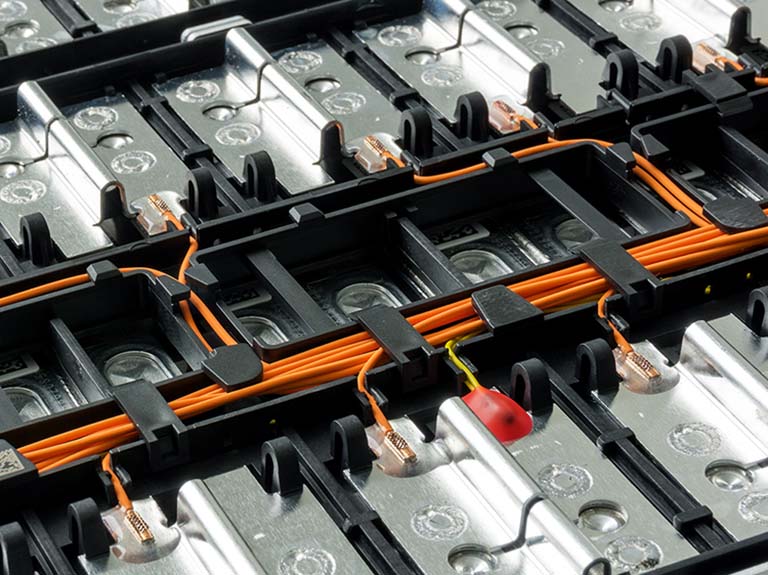
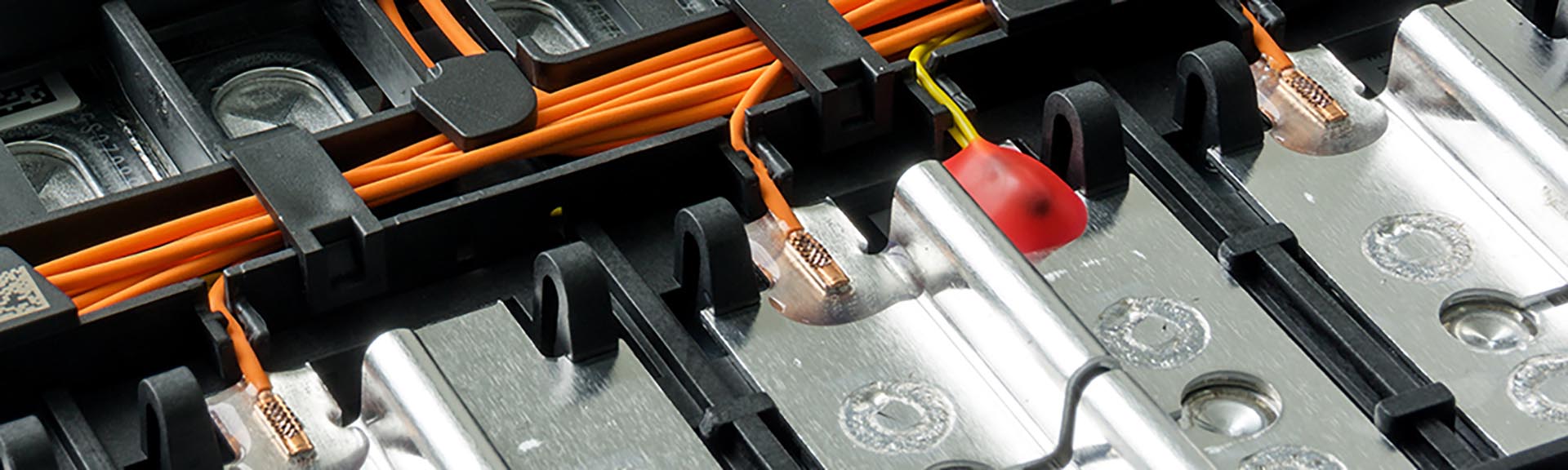
安全で信頼性の高いセル接合: バッテリーモジュール製造のための革新的なソリューション
個々の正極、負極の電池セル組立から始まり、バッテリーモジュール組立への工程と続いていきます。これらはアルミニウムやスチール製の金属フレーム、いわゆるパックにまとめられ、バッテリートレイに接着されます。
上記の工程手順の中で、安全に関わる 1 つの重要な工程があります。それは個々の電池セルの接合です。セルのコネクターが個々のセルにしっかりと溶接されていることが重要になります。I型シームの重ね溶接でその重要性を考えてみます。この接続は、2 枚のシートが接続されているかどうかを目視で確認することが難しく、非常に信頼性に欠けます。これは「フォルスフレンド」と呼ばれるタイプの欠陥です。

バッテリーモジュール製造における生産工程のソリューション
機械的負荷に耐え、溶接継手の規格要件を満たしながら、溶接継手の破損やクラックの発生を防ぎ、製品仕様に適合した高品質の部品を提供するには、溶接継手の特徴をいくつかチェックする必要があります。ピンホールの検出は、気密性の品質を左右します、さらに、溶接シーム部が溶融で十分充填され機械的負荷に耐えられるか、溶接シームのアンダーカット形状がノッチ効果やクラックを防げるか、焦点位置で変わる溶接シーム幅などがチェックポイントとなります。
このようなチェック課題をすべて解決するのが、プレシテックの CHRocodile CLS 2 ラインセンサーです。この製品は、5 μm 未満の微小な対象であっても、1 ラインで形状全体を高速に測定できます。
