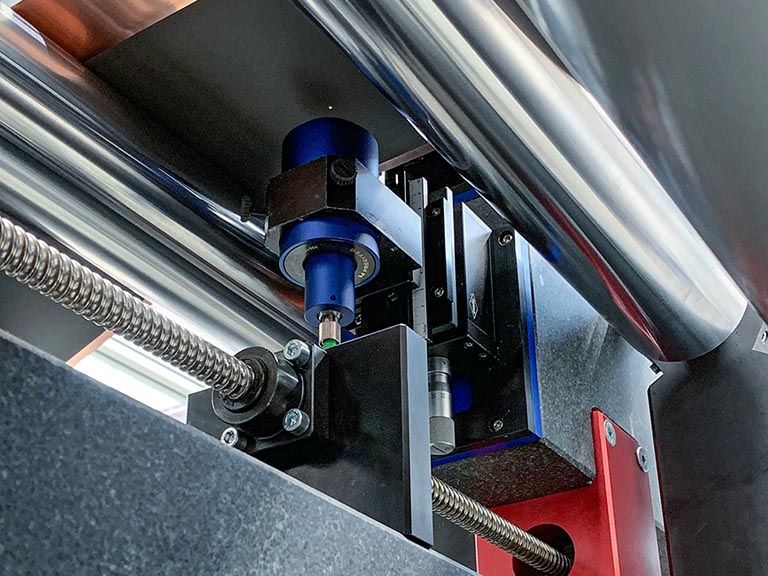
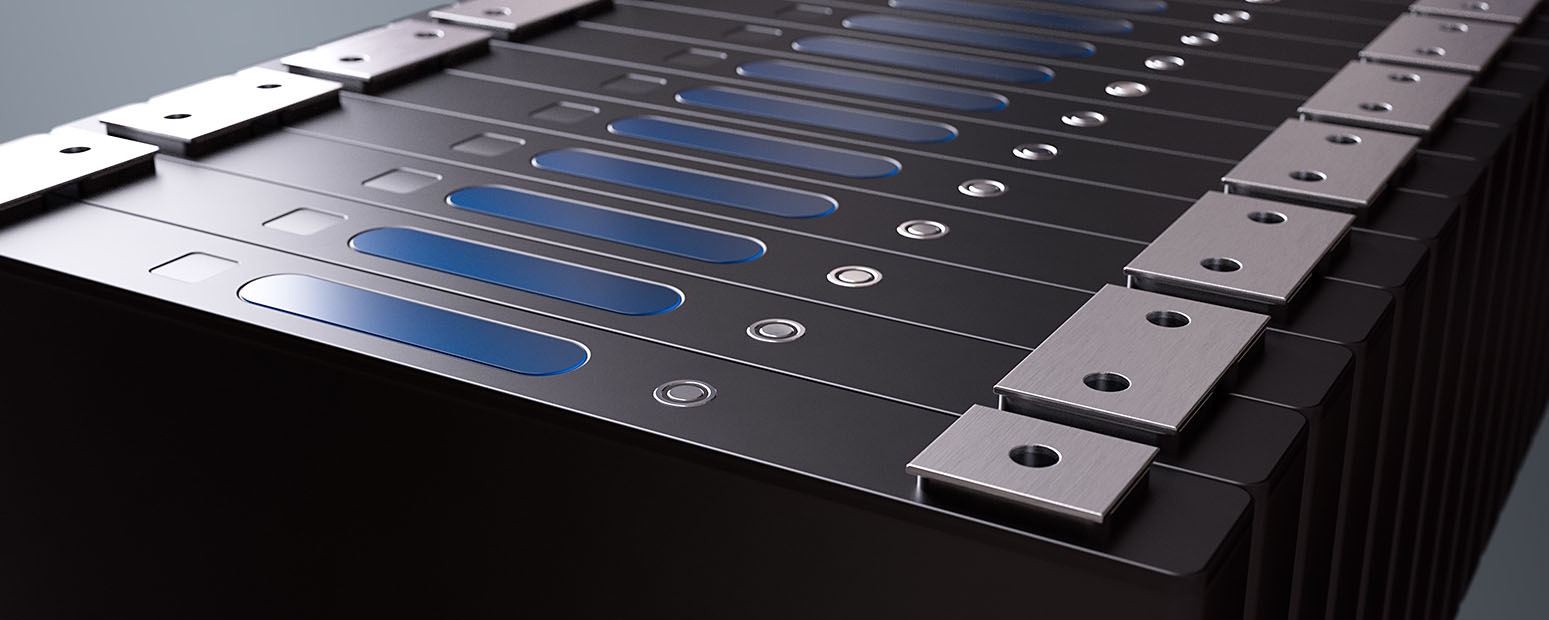
リチウムイオン電池セルの生産のための効率的なソリューション
電極の製造において、バッテリーセルは陽極ホイルと陰極ホイルを交互に重ねたもので構成されています。 これらはいわゆるセパレーターによって分離されています。 次に、ホイルを重ねたものを金属性のハウジングに入れ、電池本体をしっかりと溶接します。
当社の品質管理システムは、バッテリーセルの効率的な生産を保証するために、数多くの工程で使用されています。 例えば、電極ホイルの厚さの測定、切断バリのチェック、ホイルレイヤ(ホイルとタブ)および蓋とハウジング(キャップと缶本体)のレーザ溶接が含まれます。
当社のセンサーは、お客様からの明確なご要望である、精度1μm以下の要件を十分に満たしています。バッテリーセルの生産環境での、ロールトゥロールのアプリケーション向けに最適化されています。
- 高ウェブスピード
- 電極ホイルの振動。
- 暗色と光沢のある表面。
レーザ技術において、キャップと缶のレーザ溶接は重要なアプリケーションです。ここでの目的は、ピンホールを検出すること、最良な条件はピンホールを完全に回避することです。当社はこれらの用途に特化し、製品と光学系を最適化し、革新的なソリューションを開発しました。
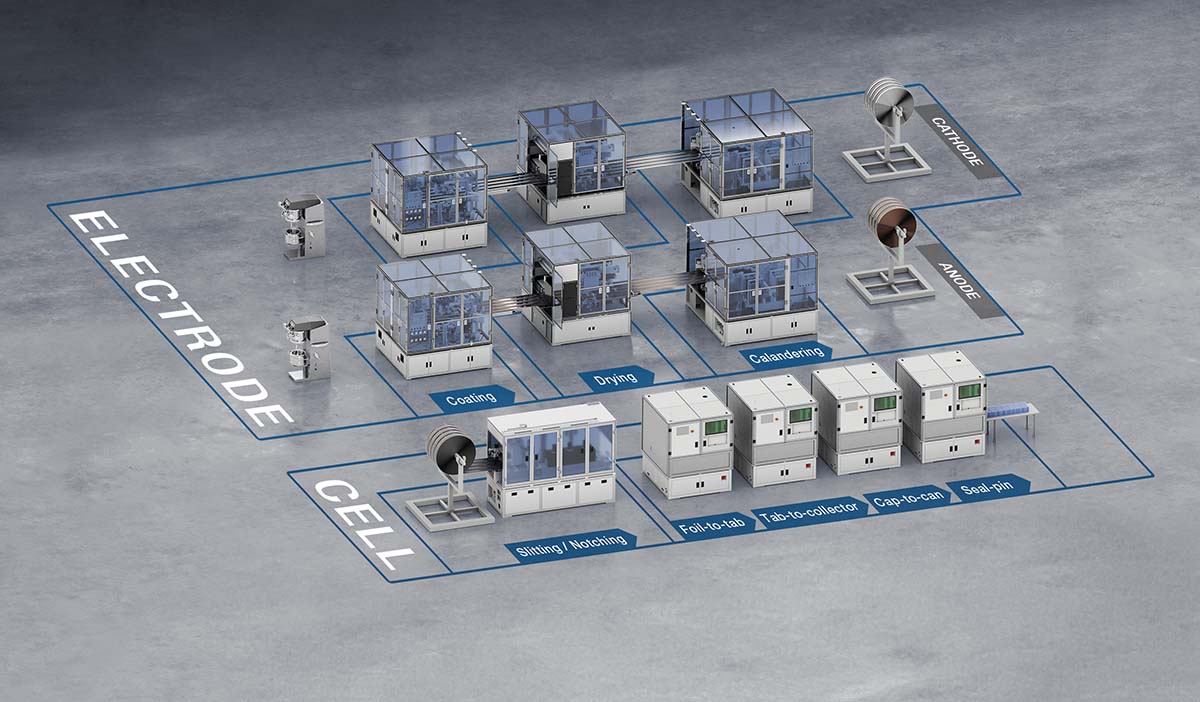
電極製造工程におけるソリューション
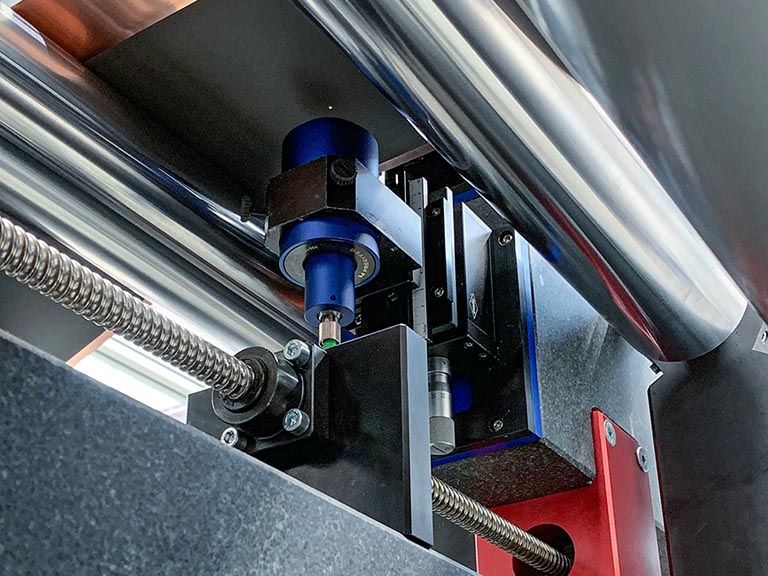
