metálica y las pilas se sueldan de forma segura.
Para garantizar una producción eficiente de las pilas, nuestros sistemas de control de calidad se utilizan en numerosos pasos del proceso, como la medición del grosor de la lámina del electrodo, la comprobación de la rebaba de corte y la soldadura por láser de las capas de lámina (lámina a lámina) y de la carcasa con la tapa (tapa a lata).
El requisito claro del cliente en este caso es Precisión < 1 micrómetro. Nuestros sensores cumplen este requisito y están optimizados para los entornos de producción de pilas de batería, las denominadas aplicaciones roll-to-roll:
- altas velocidades de banda
- láminas de electrodos vibrantes
- superficies brillantes y negras.
En la tecnología láser, la soldadura láser cap-to-can es una aplicación crucial. El objetivo es detectar agujeros de alfiler o, en el mejor de los casos, evitarlos por completo. Hemos optimizado nuestros productos y ópticas específicamente para estas aplicaciones y hemos desarrollado soluciones innovadoras.
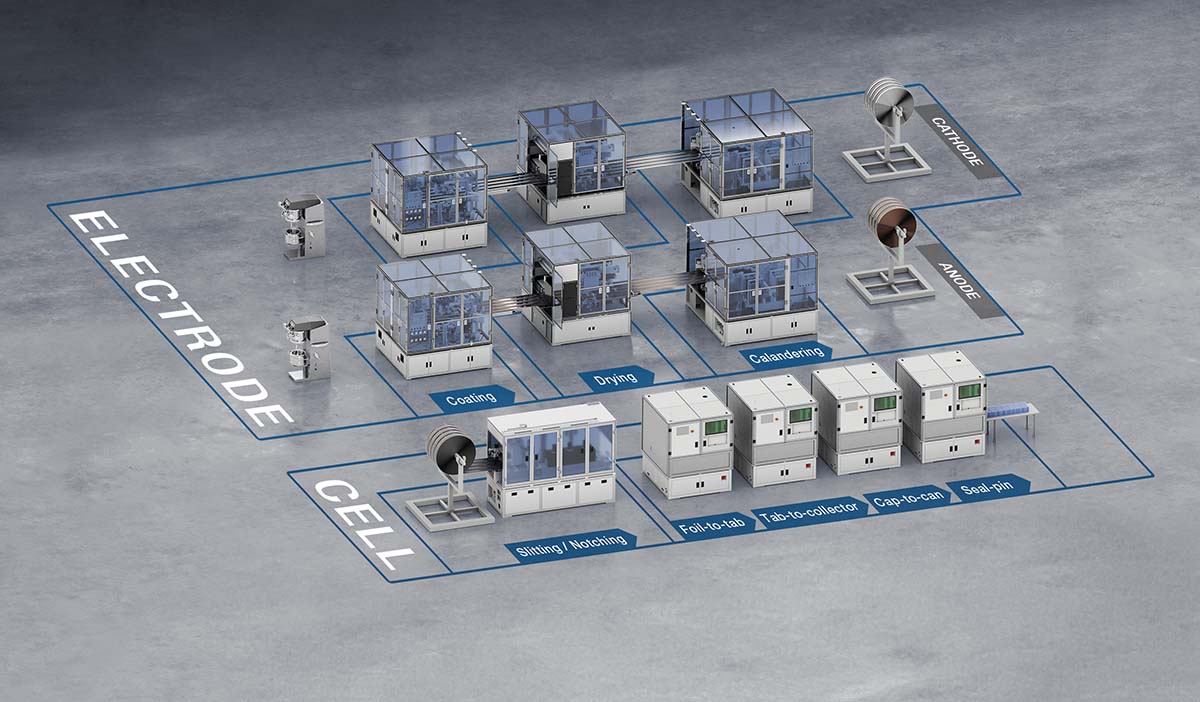
Soluciones para sus fases de fabricación de electrodos
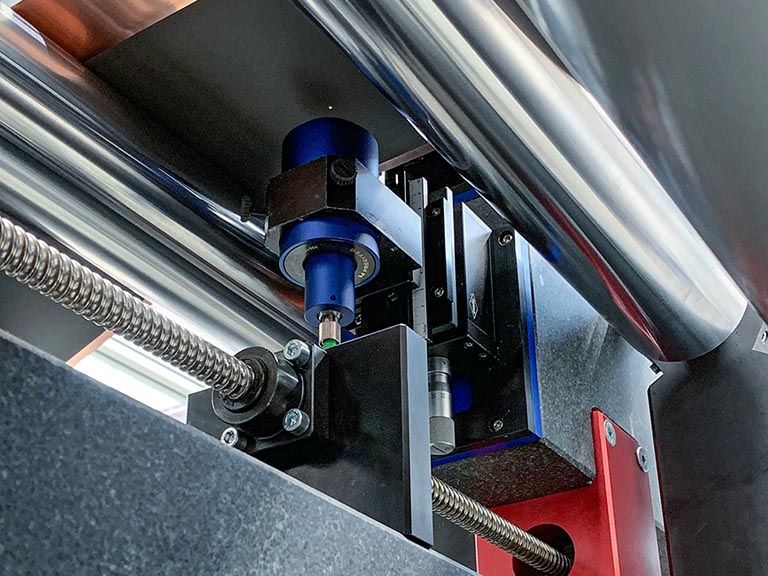
