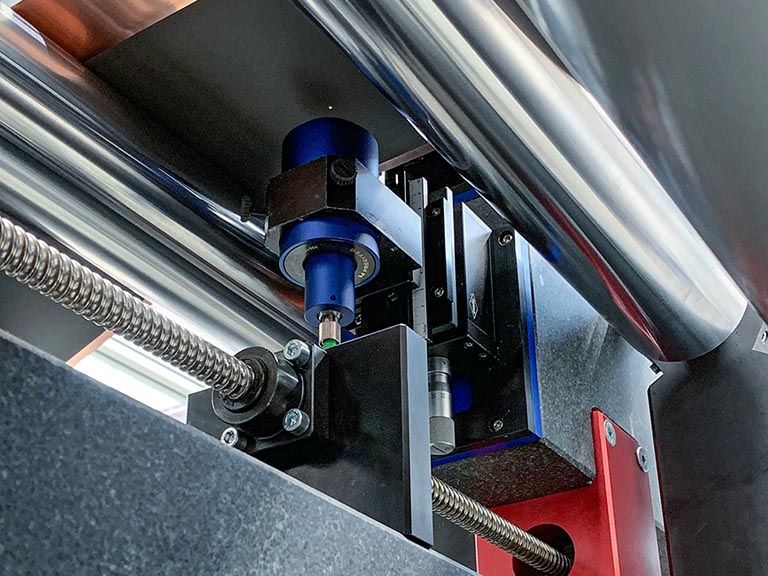
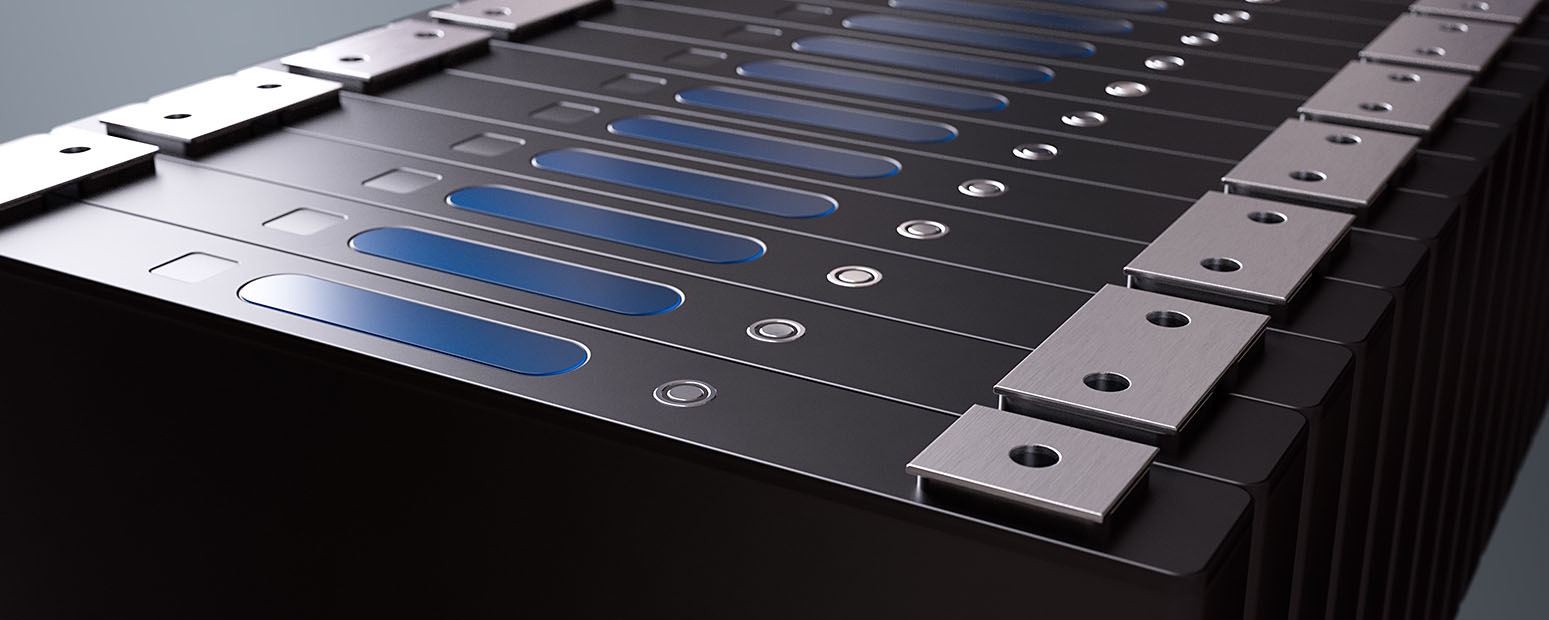
Des solutions efficaces pour la production de cellules de batteries lithium-ion
Dans le process de production d'électrodes, les cellules de batteries produites sont constituées de couches alternées de feuilles d'anode et de cathode. Elles sont séparées par ce que l'on appelle le séparateur. La pile de feuilles est ensuite enroulée, placée dans un boîtier métallique et les batteries sont ensuite solidement soudées.
Nos systèmes de contrôle de la qualité sont utilisés à de nombreuses étapes du processus afin de garantir une production efficace des cellules de batterie. Il s'agit par exemple de mesurer l'épaisseur de la feuille d'électrode, de contrôler la bavure de coupe et de souder au laser les couches de feuilles (feuille à onglet) et le boîtier cylindrique avec son couvercle (cap to can).
L'exigence du client est clairement la précision : < 1 micromètre. Nos capteurs répondent à cette exigence et sont optimisés pour les challenges des environnements de production de cellules de batteries, ce que l'on appelle les applications "roll-to-roll" :