スロットダイとキャリア箔の間の正確な距離は、塗布の品質にとって必要不可欠であり、バッテリーセルの性能にとっても重要です。距離は通常 100 ~ 300 μm です。距離が正確に調整されていない場合、塗布の厚さ、塗布の幅、および不要なエッジ片勾配(スーパーエレベーション)の形成に影響が出ます。
実際のギャップ測定は、生産中の設備でオンタイムで行うことができ、塗布中も継続的にモニターできます。塗布の厚みやエッジ片勾配(スーパーエレベーション)の測定と組み合わせて、自動制御ループをセットアップすることで、システムの効率を大幅に向上させ、生産量を高めることができます。
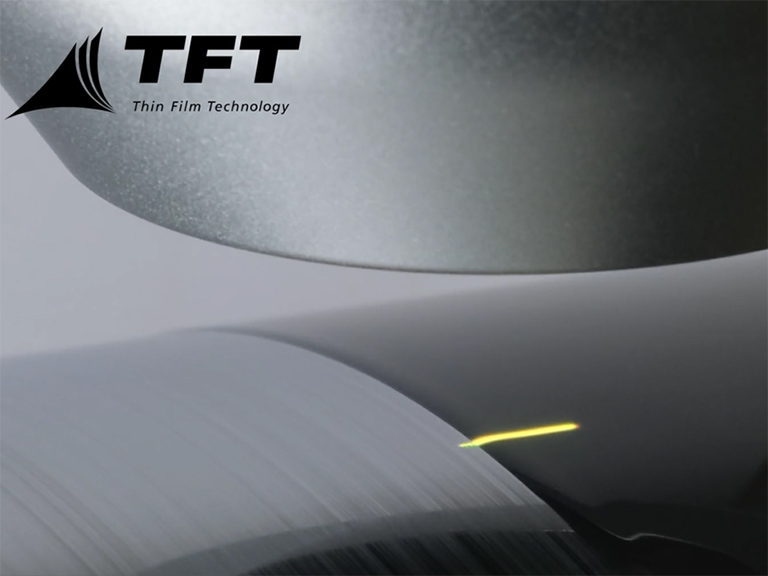
スーパーエレベーションは、塗布されたスラリーの境界で発生し、電極のさらなる加工、特にコイリング中に悪影響を与える可能性があります。非対称な厚さの巻線になり、後工程で大きな問題が生じる可能性があります。
バッテリーセルの性能を高めるため、現在、塗布の厚みを増す試みがなされています。しかし、厚い塗布はスーパーエレベーションを形成する傾向もあります。
プレシテックのラインセンサーは最大20 mmの幅を瞬時に測定できるため、製造工程でエッジ形状を正確に測定できます。ウェットエッジもドライエッジも検出でき、その過程で箔の振動も計算する事が出来ます。
また、反射性のメタリックキャリア箔から黒色スラリーへの遷移を正確に計測できます。
連続的な塗布のスタート/ストップ時にはエッジが存在します。この工程で、スラリーはキャリア箔に交互に塗布されるか、または塗布されない部分が生じてしまいます。塗布のスタート/ストップエッジの制御は難しく、バッテリーセルの長寿命と安全性を確保するためには、この部分の正確なモニタリングが必要不可欠です。
プレシテックのポイントセンサーを使用すると、形状プロファイルを正確に測定できるため、塗布の欠陥の可能性を早期かつ正確に検出できます。
