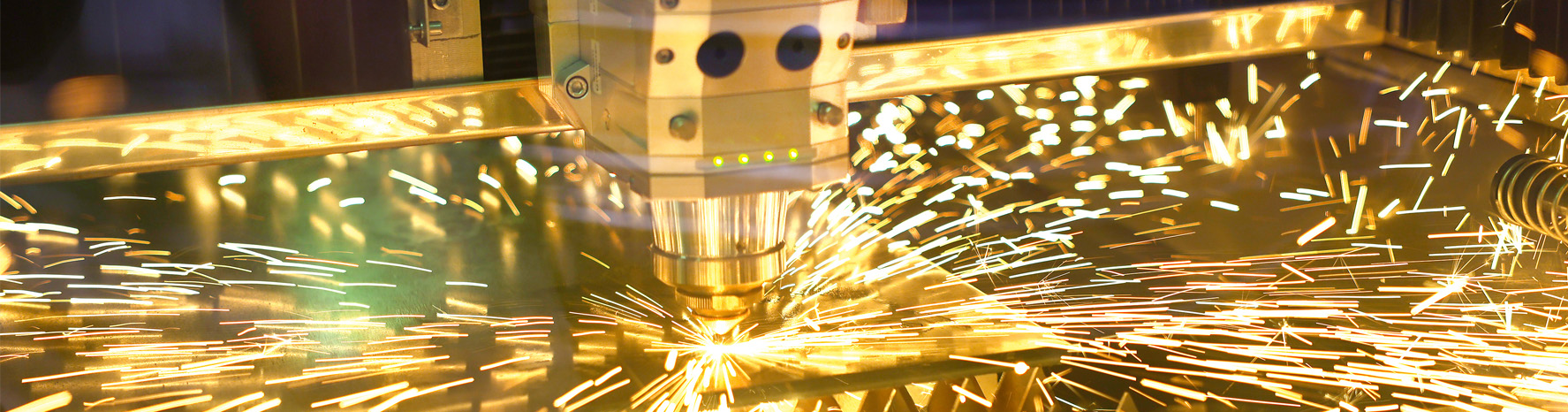
El futuro del procesamiento del metal: cómo el corte por láser de alto rendimiento está estableciendo nuevos estándares
Imagine una herramienta tan precisa que puede cortar metal con la delicadeza de un artesano experto, y con la potencia de miles de vatios. Esto no es una escena de una película futurista, sino la realidad de la tecnología láser de fibra en el corte de metales hoy en día. El desarrollo comenzó con láseres de fibra que inicialmente eran capaces de cortar una modesta chapa metálica de 3 mm de grosor, un avance que anunciaba una nueva era de eficiencia y versatilidad en la fabricación.
A medida que avanzaba la tecnología, era lógico aumentar aún más la potencia. El salto de cientos de vatios a varios kilovatios no fue sólo un cambio numérico, sino una revolución en el corte de metales. Al principio, las máquinas de 1 a 2 kW de potencia ya permitían cortar metales más gruesos, lo que parecía confirmar una correlación directa entre potencia y productividad. Pero cuando se superó el límite de 20 kW, se produjo un fenómeno fascinante: Una mayor potencia ya no conducía automáticamente a una mayor eficacia ni a la capacidad de cortar materiales aún más gruesos.
Es fundamental comprender que la potencia pura del láser no es el único factor en la capacidad de corte. Las aplicaciones del mundo real, desde las condiciones de laboratorio hasta las duras realidades de las instalaciones de producción industrial, demuestran que la clave está en una interacción bien ajustada entre la potencia de salida y la calidad de corte. A la hora de elegir un láser para el mecanizado de metales, es necesario tener en cuenta la denominada "reserva de potencia", es decir, seleccionar más potencia de la que parece necesaria a primera vista. Esta reserva no es por exceso, sino por flexibilidad para garantizar cortes de alta calidad para una amplia gama de materiales y condiciones.
La elección del gas - nitrógeno, oxígeno o una mezcla de gases - desempeña un papel decisivo en el proceso de corte, especialmente con metales diferentes como metales no férricos, acero inoxidable o chapa de hierro negro.
- El nitrógeno permite realizar cortes rápidos y limpios en metales más finos y supera claramente al oxígeno tanto en velocidad como en eficacia. Esto se debe a que el uso de oxígeno crea un corte mucho más ancho, lo que reduce la velocidad de corte.