vitesses de roulement de bandes élevées
vibrations des feuilles d'électrodes
surfaces brillantes et noires
Dans la technologie laser, le soudage laser cap-to-can est une application cruciale. L'objectif est ici de détecter les trous d'épingle ou, au mieux, de les éviter complètement. Nous avons optimisé nos produits et nos optiques spécifiquement pour ces applications et développé des solutions innovantes.
![[Translate to Französisch:] Produktionskette Batterieproduktion bestehend aus Zell- und Modulproduktion Chaîne de production de batteries comprenant la production d'électrodes et de cellules](/fileadmin/landingpages/Prozesskette_E-Mobility_WEB/Productionchain_E-Mobility_Electrode_Cell_Production.jpg)
Solutions pour vos étapes de fabrication d'électrodes
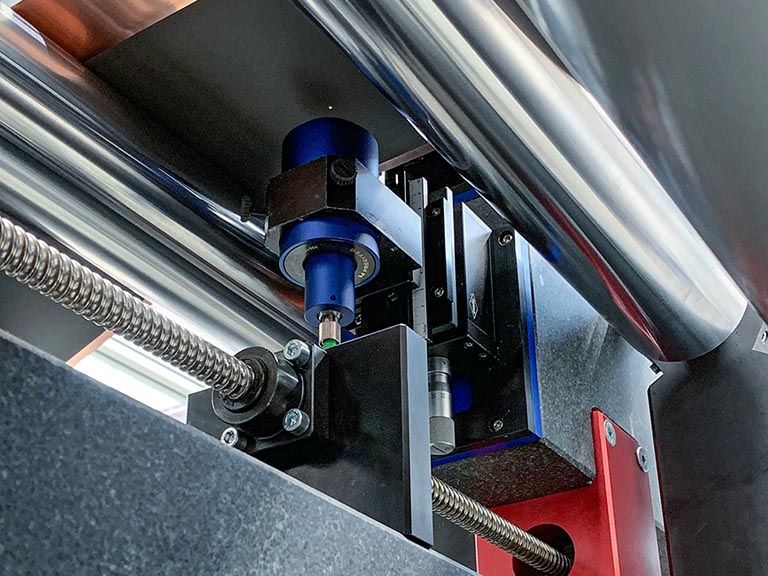
L'épaisseur exacte du revêtement des feuilles d'électrodes joue un rôle essentiel, car elle a une influence significative sur les performances et la durée de vie des batteries. Dans le processus de production, la feuille support est d'abord enduite de suspension, soit en continu ou par intermittence, puis le solvant est éliminé de la couche dans le four de séchage.