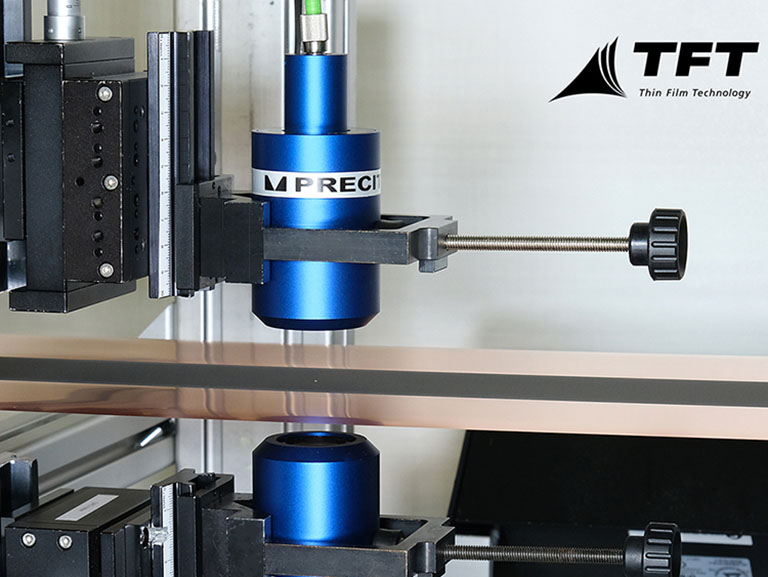
キャリアホイルに塗布された電極塗膜層の正確な測定は、電池の性能と寿命の長さに大きく影響を与えるため、重要な役割となります。塗膜製造工程では、まずキャリアホイルに電極ペーストスラリーを連続的に塗布し、乾燥工程で熱を加えてスラリー電極塗膜層から溶媒を除去します。キャリアホイルとスラリー電極塗膜層との高い結束強度を担保するには、塗膜乾燥過程5段階の識別が必須です。例えばこの5段階を識別することで、バインダーが電極塗膜表層部に移動し偏在するバインダーマイグレーションを抑制することができ、多孔質の空孔を形成する時間を確保する乾燥過程を最適化することが出来ます。
プレシテックのセンサーは、この5つの塗膜乾燥過程を特定出来ます、これにより、乾燥時間を短縮し、塗膜の品質を最適化し、エネルギーコストを削減出来ます。
また、全ての乾燥工程で、正確な厚み測定が可能です。ウェット層やドライ層、黒鉛や多孔質グラファイト、正極活物質がキャリアホイルに塗膜されていても、正確な厚み測定の結果が維持出来ます。振動とベルト速度の影響は測定中に補正されます。プレシテックのセンサーを使用することで、乾燥時間を短縮し、塗布の品質を最適化し、エネルギーコストを節約出来ます。
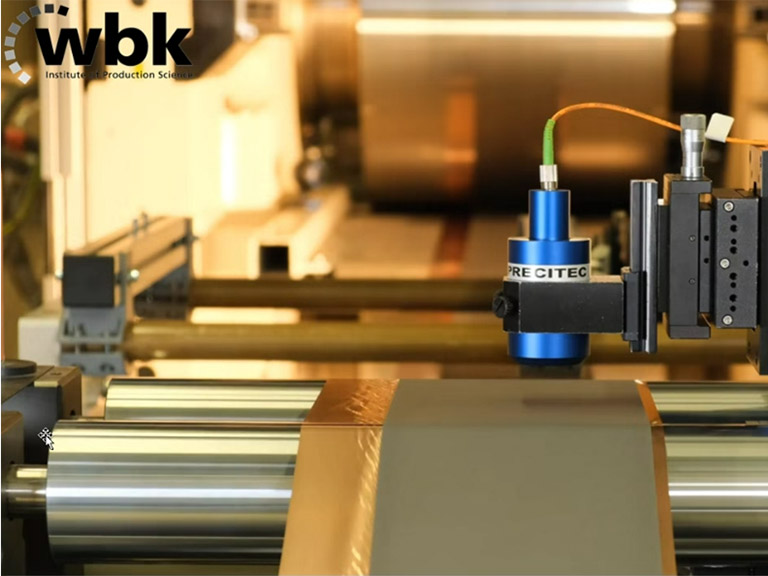
カレンダー処理は、電極箔製造工程の最終工程です。ここで電極塗膜の最終的な厚みと気孔率が決定します。ホイル単位面積当たりの重量に加え、厚みと気孔率は電池セルの性能と安全性を決定付ける特性です。