El grosor exacto del revestimiento de las láminas de electrodos desempeña un papel fundamental, ya que influye notablemente en el rendimiento y la vida útil de las baterías. En el proceso de producción, la lámina portadora se recubre primero de forma continua o intermitente con el lodo y después se elimina el disolvente del recubrimiento en el canal de secado.
Las mediciones de espesor se realizan antes y después del proceso de secado. El revestimiento puede estar en estado seco o húmedo, es decir, nuestra medición siempre es precisa independientemente de si la superficie es reflectante, negra o porosa. Se compensan los efectos de la vibración y la velocidad de la cinta. La ondulación y el grosor de la película se analizan con precisión y se muestran los resultados. Los requisitos actuales del mercado son una resolución absoluta de < 1 µm, con una repetibilidad de 0,5 µm.
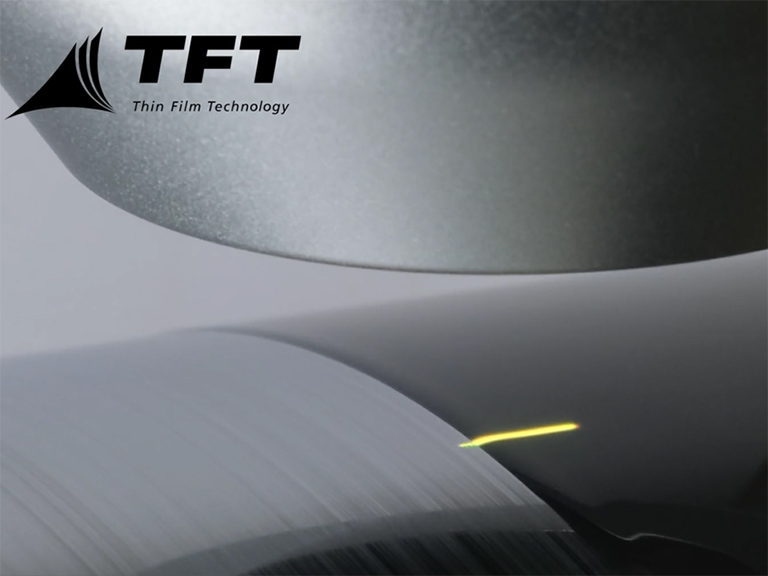
El peralte del borde se produce en el borde de la lechada aplicada y puede tener un efecto negativo en el procesamiento posterior del electrodo, especialmente durante el bobinado. Puede dar lugar a un bobinado asimétrico y, por tanto, a graves problemas de manipulación.
Para mejorar el rendimiento de las pilas de batería, actualmente se intenta aumentar el grosor del revestimiento. Sin embargo, los revestimientos más gruesos también tienden a formar un borde elevado.