Des mesures d'épaisseur sont effectuées avant et après le processus de séchage. Le revêtement peut être sec ou humide - nos mesures sont toujours exactes, que la surface soit réfléchissante, noire ou poreuse. Les effets des vibrations et de la vitesse de la bande sont compensés. L'ondulation et l'épaisseur du film sont analysées avec précision et les résultats sont affichés. Les exigences actuelles du marché sont une précision absolue de < 1 µm en combinaison avec une répétabilité de ± 0,5 µm.
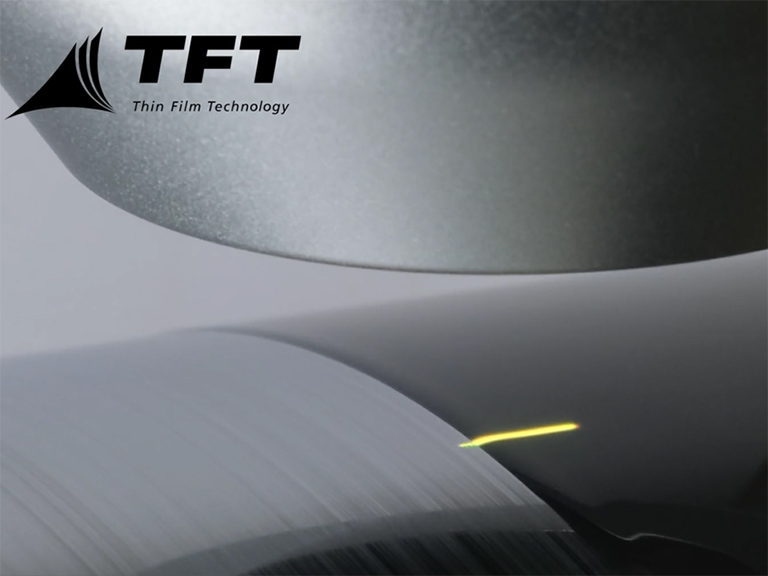
La surélévation des bords qui peut se produire lors de l´application de la suspension peut avoir un effet négatif sur le traitement ultérieur de l'électrode, en particulier lors de l'enroulement. Elle peut conduire à un enroulement asymétrique et donc à d'importants problèmes de manipulation.
Pour améliorer les performances des cellules de batterie, des efforts sont faits pour augementer l´épaisseur du revêtement. Cependant, les revêtements plus épais ont également tendance à former des surélévations sur les bords.
Notre capteur de ligne permet de mesurer avec précision la hauteur du bord sur une longueur allant jusqu'à 20 mm, cela même lors du processus de fabrication. La mesure est possible, que le bord soit sec ou humide. La vibration de la feuille est prise en compte lors de cette mesure. Les transitions entre les feuilles porteuses métalliques miroitantes et le revêtement sombre sont reconnues avec une grande précision.
Lors d´un dépôt intermittent, ce que l´on appelle le start/stop va provoquer une différence de la hauteur du revêtement. Dans ce processus, le dépôt est appliqué en alternance sur la feuille de support ou délibérément évité. Les hauteurs de marche ainsi produites constituent un défi pour ce type de revêtement et doivent être surveillés pour garantir la longévité et la sécurité de la cellule de batterie.
Nos capteurs point permettent de mesurer avec précision le profil topographique et donc de détecter tôt et avec précision les éventuels défauts dans le revêtement.