プレシテックのセンサーは、カレンダー処理工程の全般にわたり電極箔の厚みの測定が出来ます。カレンダー処理前後の電極箔の厚み、カレンダーローラーの同心度、スーパーエレベーションのような欠陥塗布を検出出来ます。これは、ホイル基材上の電極塗布の端に発生しやすい欠陥です。また、プレシテックのセンサーは、ホイルの振動を測定し補正演算することで、うねりを計算します。そのため100 ~ 150 m/分の高速なローラー送り速度でも、正確な測定が可能です。
カレンダーロールは、直径が 1 m を超えるスチール製の圧延ロールです。電極箔を高品位に圧延するために、鏡のように表面が研磨されています。圧延ロールの表面の欠陥や、わずかな同心度のズレは、電極箔の厚さや表面状態に悪影響を直接与えます。したがって、同心度と同様にカレンダーロール表面の摩耗状態を監視することも極めて重要です。
プレシテックのセンサーは、これら品質の特性を記録でき、同心度からのわずかなズレや、ロール表面のわずかな傷も検出できます。
カレンダーロールの力、電極塗布膜とキャリアホイル材料の膨張力の違いにより、圧延後にしわが発生することがあります。特に塗布面のスーパーエレベーションはキャリアホイルと塗布面の端部で必ず発生します。このようなしわが発生すると、後工程での対応を非常に複雑にし、最悪生産を止める事態となります。
プレシテックのセンサー技術を使用すれば、スーパーエレベーション等の塗布面の重大欠陥を検出し、そのサイズも測定出来ます。測定サイズが大きすぎる場合、材料は排除するよう制御出来ます。塗布不良の発生は、圧延パラメーターをクローズドループ制御等で調整することによっても抑えることが出来ます。