- En cambio, la menor velocidad de corte del oxígeno es más adecuada para el hierro negro más grueso, ya que el menor coste del gas puede compensar la menor velocidad.
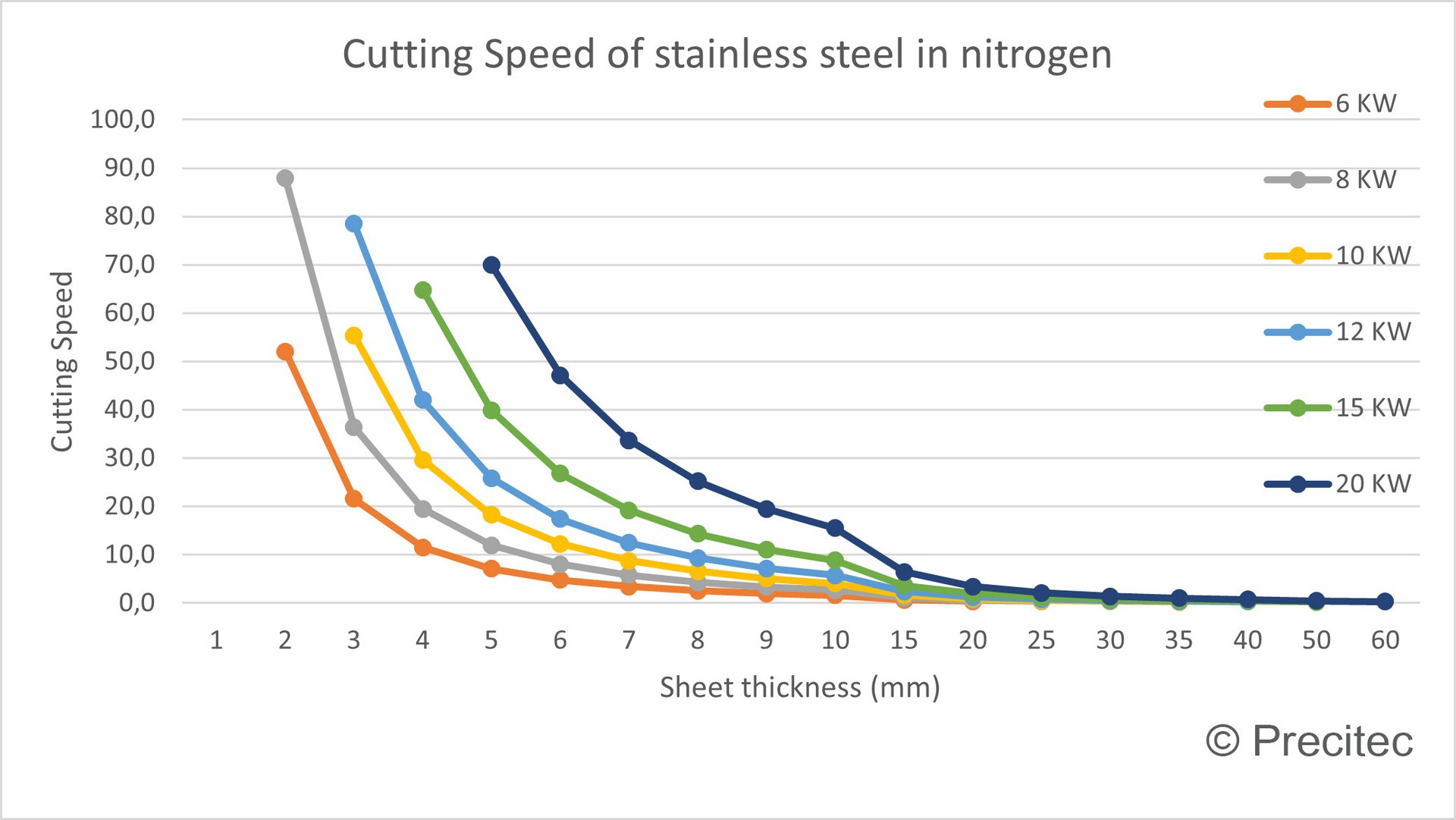
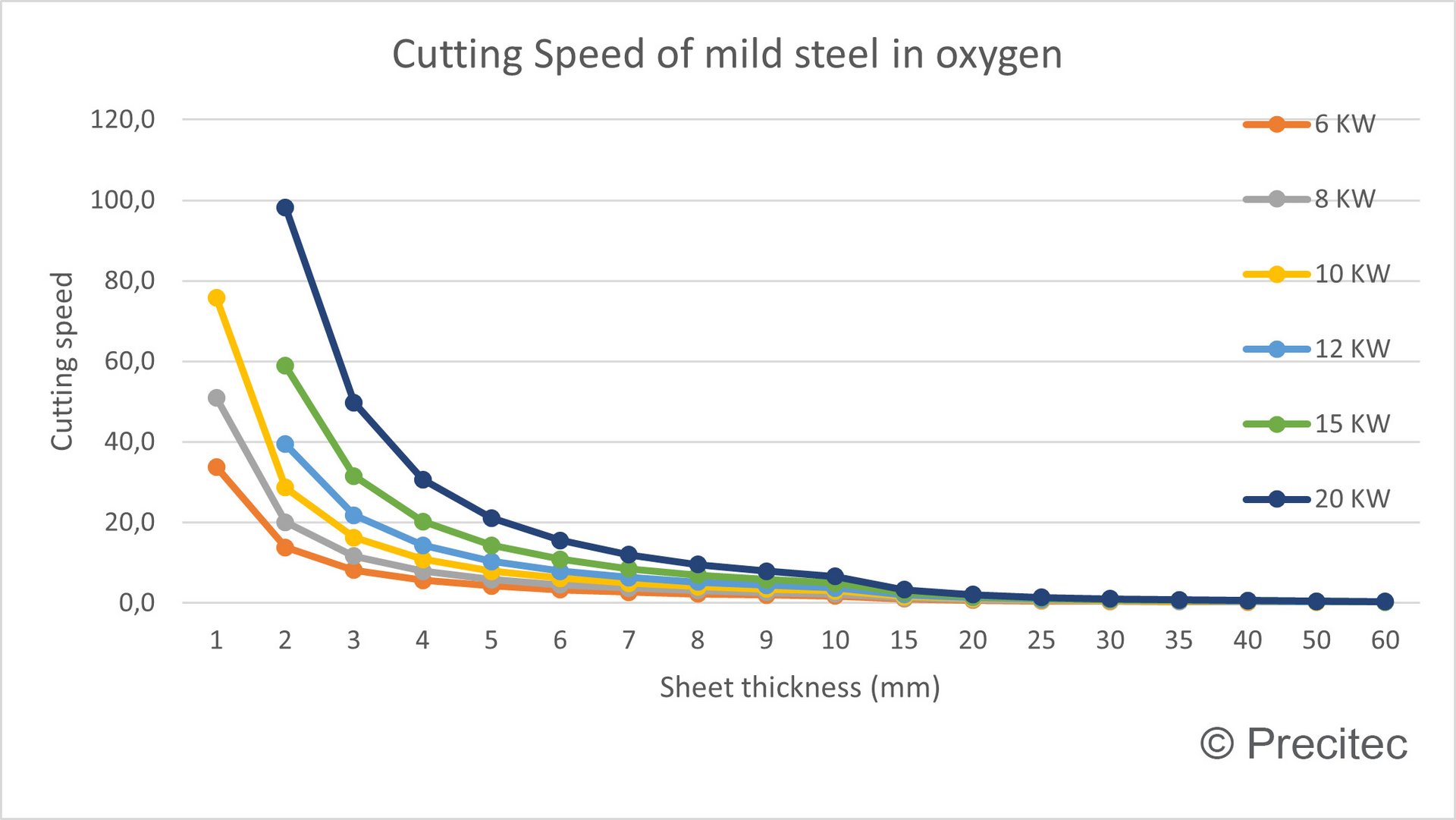
El gráfico muestra que el aumento de la potencia del láser tanto para el acero inoxidable con nitrógeno como para el acero dulce con oxígeno produce un aumento significativo de la velocidad de corte para determinados grosores de material y, al mismo tiempo, permite cortar materiales más gruesos.