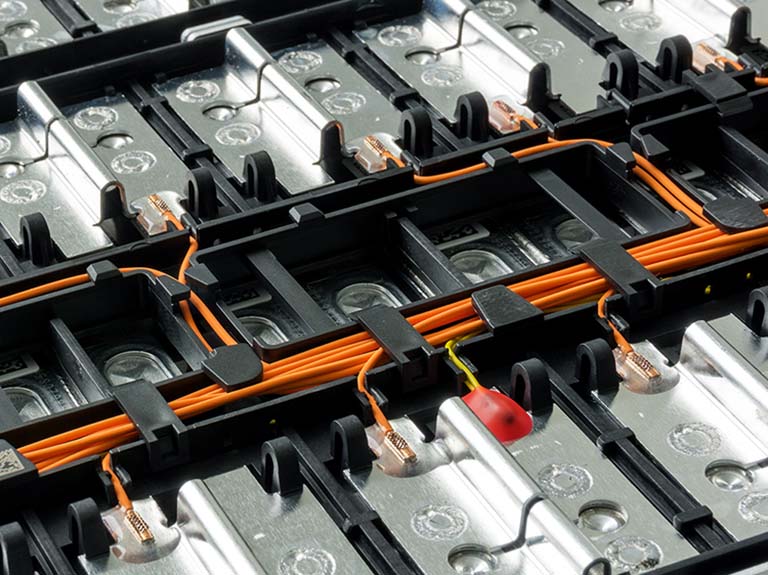
電池タイプが、円筒形、角形、パウチのいずれであっても、電池セルの精密で正確な製造工程が電池の性能と品質を決定づける要因となります。レーザは非接触で加工するので、この目的に適した安全なツールです。電池セル同士を接合は、熱影響を抑えた、歪みのないしっかりとしたスポットシーム溶接で形成されます。個々の溶接された接合部はを、オンラインで監視、評価、記録でするために、プレシテックの溶接モニタリングシステムは、不規則で欠陥のある溶接部をNG検出し、NG特定した不適合部分を手直し溶接を可能にします。これにより、100% のトレーサビリティと工程の見える化を実現出来ます。このようにして、セル製造のコストと品質を最適化出来ます。
電池セルとセルモジュールの接合で重大な欠陥は、いわゆる「フォルスフレンド」です。つまり、目視で見る限りでは溶接シームは良好に見えますが、電気的な接触(接続)がないという状態です。したがって、品質管理としてインライン溶接モニタリングシステムによる欠陥検出が不可欠です。
詳細情報

従来の丸型電池(円筒形の電池セル)では、電極箔は巻きa取られて金属製の筐体に密閉封入されています。ここで、セルの確実で欠陥のない接合が、最終工程の段階で電池の性能をフルに発揮することが確認出来ます。円筒形セルを接合する場合、レーザは 100 ~ 400 μm の非常に薄い層を溶接します。この正確で再現性のある加工は不可欠であり、インライン溶接モニタリングと組み合わせることで、生産ラインの信頼性を高めることが出来ます。これによって、セル製造コスト、品質、スループットを最適化出来ます。