セパレータフィルムは、陽極と陰極2つの電極箔を分離し、短絡を防止します。セパレータフィルムは電気絶縁性でなければならないため、通常はポリプロピレンやポリエチレンなどの多孔質か、場合によっては多層のプラスチックで製膜構成されます。これらのセパレータフィルムの厚さは 15 ~ 25 μm で、異物による損傷があってはなりません。セパレータフィルムが異物で貫通してしまうと、陽極と陰極の電極箔がショートし、発火の危険性が高くなります(熱暴走)。
プレシテックセンサーを使用すれば、セパレータフィルムの厚さを測定したのち品位の特定が出来き、セパレータフィルムの個々の層の厚さを決定することが出来ます。
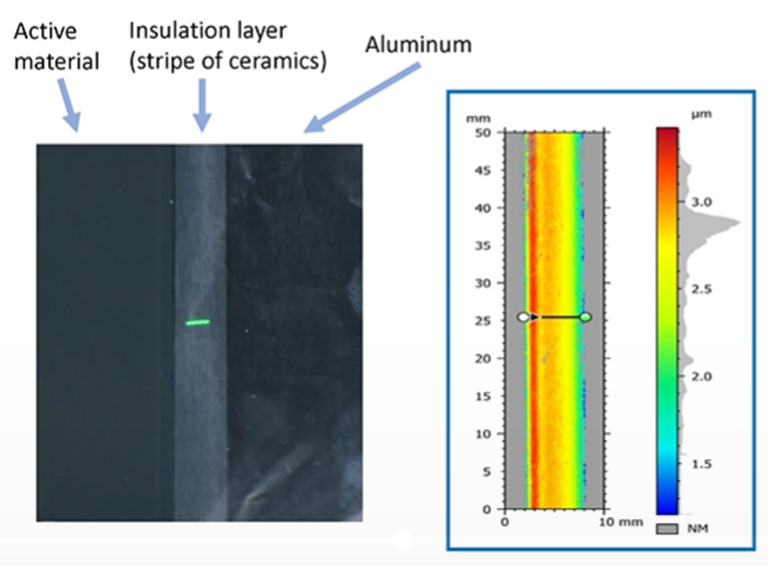
電池セルの安全性を向上させるため、電極に絶縁層を設けることがあります。この絶縁層はセラミックストリップでできており、活物質の隣に貼り付けられます。
その理由は、ポリプロピレン・セパレータは110℃の温度で収縮し、150℃以上では溶融することがあるからです。セラミックストリップは、正極と負極間の短絡の潜在的なリスクを防ぎ、電池セルの安全性を向上します。
標準的な絶縁層の厚さは3~10 µmです。最高の品質と効率的な生産のために、これらの厚みは最大 150 m/min のストリップ速度で、ロール・ツー・ロール工程のインラインで測定されます。これにより、酸化アルミニウム(Al2O3)の厚さプロファイルを表示し、欠陥を検出することができます。活物質とセラミックストリップ間のギャップが検出され、活物質上のセラミックの重なりも可視化されます。
セル製造工程におけるソリューション
電極箔の直線カットのために、Precitec は「スリットロール上でのガス補助レーザー切断」と呼ばれるソリューションを開発しました。この革新的な方法は、加工中に箔を正確にガイドし、振動を最小限に抑えることで、常に高い切断品質を保証します。ロール上で直接切断することにより、レーザースポットのサイズと平均出力が低減され、熱影響部(HAZ)が大幅に縮小され、全体的な切断品質が向上します。
