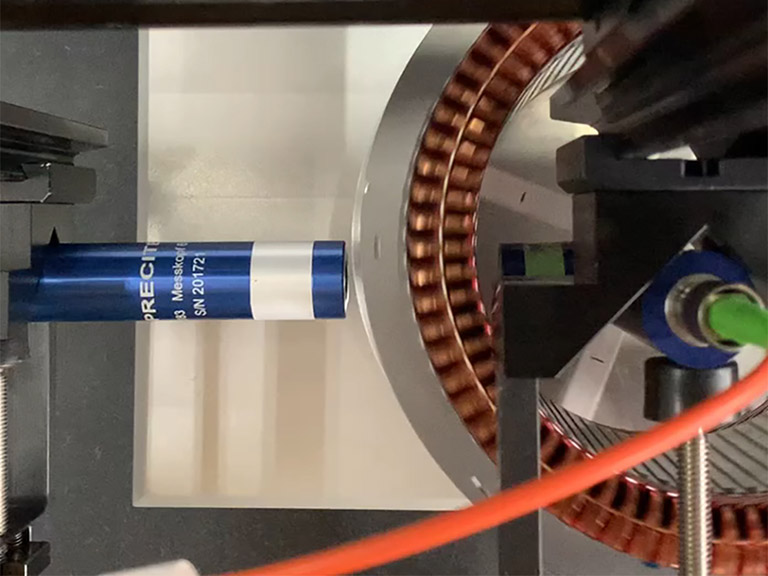

Medición de precisión y soluciones adaptativas para la producción de estator de alta calidad en la cadena cinemática
Las baterías o las pilas de combustible proporcionan la energía. La cadena cinemática se encarga del movimiento de las ruedas. La cadena cinemática puede dividirse en el motor eléctrico, compuesto por el estator y el rotor, y la electrónica de potencia. Nuestros productos se utilizan en numerosas fases de la producción, sobre todo en la fabricación de estatores.
Por ejemplo, el grosor de las capas esmaltadas de los hilos de cobre se mide en línea y directamente después del desenrollado. La detección de residuos de esmalte tras el decapado y antes de la soldadura por láser también es crucial para una alta calidad de la soldadura por láser. Esto se debe a que si aún quedan restos de pintura, éstos se funden durante la soldadura láser y pueden provocar la formación de poros. En ese caso, ya no pueden garantizarse las secciones transversales de unión requeridas.
Sin embargo, la soldadura láser también requiere soluciones innovadoras. Los pivotes a soldar pueden tener alturas diferentes, los pivotes individuales pueden estar torcidos en el plano y puede haber huecos entre los pivotes. Los pasadores pueden cortarse de forma diferente y los reflejos del dispositivo de sujeción también juegan su papel. Para hacer frente a estos retos, hemos personalizado nuestros productos para adaptar el proceso de soldadura láser rápidamente y en cualquier momento: para la máxima calidad en la producción de estátores.
Soluciones para sus fases de producción de estator de alta calidad en la cadena cinemática
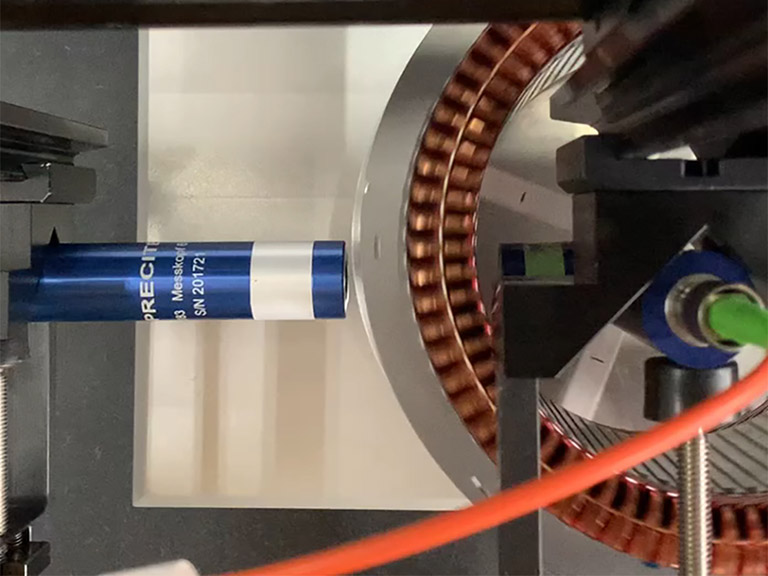
Medir el grosor de la capa de alambres de horquilla de cobre, detectar grietas en las lacas de las horquillas, controlar el decapado por láser y detectar residuos de laca tras el decapado son tareas de inspección fundamentales para la producción de estatores y bobinas enchufables de horquilla. Las elevadas propiedades eléctricas de las bobinas enchufables son un factor clave que debe tenerse en cuenta a la hora de seleccionar la tecnología de medición.
Es importante comprobar si el recubrimiento de esmalte es lo suficientemente grueso como para evitar cortocircuitos o no se agrieta durante el doblado del molde, asegurarse de que los recubrimientos están libres de agujeros de alfiler o burbujas, detectar el desconchado, comprobar los residuos de recubrimiento después del desencofrado y evaluar la forma de las costuras de soldadura en el núcleo laminado.