Nuestro sensor de línea permite medir con precisión el borde en una longitud de hasta 20 mm durante el proceso de producción. Se pueden detectar tanto bordes húmedos como secos. Se tiene en cuenta la vibración de la banda. Se pueden visualizar con precisión las transiciones de láminas portadoras reflectantes y metálicas a lodo negro.
El borde de arranque/parada se produce durante el recubrimiento intermitente. En este proceso, la lechada se aplica alternativamente a la película portadora o se omite deliberadamente. Los bordes de arranque/parada suponen un reto en este tipo de revestimiento y deben controlarse para garantizar una larga vida útil y la seguridad de la célula de la batería.
Con nuestros sensores puntuales, la topografía puede medirse con precisión y los posibles defectos del revestimiento pueden detectarse a tiempo y con exactitud.
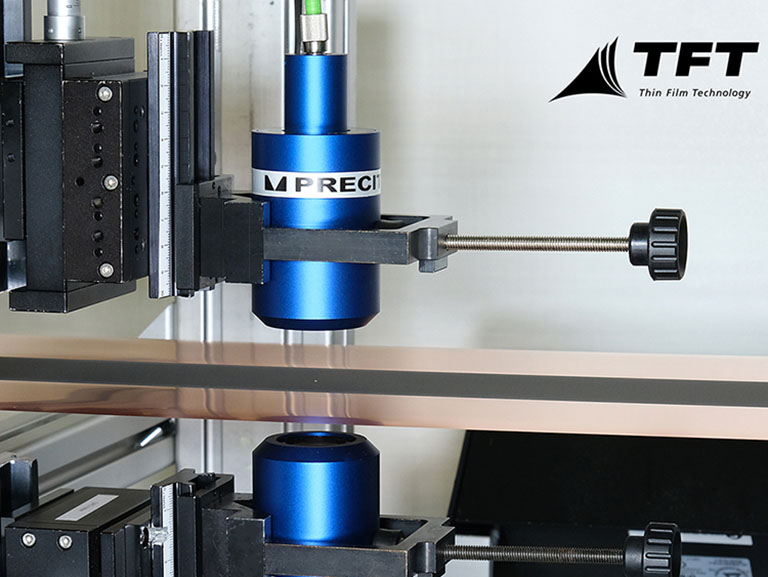
El grosor exacto del revestimiento de las láminas de electrodos desempeña un papel fundamental, ya que influye notablemente en el rendimiento y la vida útil de las baterías. En el proceso de producción, la lámina portadora se recubre primero de forma continua con la lechada y después se elimina el disolvente de la capa en el canal de secado aplicando calor. Para garantizar una elevada fuerza de adherencia de la lechada sobre la lámina portadora, es esencial identificar las 5 etapas del secado. Por ejemplo, debe evitarse la migración del aglutinante. El momento en que los poros se vacían por completo también es crucial para optimizar el secado.
Nuestros sensores permiten reconocer estos puntos en el tiempo durante el proceso de secado. Esto puede acortar el tiempo de secado, optimizar la calidad del recubrimiento y ahorrar costes energéticos.
También se pueden realizar las mediciones de espesor más precisas durante todo el proceso de secado. Ya se trate de capas húmedas o secas, grafito negro o poroso o material activo catódico, el resultado de la medición sigue siendo exacto. Los efectos de la vibración y la velocidad de la cinta se compensan durante la medición.