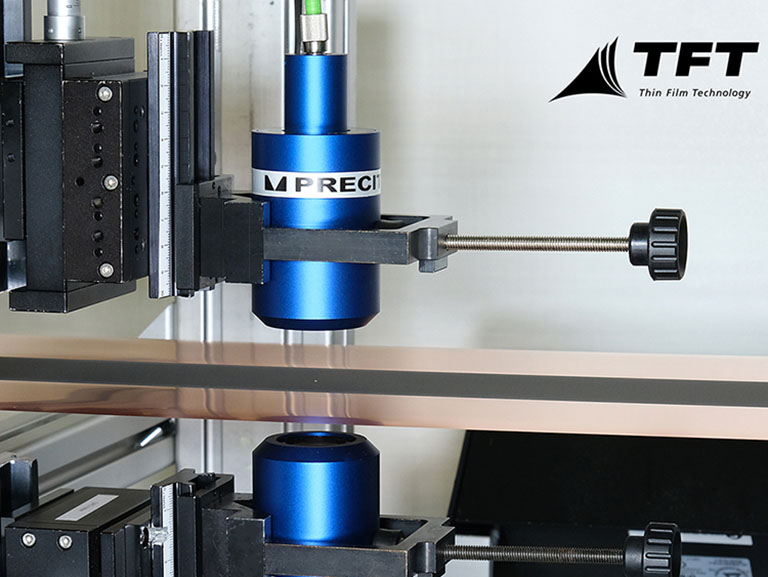
L'épaisseur exacte du revêtement des feuilles d'électrodes joue un rôle essentiel, car elle a une influence significative sur les performances et la durée de vie des batteries. Dans le processus de production, la feuille de support est d'abord recouverte en continu de slurry, puis le solvant est éliminé de la couche lors de son passage dans le canal de séchage. Pour garantir une forte adhérence du slurry sur le film, il est essentiel de garantir les cinq étapes du séchage. Par exemple, la migration du liant doit être évitée. Pour un séchage optimisé, le temps necessaire pour que les pores se vident est également crucial.
Nos capteurs permettent d'identifier ces moments clés du séchage. Cela permet de réduire la durée du séchage, d'optimiser la qualité du revêtement et de réduire les coûts énergétiques.
Des mesures d'épaisseur précises peuvent également être effectuées pendant tout le processus de séchage. Qu'il s'agisse de couches humides ou sèches, de graphite noir ou poreux ou de matériau actif de cathode, le résultat de la mesure reste précis. Les effets des vibrations et de la vitesse de la bande sont compensés pendant la mesure. L'utilisation des capteurs permet de réduire la durée du séchage, d'optimiser la qualité du revêtement et d'économiser de l'énergie.
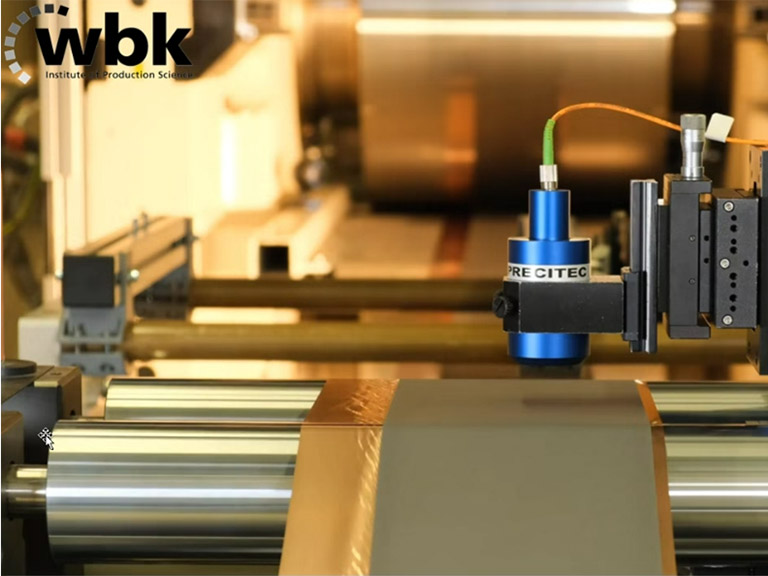
Le calandrage est la dernière étape de la production de l'électrode. C'est là que l'épaisseur finale et la porosité du revêtement sont essentiellement déterminées. Outre le poids par unité de surface, ces caractéristiques sont décisives pour la performance et la sécurité de la cellule de la batterie.