Precitec tiene exactamente la solución adecuada para cada una de estas tareas específicas:
- Nuestro sensor de línea CHRocodile CLS 2Pro es ideal para detectar cualquier agujero y ampolla a altas velocidades de inspección. Cubre amplias zonas en una sola medición (hasta 20 mm de longitud de línea) y puede detectar incluso los defectos más pequeños.
- Nuestro Flying Spot Scanner 310 detecta residuos en toda la anchura del alambre y mide con precisión el grosor del revestimiento protector, hasta 2 µm.
Proporciona mediciones rápidas a velocidades de hasta 70 kHz.
- Nuestras CHRocodile 2K y CHRocodile 2 IT son ideales para medir con precisión y eficacia el grosor de una amplia gama de revestimientos en las cuatro superficies alrededor de la bobina. Ambos dispositivos utilizan sondas puntuales que permiten realizar mediciones precisas de alta velocidad del espesor de revestimientos, hasta espesores de 2 µm, con una velocidad de medición de hasta 70 kHz.
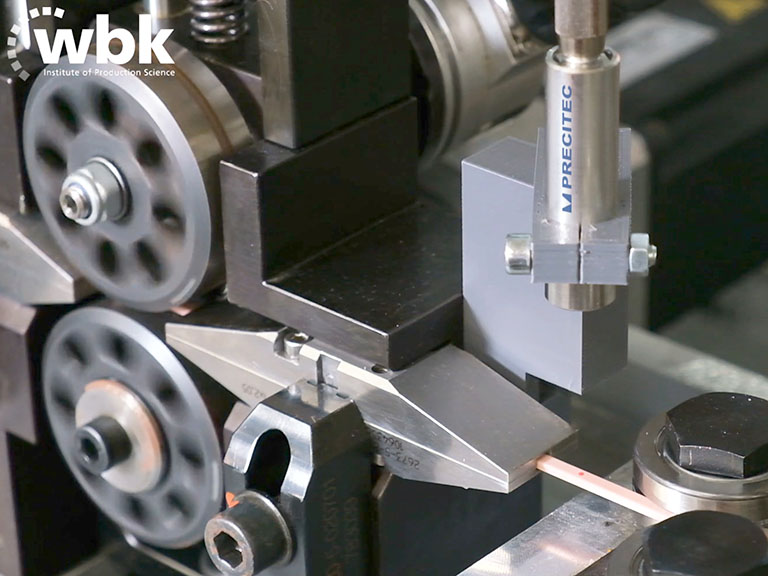
La tecnología de horquillas es un componente central de la producción moderna de estátores para electromovilidad. En este proceso, los alambres de cobre doblados, conocidos como horquillas, se recubren con una capa aislante de polímeros. El grosor de este revestimiento desempeña un papel decisivo en el proceso de producción.
Si es demasiado fino: aislamiento eléctrico insuficiente, mayor riesgo de cortocircuitos
Si es demasiado gruesa: problemas durante el procesamiento, riesgo de fallos en el sistema de producción
Nuestros sensores CHR Mini y CHR 2 IT de alta precisión permiten medir el grosor del revestimiento al 100% en línea, sin tiempos de ciclo y directamente en la línea de producción. Gracias a esta medición en tiempo real, los alambres con un recubrimiento demasiado fino pueden reconocerse en una fase temprana y expulsarse del proceso antes de que se instalen en el estátor. Esto no sólo garantiza la calidad de los componentes fabricados, sino que también aumenta la eficacia de todo el sistema de producción. Además, la documentación completa de los resultados de las mediciones permite una trazabilidad total de cada alambre de horquilla.
La producción en serie de motores eléctricos de tracción para la tecnología de propulsión electromóvil debe ser flexible y posible en grandes cantidades. Esto requiere sistemas de fabricación de alta precisión y procesos estables.
En la producción de las denominadas horquillas, los alambres de cobre en forma de horquilla se insertan en ranuras, se retuercen y se sueldan con láser. La supervisión del proceso de soldadura del cobre permite obtener uniones soldadas reproducibles y de alta calidad con una buena conductividad. Se consigue una sección transversal de conexión elevada, una formación mínima de salpicaduras y la reducción de la formación de poros.
ScanMaster ofrece una atractiva solución de soldadura por escáner. Combina la medición de distancia de alta precisión a la pieza de trabajo (posición z), el enfoque automático (corrección z), una iluminación perfecta y, por tanto, el uso de un algoritmo rápido para la detección de la posición (posición x-y), así como la supervisión del proceso.
Otros campos de aplicación de la movilidad eléctrica
Célula de batería
Las celdas de las baterías están en el corazón de la electromovilidad y, por tanto, son cruciales para la seguridad, la vida útil y el rendimiento de los vehículos eléctricos. Nuestros productos para tecnología láser y tecnología de medición 3D permiten una innovación continua en la producción de baterías, reduciendo costes y aumentando el rendimiento de las celdas de batería.
Pila de combustible
Una pila de combustible consta de numerosas placas bipolares que deben soldarse de forma estanca al gas. En la mayoría de los casos, las velocidades de soldadura son muy elevadas, al igual que los requisitos de calidad del cordón de soldadura. Además, los parámetros geométricos de las placas bipolares deben mantenerse con precisión para garantizar un alto rendimiento de la pila de combustible. Nosotros los medimos con nuestros sensores de tecnología de medición 3D.