ガス補助レーザー切断は、よりクリーンで効率的なプロセスも実現します。切断中に発生する粒子や残渣は、スリットロール内に誘導され、統合された排出システムを通じて安全に除去されます。これにより、レーザー切断システムの汚染が防がれます。
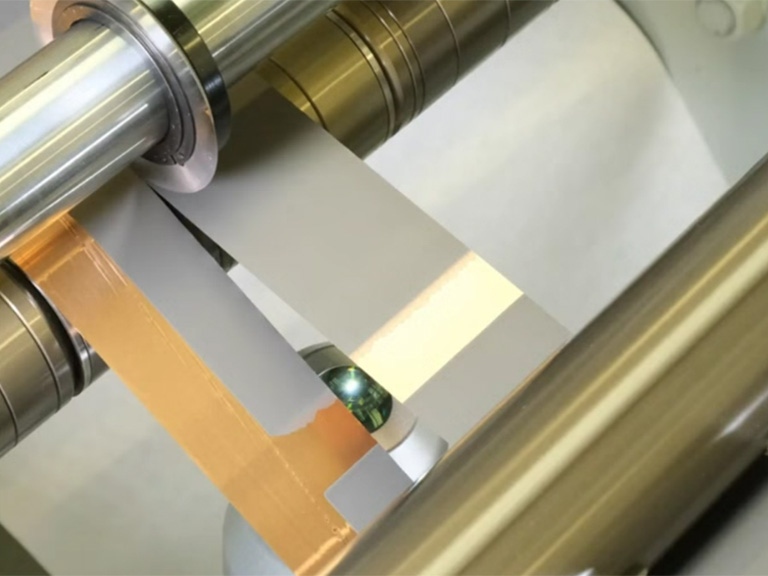
セパレータフィルムが貫通するとショートが発生し、発火の危険性が高くなります(熱暴走)。セパレータフィルムの厚さは通常約 20 μm(15~30μm) です。そのため、約 10 μm の切断バリを検出することは極めて重要となります。
バリの測定により、金属ホイルの形状、および下地の金属ホイルを含む塗布の形状を計測することが出来ます。バリの測定には、下からあるいは横からと他周辺機器や作業性に応じた方向からの測定手法が用いられます。ロール・ツー・ロールシステムに組込ことでで、バリを確実に検出し、スリッターの加工品質(予防保全)やレーザ切断に関する切断品質情報を入手できます。
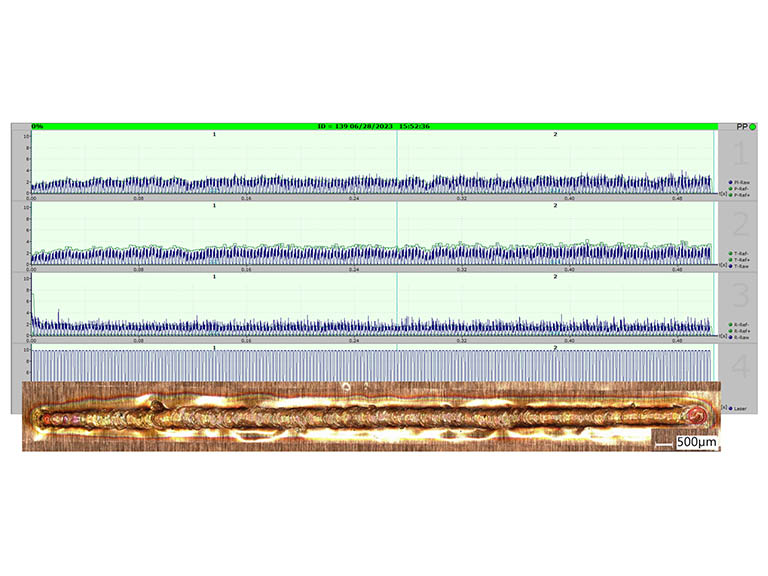
電池の集電体セルは活性物を塗布された銅ホイルやアルミホイル(5 ~ 10 μm)を何層にも重ねたものであり、それらが溶接され安定した高出力の電池が形成されます。通常、60 ~ 100 枚の銅またはアルミホイルが重ね溶接されます。電池の目標とする容量と性能に応じて、これらのホイルをいくつも重ねていきます。