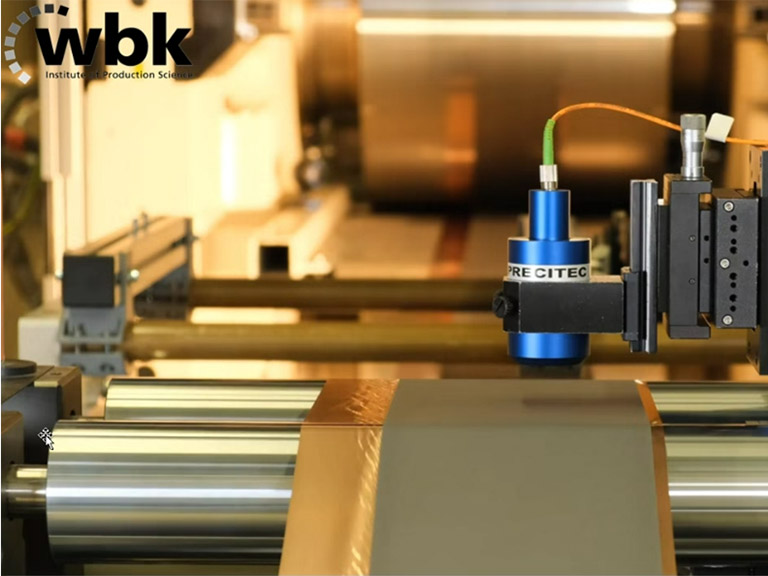
El calandrado es el último paso del proceso de fabricación del electrodo. Aquí es donde se decide el grosor final y la porosidad del revestimiento. Además del peso de la superficie, son características decisivas para el rendimiento y la seguridad de la célula de la batería.
Nuestros sensores permiten medir exhaustivamente el proceso de calandrado. Se mide el grosor del electrodo antes y después del calandrado, la concentricidad de los rodillos de calandrado y las llamadas arrugas. Se trata de arrugas en el borde del revestimiento sobre el material de soporte. Nuestros sensores compensan las vibraciones de las películas y compensan las ondulaciones. Esto permite realizar mediciones precisas en todo momento, incluso a velocidades de cinta elevadas de entre 100 y 150 m/min.
Los rodillos de calandra son rodillos de acero macizo con diámetros superiores a 1 metro. Las superficies reflectantes se rectifican con precisión para garantizar la máxima calidad de los electrodos laminados. Los defectos en las superficies de laminación y las pequeñas desviaciones de concentricidad influyen directamente en el grosor y la calidad de la lámina de electrodo. Por lo tanto, la supervisión del desgaste de las superficies de los rodillos de la calandra y de la concentricidad es de suma importancia.
Nuestros sensores permiten registrar estas características de calidad. Se reconocen las desviaciones más pequeñas de la concentricidad y se detectan los arañazos más diminutos en las superficies de los rodillos.
Como las fuerzas del rodillo sólo actúan sobre la parte revestida del electrodo durante el calandrado, pero no sobre las zonas de los bordes no revestidas, pueden formarse arrugas en la lámina de la batería.
Las arrugas, también conocidas como "espiguillas", están causadas por tensiones residuales en el material. Son un defecto grave en la producción de electrodos, que puede tener un impacto significativo en los procesos de fabricación posteriores. Por ejemplo, pueden introducirse más tensiones en el material durante el bobinado posterior, lo que puede provocar una fisura en el electrodo.
Nuestra tecnología de sensores puede detectar las arrugas y medir su tamaño. Si son demasiado grandes, se rechaza el material. La formación de arrugas también puede reducirse ajustando los parámetros de enrollado, como aumentando la temperatura de los rodillos de calendario o incrementando la tensión de la banda.
La lámina separadora separa las dos láminas de electrodos, es decir, el ánodo y el cátodo, y evita así cortocircuitos. Las láminas separadoras deben ser eléctricamente aislantes, por lo que suelen estar hechas de plásticos porosos, a veces de varias capas, como polipropileno o polietileno. Estas láminas tienen un grosor de entre 15 y 25 µm y no deben ser dañadas por partículas extrañas. Si se perfora la película separadora, se produce un cortocircuito y el riesgo de ignición es elevado. (embalamiento térmico).
Con nuestros sensores, podemos medir el grosor y la integridad de las películas separadoras y también resolver el grosor de las capas individuales.