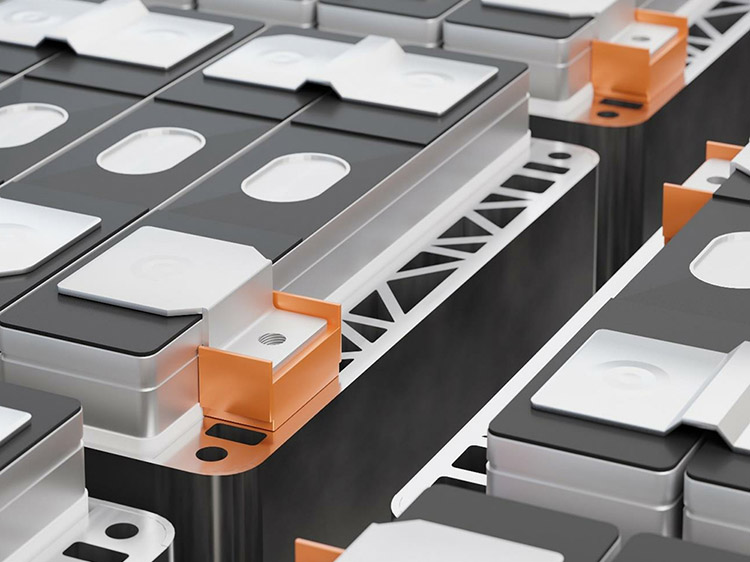
e-mobility 用バッテリーパックの塗布に UV 硬化型塗料やエポキシ塗料が用いられることが増えています。この塗料の厚さの測定は義務付けられており、特にバッテリーパックの角にあたる塗装膜の測定は特に重要です。しかしながら、既存の接触測定技術では再現性レベルが低く、オペレーターの技量に大きく左右されてしまいます。
電池セルで使用されている、特に不透明の塗装膜厚の測定には、プレシテック Enovasense のレーザ輻射熱を用いた測定技術が最適なソリューションとなり、優れた精度で表面全体を測定できます。この技術により、非接触、非破壊、非侵入、非放射による塗布厚の測定が可能となり、高速かつ高い費用対効果で卓越した再現性を実現出来ます。これは生産工程に簡単に組み込むことができる小型軽量の装置で、インラインまたはオフライン測定によって、工程の品質を向上させることが出来ます。センサーが全自動 3 軸コントロールステーション HKL2 に組み込まれていれば、あらかじめプログラムされたサイクルで、複数の測定ポイントを数秒でカバー出来ます。
詳細情報はフォームに記入することでダウンロードできます。
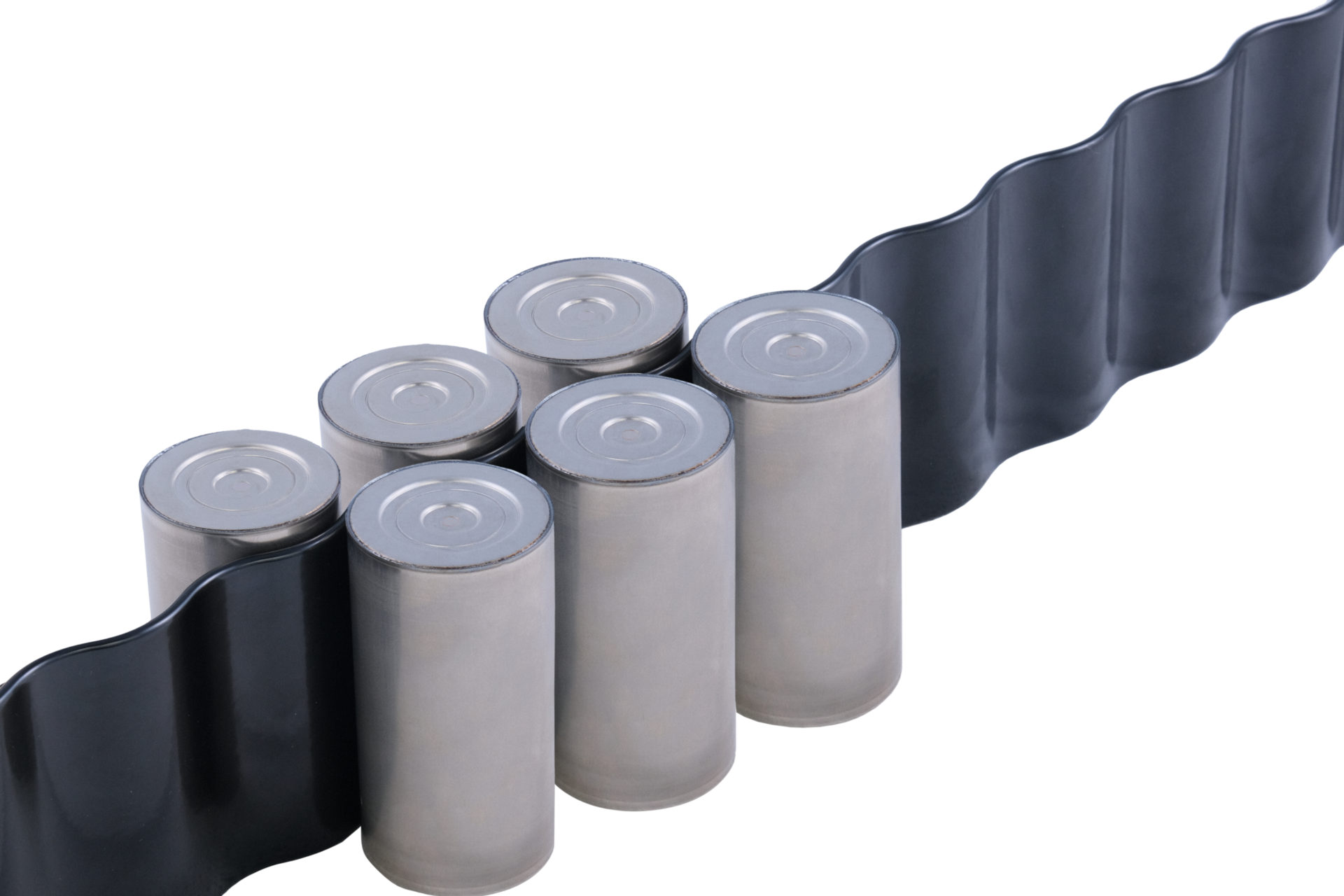
冷却管コーティングの厚さの測定
バッテリーセルの性能と寿命は動作温度に大きく依存するため、効率的な熱管理が求められます。
いわゆる冷却プレートや冷却チャネルは、バッテリーの動作温度を最適な範囲に保つのに役立ちます。
冷却プレートの内側にある冷却水ダクトは、冷却水を循環させ、熱を排出します。