ホイルをスタックして溶接する際、スタックの正確なクランプに加え、的確な溶接手順が必要です。これにより、最初のフィルムから最後のフィルムまで、歪みがなく、バンスルー(溶け落ち)のない溶接加工を実現出来ます。レーザ溶接モニタリリングシステムを使用することで、溶接の異常やわずかな違いを検出し、溶接継ぎ目の品質と信頼性を担保できます。最終的には、生産量の増加と製品品質の向上につながります。
詳細情報
キャップと缶のレーザ溶接では、金属製の蓋(キャップ)を金属製のコンテナ(缶)に溶接します。レーザ溶接による封缶シーム溶接は、電解質を外部から隔離し、液漏れを防ぐために、バッテリー製造で多用される工法です。蓋と缶の素材はアルミニウムまたはニッケルメッキのスチールです。
キャップと缶のレーザ封缶溶接は、円筒形だけでなく角形のバッテリーセルにも使用されます。いずれの場合も、溶接の品質は電池の性能と信頼性にとって極めて重要です。
4680 のような大型バッテリーセルでは、缶の丸みが必ずしも完全ではありません。しかし、溶接の気密性を高めるため、レーザビームが缶の輪郭に沿って走査することが必要です。
プレシテックScanMaster を使用すれば実際の輪郭を正確かつ迅速に検出測定し、輪郭に沿ってレーザビームを走査出来ます。このようにして、セル内に溶接貫通させずに高品質の封缶シーム溶接を実現出来ます。
キャップと缶のレーザ溶接の典型的な欠陥は、いわゆるピンホールで、これは溶接接合部からの液漏れにつながります。大きなピンホールは、レーザ溶接モニターで溶接異常として検出出来ます 溶接ビードの微細な欠陥は、ビード形状を後工程の計測機で外観検査することにより検出出来ます。こうすることでセルの再加工も可能になり、スクラップを減らすことが出来ます。