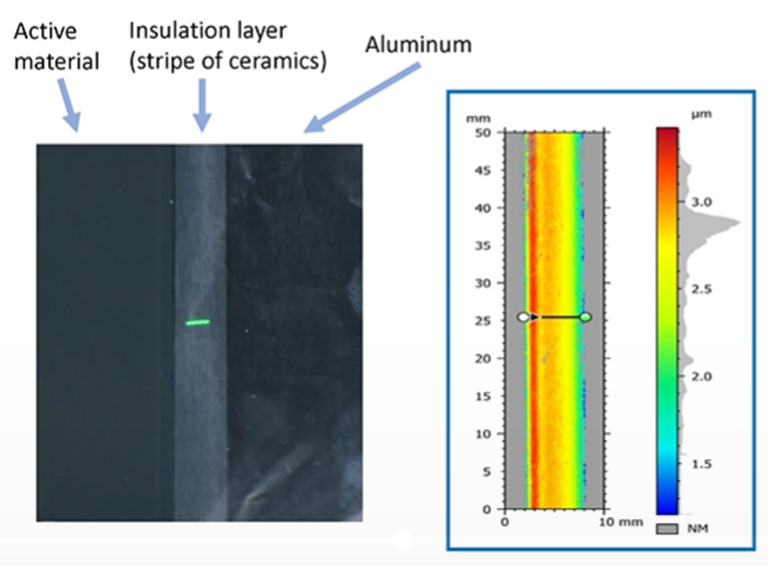
Para mejorar la seguridad de las pilas, a veces se aplica una capa aislante al electrodo. Consiste en una tira de cerámica que se aplica junto al material activo.
La razón es que los separadores de polipropileno se contraen a temperaturas de 110°C e incluso se funden a 150°C y más. La tira cerámica evita el riesgo potencial de cortocircuito entre el cátodo y el ánodo, aumentando así la seguridad de la célula.
Los espesores estándar en el mercado de la capa aislante se sitúan entre 3 y 10 µm. Para obtener la mejor calidad y una producción eficiente, estos espesores se miden en línea en procesos rollo a rollo, incluso a altas velocidades de banda de hasta 150 m/min. Por ejemplo, se puede visualizar el perfil de espesor del óxido de aluminio (Al2O3) y detectar defectos. Se detecta un posible hueco entre el material activo y la banda cerámica, y también puede visualizarse un solapamiento de la cerámica sobre el material activo.
Soluciones para sus fases de fabricación en la producción celular
Precitec ha desarrollado la solución denominada "corte por láser asistido por gas en una bobina cortada" para el corte recto de la lámina del electrodo. Este innovador método garantiza una calidad de corte elevada y constante al guiar la lámina con precisión durante el proceso y minimizar las vibraciones. Al cortar directamente sobre el rollo, el tamaño del punto láser se reduce y la potencia media del láser disminuye, lo que minimiza significativamente la zona afectada por el calor (HAZ) y mejora la calidad general del corte.
El corte por láser asistido por gas también ofrece un proceso más limpio y eficaz. Las partículas y residuos generados durante el corte se canalizan hacia el rodillo de corte y se eliminan de forma segura mediante un sistema de extracción integrado, evitando así la contaminación del sistema de corte por láser.
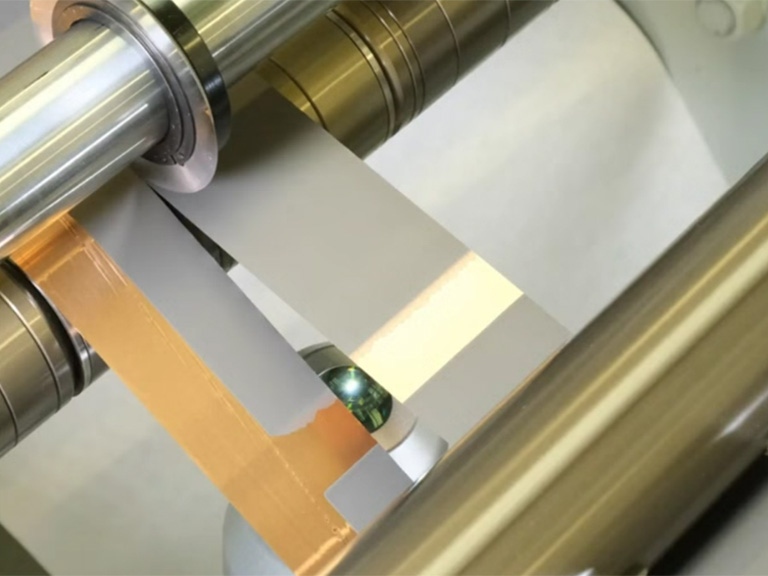
Si se perfora el separador, se produce un cortocircuito y existe un alto riesgo de ignición (fuga térmica). Los separadores suelen tener un grosor de aprox. 20 µm. Por lo tanto, es extremadamente importante detectar rebabas de aprox. 10 µm.