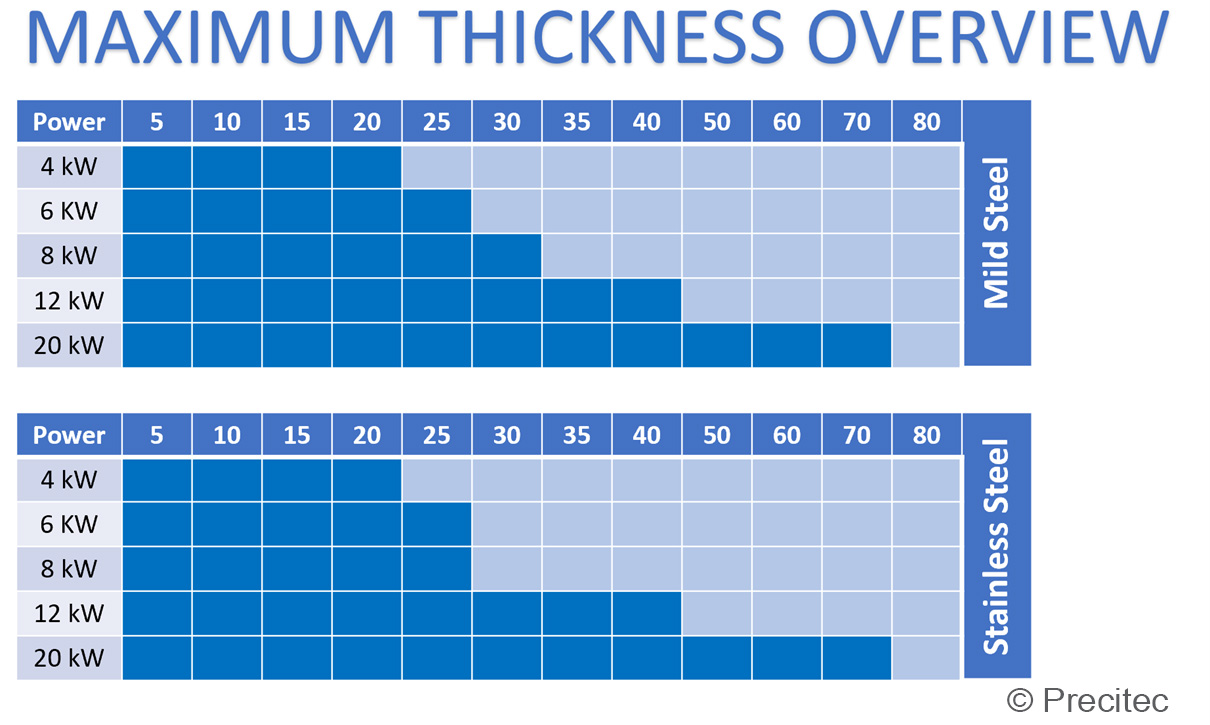
La tabla destaca el papel crucial de seleccionar el gas de apoyo adecuado para el corte por láser: El oxígeno mejora la velocidad y capacidad de corte del acero dulce, mientras que el nitrógeno garantiza cortes limpios y sin oxidación en acero inoxidable. La elección entre nitrógeno y oxígeno va más allá de la mera velocidad de corte y representa un equilibrio entre eficacia, coste y consideraciones medioambientales.
Aunque el corte con nitrógeno ofrece mayores velocidades y bordes más limpios, requiere una mayor presión de gas, lo que se traduce en mayores costes operativos. No obstante, las ventajas de una mayor eficacia y el coste relativamente inferior del nitrógeno pueden compensar estos costes, convirtiéndolo en la opción preferida para una amplia gama de aplicaciones.
El gráfico nos recuerda los numerosos factores que hay que tener en cuenta para un corte por láser eficaz y de alta calidad, como por ejemplo
- el tipo de acero
- el grosor
- la potencia del láser
- la elección del gas de soporte
Los datos muestran claramente que las potencias de salida más elevadas aportan ventajas significativas: desde cortar materiales más gruesos hasta alcanzar velocidades que antes se consideraban imposibles. Un láser de 3 kW puede atravesar una chapa de 15 mm de grosor, pero si se duplica la potencia a 6 kW se puede ampliar aún más esta capacidad, mejorando tanto el grosor como la velocidad de corte. Un fenómeno similar puede observarse con un aumento adicional de la potencia.
Como estamos en la cúspide de nuevos avances en tecnología láser, la atención no se centra sólo en la potencia. Se trata de comprender todo el ecosistema del corte por láser, desde las propiedades del material y los gases de corte hasta la eficiencia operativa y el impacto medioambiental. El futuro del procesamiento de metales pasa por invertir no sólo en mayores rendimientos de potencia, sino también en tecnologías más inteligentes y sostenibles que amplíen los límites de lo posible.