Nos capteurs permettent une mesure complète du processus de calandrage. L'épaisseur de l'électrode avant et après le calandrage, la concentricité des rouleaux de calandrage et les "winkles" sont mesurées. Ce sont des rides en bordure du revêtement sur le substrat. Les vibrations des feuilles sont compensées par nos capteurs et l'ondulation est calculée. Cela signifie que des mesures exactes peuvent être effectuées à tout moment, même à des vitesses de bande élevées de 100 à 150 m/min.
Les rouleaux de calandre sont des rouleaux en acier massif d'un diamètre supérieur à 1 m. Les surfaces miroires sont lissées avec grande précision pour garantir la meilleure qualité des électrodes laminées. Le moindre défaut de la surface de laminage ainsi que les petits écarts de concentricité ont une influence directe sur l'épaisseur et l'état de la feuille d'électrode. Le contrôle de l'usure des surfaces des cylindres de calandre et de la concentricité est donc de la plus haute importance.
Nos capteurs permettent d'enregistrer ces caractéristiques de qualité. Ils détectent les moindres écarts de concentricité et les moindres rayures sur la surface des cylindres.
En raison de la force de laminage et des différentes dilatations du revêtement et de la feuille, des plis (ou winkles) peuvent se former après le laminage. Ces plis se produisent en particulier au niveau du bord de la feuille conductrice par rapport au revêtement. Les plis compliquent considérablement les processus de production ultérieurs, voire les rendent impossibles.
Notre technologie de capteurs permet de détecter les plis et de mesurer leur taille. Si ceux-ci sont trop grands, le matériau est rejeté. La formation de plis peut également être réduite en ajustant les paramètres de laminage.
Le film séparateur sépare les deux feuilles d'électrode, c'est-à-dire l'anode et la cathode, et empêche ainsi les courts-circuits. Les films séparateurs doivent être électriquement isolantes et sont donc généralement constituées de plastiques poreux, parfois multicouches, tels que le polypropylène ou le polyéthylène. Ces films ont une épaisseur comprise entre 15 et 25 µm et ne doivent pas être endommagés par des particules étrangères. Si le film séparateur est pénétré, il y a un court-circuit et le risque d'incendie est élevé (emballement thermique).
Nos capteurs permettent de mesurer l'épaisseur et l'intégrité des films séparateurs et de déterminer l'épaisseur des différentes couches.
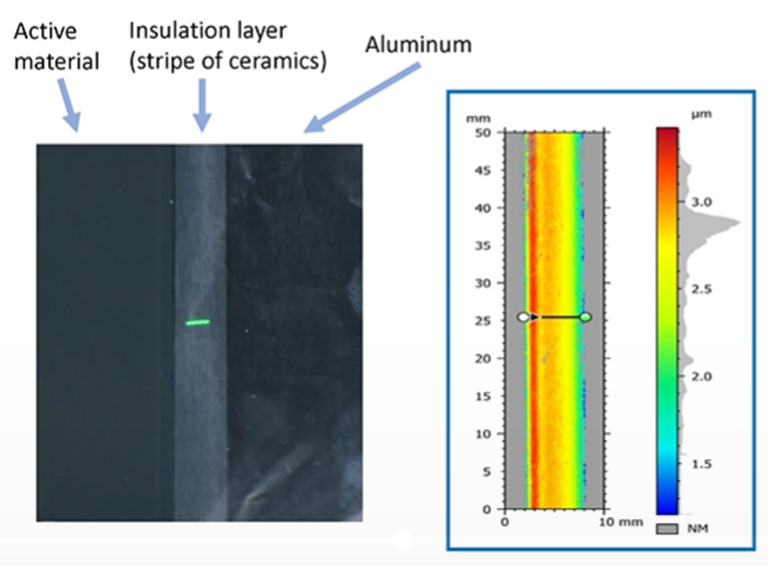
Pour améliorer la sécurité des éléments de batterie, une couche d'isolation est parfois appliquée sur l'électrode. Il s'agit d'une bande de céramique appliquée à côté de la matière active.