通常アルミニウムまたは銅で作られた冷却プレートには冷却水ダクトがあり、冷却水が循環して熱を運び出します。ここでは、均一かつ全面的な接触が重要になります。
絶縁層は、バッテリーと冷却プレートを互いに電気的に絶縁し、短絡を防いで安全性を確保するために使用されます。
層が透明か不透明かに関係なく、Precitec ポイント センサーはこれらの層を測定できる可能性を提供します。 透明層の測定について詳しく知りたいですか?ここをクリック
不透明層の測定について詳しく知りたいですか?ここをクリック
次のステップでは、個々のバッテリーモジュールをバッテリーボックス内で組み合わせます。車体の軽量化が望まれているため、ボックスの材質は 5xxx および 6xxx シリーズの高強度アルミニウム合金となります。現時点ではクラックとスパッターが最大の課題となっているため、アルミニウム構造物でクラックとポロシティーを減らしたレーザ溶接品質を確保するには、高精度の品質監視システムとなるレーザ溶接モニタリングを使用することが不可欠です。
詳細情報
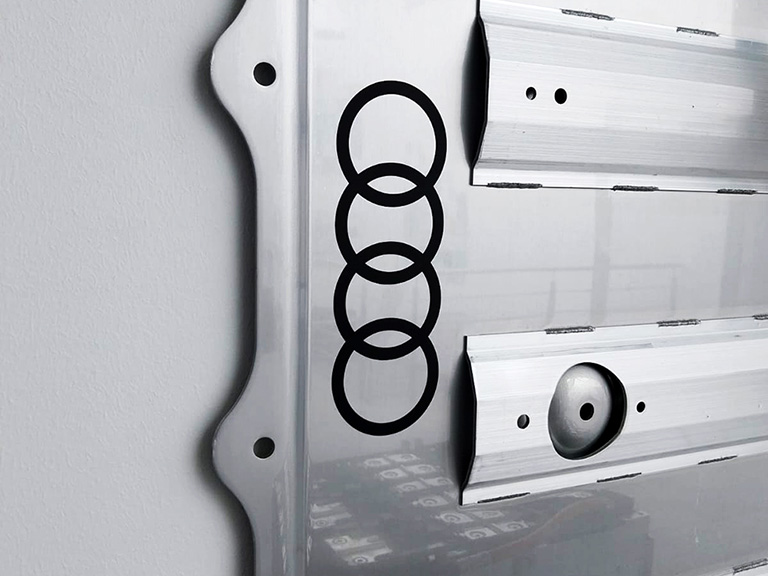
バッテリーボックスは、製造最終工程でアンダーライドガード(スキッドプレート)上に設置されます。この高強度素材と溶接され補強されたバッテリーモジュールは、損傷からの保護と耐性が恒久的に確保されます。ここでは、インテリジェントで自動化されたレーザ溶接システムが、熱影響による歪みを制御し、溶接シーム形状を最適に形成し、納得のいく溶接品質を提供します。レーザ溶接された接合部は、インプロセスで溶接モニタリング、また直後に外観検査にて品質評価を実施します。