La medición de las rebabas puede mostrar la geometría y la forma de las láminas metálicas, así como la topografía del revestimiento, incluida la lámina metálica subyacente. Se utilizan diversas técnicas para medir las rebabas desde abajo o desde el lateral, en función de la tarea y los requisitos. Integrado en un sistema rollo a rollo, detectamos las rebabas de forma fiable y proporcionamos información sobre la calidad de la cortadora rebobinadora (mantenimiento predictivo) o del corte por láser.
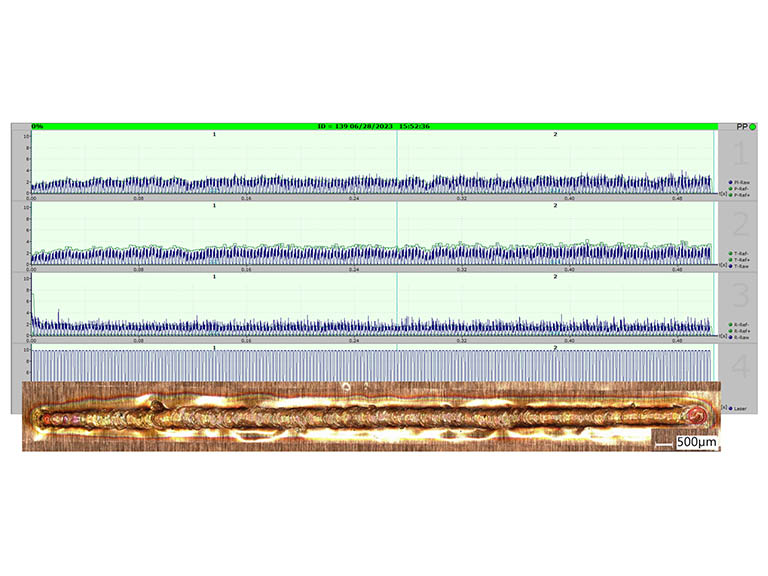
Las baterías están formadas por varias capas de finas láminas de cobre y aluminio (5 - 10 µm), que deben soldarse entre sí para producir una batería estable y potente. Normalmente se sueldan entre 60 y 100 láminas. En función de la capacidad y el rendimiento deseados para la batería, se apilan varias de estas capas.
Además de la sujeción precisa de la pila de láminas, también es importante una estrategia de soldadura inteligente al soldar la pila de láminas. Esto permite realizar una conexión segura de la primera a la última lámina con poca distorsión y sin quemaduras. El uso de sistemas de supervisión del proceso permite detectar las anomalías de soldadura y las desviaciones más pequeñas para garantizar la calidad y fiabilidad del cordón de soldadura. En última instancia, esto se traduce en un mayor rendimiento de la producción y una mejor calidad del producto.
En la soldadura láser de tapa a lata, se suelda una tapa metálica (tapón) a un recipiente metálico (lata). Este tipo de soldadura láser se utiliza a menudo en la producción de baterías para aislar los electrolitos del mundo exterior y evitar la fuga de líquidos. Los materiales utilizados son aluminio o acero niquelado.
La soldadura láser cap-to-can se utiliza tanto para pilas cilíndricas como prismáticas. En ambos casos, la calidad del cordón de soldadura es de vital importancia para el rendimiento y la fiabilidad de la batería.