En effet, les séparateurs en polypropylène se contractent à partir de 110°C et fondent même à partir de 150°C. La bande de céramique empêche le risque potentiel de court-circuit entre la cathode et l'électrode. La bande de céramique prévient le risque potentiel de court-circuit entre la cathode et l'anode, augmentant ainsi la sécurité de la cellule.
Les épaisseurs standard de la couche d'isolation sont comprises entre 3 et 10 µm. Pour une qualité optimale et une production efficace, ces épaisseurs sont mesurées directement lors du calandrage, et même à des vitesses de bande élevées allant jusqu'à 150 m/min. Par exemple, le profil d'épaisseur de l'oxyde d'aluminium (Al2O3) peut être affiché et les défauts détectés. Un éventuel écart entre le matériau actif et la bande de céramique est détecté et un chevauchement de la céramique sur le matériau actif peut également être visualisé.
Solutions pour vos étapes de fabrication de cellules
Pour la découpe droite des feuilles d'électrode, Precitec a développé la solution dite de « découpe laser assistée par gaz sur rouleau rainuré ». Cette méthode innovante garantit une qualité de découpe constamment élevée en guidant avec précision le film pendant le processus et en minimisant les vibrations. La découpe directement sur le rouleau permet de réduire la taille du point laser ainsi que la puissance moyenne du laser, ce qui minimise significativement la zone affectée thermiquement (HAZ) et améliore la qualité de découpe globale.
La découpe laser assistée par gaz offre également un processus plus propre et plus efficace. Les particules et résidus générés lors de la découpe sont dirigés dans le rouleau rainuré, puis éliminés en toute sécurité via un système d’extraction intégré – évitant ainsi toute contamination du système de découpe laser.
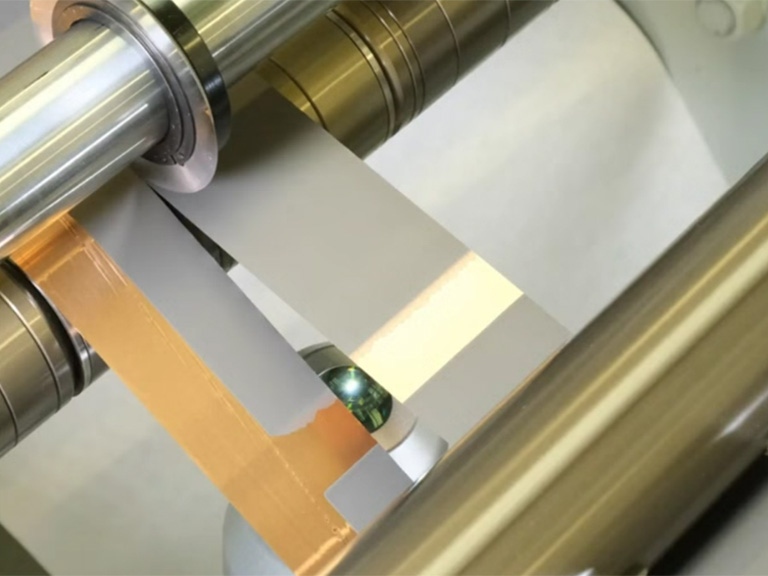
Si la feuille séparateur est endommagée, un court-circuit se produit et le risque d'incendie est élevé (emballement thermique). Les séparateurs ont généralement une épaisseur d'environ 20 µm. Il est donc extrêmement important de détecter les bavures d'environ 10 µm.