電池セルを組立工程で、電池の最適な性能を確保するため、電解液はセル内に均等かつ完全に充填されます。電池セル外側の充填口部に電解液が残留すると、製品の安全性が損なわれます。電池の生産量が増えるほど、電池セルの電解質充填口部の汚れの自動検出と、汚れた電池セルの自動排出の重要性が高まります。封孔シール溶接として知られる充填口のシール溶接の後工程では、円筒形または角形セルの充填口がレーザによって封孔シール溶接されます。電解液の残留は、封孔シール溶接の品質に影響 し、電解質の漏れや溶接スパッタによるコンタミ汚れにつながります。そのようなセルは、液漏れがあると判定され、NG排出されなくてはなりません。
電池セルに電解液を充填した後、充填口をカバーで閉じ、レーザでしっかりと溶接します。これによりセルが密閉され、電解液漏れを防ぎます。こうしてセルは密閉されます。
電池セルの溶接は、気密性の高い溶接が求められるため、非常に重要な工程です。セルに漏れがあれば、即スクラップとなります。不純物やスパッタは、溶接部からのわずかな液漏れにつながる可能性があります。したがって、セルを確実に密閉し、電解液が漏れないようにするには、シールピンを正確にピンポイントで溶接することが非常に重要です。目標とするのは、熱影響を抑えた、歪みのないしっかりとした溶接です。個々の溶接を、オンラインでモニタ、評価、記録するために、プレシテックの溶接モニタリングシステムは、不規則で欠陥のある溶接部をNG検出し、100% のトレーサビリティと工程の見える化を保証出来ます。
詳細情報
様々なセルの種類と用途
e-mobility には、一般的に 3 種類のリチウムイオン電池が使用されます。バッテリーは同じ機能原理で作動し、高出力を長い時間保ち続ける事が出来ます。使用されるセル形状はパウチ型、円筒形、角型があり、それらを複数接続してバッテリーモジュールが形成され、必要な電力を供給できるようになります。しかし、それぞれのセルタイプには、どのような違いがあるのでしょうか?