Con pilas de gran tamaño, como la 4680, la redondez de la lata no siempre está garantizada al 100%. Sin embargo, es esencial para la estanqueidad del cordón de soldadura que el haz láser se guíe a lo largo del contorno de la lata. El contorno real puede medirse con precisión y rapidez con el ScanMaster y el rayo láser puede ajustarse en consecuencia. De este modo se consiguen cordones de soldadura de alta calidad sin necesidad de soldar en la cubeta.
Un defecto típico de la soldadura láser de tapón a lata es el llamado pinhole, que puede provocar fugas en la unión soldada. Los agujeros de alfiler grandes pueden detectarse como una anomalía de la soldadura con el monitor de soldadura láser. Los defectos más pequeños del cordón de soldadura se reconocen en el postproceso midiendo la topografía del cordón de soldadura. A continuación, la célula puede volver a trabajarse, lo que reduce el número de rechazos.
Durante el montaje de la celda de la batería, el electrolito se rellena de manera uniforme y completa en el interior de la celda y se distribuye para garantizar un rendimiento óptimo. Los residuos de electrolito en el exterior de las celdas de la batería perjudican la seguridad del producto. Cuantas más baterías se producen, más urgente es la necesidad de detectar y eliminar automáticamente las zonas contaminadas en el lado de llenado de la celda de la batería en la línea de producción. En el proceso posterior, conocido como soldadura de pasadores de sellado, la abertura de llenado de las celdas cilíndricas o prismáticas se suelda herméticamente mediante láser. Los residuos de electrolito afectan a la calidad del cordón de soldadura y pueden provocar fugas o una contaminación importante por salpicaduras de soldadura. En ese caso, la célula tendría fugas y sería rechazada.
Después de llenar la célula de la batería con el electrolito, la abertura de llenado se cierra con una tapa y se suelda herméticamente con luz láser. Esto sella la célula e impide que el electrolito salga. La célula queda así sellada.
La soldadura de las celdas de la batería es un paso crítico del proceso, ya que se trata de una soldadura estanca. Si la célula tiene fugas, se rechaza. La contaminación o las salpicaduras pueden provocar pequeñas fugas en el cordón de soldadura. Por lo tanto, la soldadura precisa y exacta del pasador de sellado es de gran importancia para garantizar que la célula permanezca sellada y no pueda escapar electrolito. El objetivo es conseguir costuras estancas y sin distorsiones con un aporte de calor bajo y localizado. Cada soldadura individual puede supervisarse, evaluarse y documentarse en línea. Nuestros sistemas reconocen las irregularidades y las soldaduras defectuosas. Esto garantiza la trazabilidad y transparencia de sus procesos al 100%.
Diferentes tipos de células para diferentes aplicaciones
En la e-movilidad se utilizan generalmente tres tipos de baterías de iones de litio. Las baterías funcionan según el mismo principio funcional y tienen una alta densidad energética para garantizar una gran autonomía. Se utilizan pilas de tipo bolsa, prismáticas y cilíndricas, que se conectan para formar módulos de baterías con el fin de proporcionar la energía necesaria. Pero, ¿en qué se diferencian estos tipos de pilas?
Otros campos de aplicación de la movilidad eléctrica
Pila de combustible
Una pila de combustible consta de numerosas placas bipolares que deben soldarse de forma estanca al gas. En la mayoría de los casos, las velocidades de soldadura son muy elevadas, al igual que los requisitos de calidad del cordón de soldadura. Además, los parámetros geométricos de las placas bipolares deben mantenerse con precisión para garantizar un alto rendimiento de la pila de combustible. Nosotros los medimos con nuestros sensores de tecnología de medición 3D.
Transmisión
La cadena cinemática eléctrica está formada, entre otros elementos, por el estator, el rotor y la electrónica de potencia. Los alambres de horquilla bien pelados son cruciales para la soldadura láser de alta calidad de estatores (soldadura de horquilla). Podemos detectar residuos de esmalte en los alambres y permitir procesos de soldadura láser adaptables.