La mesure des bavures peut révéler la géométrie et la forme des feuilles métalliques ainsi que la topographie du revêtement, y compris la feuille métallique sous-jacente. Différentes techniques sont utilisées pour mesurer les bavures, soit par le bas, soit par le côté, en fonction de la tâche et des exigences. Intégrés dans la presse à rouleau, nos systèmes détectent les bavures de manière fiable et fournissent ainsi des informations sur la qualité de la découpeuse (maintenance prédictive) ou de la découpe au laser.
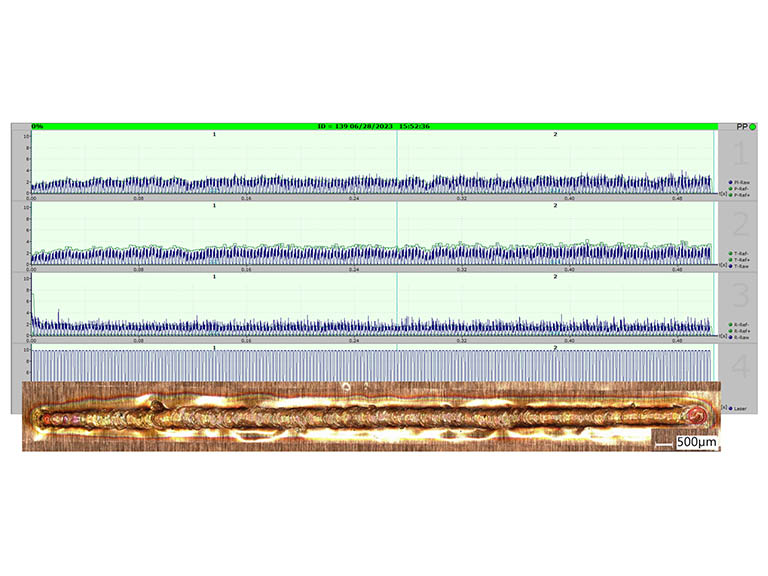
Les cellules des batteries sont constituées de plusieurs couches de fines feuilles de cuivre et d'aluminium (5 à 10 µm) qui doivent être soudées ensemble pour créer une batterie stable et puissante. En général, 60 à 100 feuilles sont soudées au cours du process. En fonction de la capacité et des performances souhaitées de la batterie, plusieurs de ces couches sont ensuite empilées les unes sur les autres.
Lors du soudage de la pile de feuilles, une stratégie de soudage intelligente est importante en plus d'un serrage précis de la pile de feuilles. Cela permet de réaliser une connexion sûre du premier au dernier film, avec peu de distorsion et sans brûlure. L'utilisation de systèmes de monitoring de process permet de détecter les anomalies de soudage et les moindres déviations afin de garantir la qualité et la fiabilité du cordon de soudure. En fin de compte, cela permet d'augmenter le rendement de la production et d'améliorer la qualité des produits.
Le soudage laser cap-to-can consiste à souder un couvercle métallique (cap) sur un récipient métallique (can). Ce type de soudage laser est souvent utilisé dans la production de batteries pour isoler les électrolytes du monde extérieur et éviter les fuites de liquides. Les matériaux utilisés sont l'aluminium ou l'acier nickelé.
Le soudage laser "cap-to-can" est utilisé pour les piles cylindriques, mais aussi pour les piles prismatiques. Dans les deux cas, la qualité de la soudure est cruciale pour les performances et la fiabilité de la batterie.
Dans le cas des éléments de batterie de grande taille, tels que le 4680, la circularité du boîtier n'est pas toujours parfaite. Cependant, il est essentiel pour l'étanchéité de la soudure que le faisceau laser soit guidé le long du contour du boitier. Le ScanMaster permet de mesurer exactement et rapidement le contour réel et d'ajuster le faisceau laser en conséquence. De cette manière, il est possible d'obtenir des soudures de haute qualité sans endommager le boitier.
Un défaut typique dans le soudage laser de couvercle à boitier est le trou d'épingle, qui peut entraîner des fuites dans le joint soudé. Les grands trous d'épingle peuvent être détectés comme une anomalie de soudage à l'aide du moniteur de soudage laser. Les plus petits défauts sur le cordon de soudure sont détectés en post-process en mesurant la topographie du cordon de soudure. Il est alors possible de retravailler la cellule, ce qui permet de réduire les déchets.
Lors de l'assemblage final de la batterie, l'électrolyte est versé et réparti uniformément dans le cylindre afin de garantir des performances optimales. Les résidus d'électrolyte à l'extérieur des cellules de batterie compromettent la sécurité du produit. Plus la production de batteries est importante, plus il est urgent d'automatiser la détection et l'éjection des zones contaminées au niveau du remplissage des cylindres dans la ligne de production. Dans le processus suivant, connu sous le nom de "seal pin welding", l'ouverture des cylindres est soudée au laser. Les résidus d'électrolyte influencent la qualité du cordon de soudure et peuvent entraîner des fuites ou une contamination considérable par les éclaboussures de soudure. La cellule serait alors non étanche et donc rejetée.
Après avoir rempli la batterie cylindrique avec l'électrolyte, l'orifice de remplissage est fermé par un couvercle et soudé de manière étanche à l'aide d'un laser.Cela permet de sceller la cellule et d'empêcher l'électrolyte de s'échapper. La cellule est ainsi scellée.
Le soudage des éléments de batterie est une étape critique du process, car il s'agit d'un soudage d'étanchéité. Si la cellule n'est pas étanche, elle est mise au rebut. Des impuretés ou des éclaboussures peuvent entraîner de minuscules fuites dans la soudure. Le soudage précis et ponctuel de la membrane d'étanchéité est donc très important pour garantir que la cellule reste étanche et qu'aucune fuite d'électrolyte ne se produise. L'objectif est d'obtenir des soudures étanches et sans distorsion avec un apport de chaleur faible et localement limité. Chaque soudure peut être contrôlée, évaluée et documentée en ligne. Nos systèmes détectent les irrégularités et les soudures défectueuses. La traçabilité et la transparence de vos processus sont assurées à 100 %.
Différents types de cellules pour différentes applications
Trois types de batteries lithium-ion sont généralement utilisés dans l'e-mobilité. Les batteries fonctionnent selon le même principe et ont une densité énergétique élevée pour garantir une longue autonomie. On utilise des cellules poche, des cellules cylindriques et des cellules prismatiques, qui sont ensuite connectées pour former des modules de batterie afin de pouvoir fournir la puissance nécessaire. Mais en quoi ces types de cellules diffèrent-ils ?
Autres champs d'application dans l'e-mobilité
Pile à combustible
Une pile à combustible se compose de nombreuses plaques bipolaires qui doivent être soudées de manière étanche aux gaz. Dans la plupart des cas, les vitesses de soudage sont très élevées, tout comme les exigences de qualité du cordon de soudure. En outre, les paramètres géométriques des plaques bipolaires doivent être maintenus avec précision pour garantir une performance élevée de la pile à combustible. Nous mesurons ces paramètres à l'aide de nos capteurs de la technologie de mesure 3D.
Groupe motopropulseur
La chaîne de traction électrique se compose entre autres du stator, du rotor et de l'électronique de puissance. Pour un soudage laser de haute qualité des stators (soudage de hairpin), il est essentiel que les fils soient bien dénudés. Nous pouvons détecter les résidus de vernis sur les fils et permettre des process de soudage laser adaptatifs.