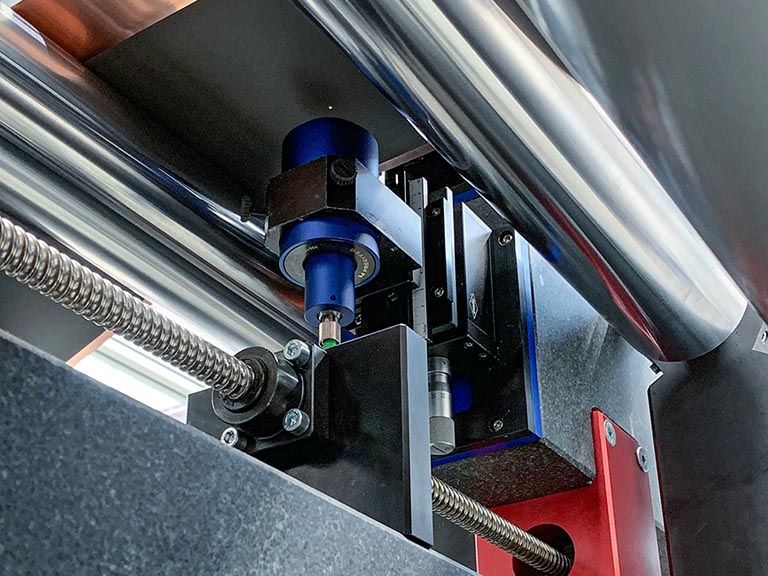
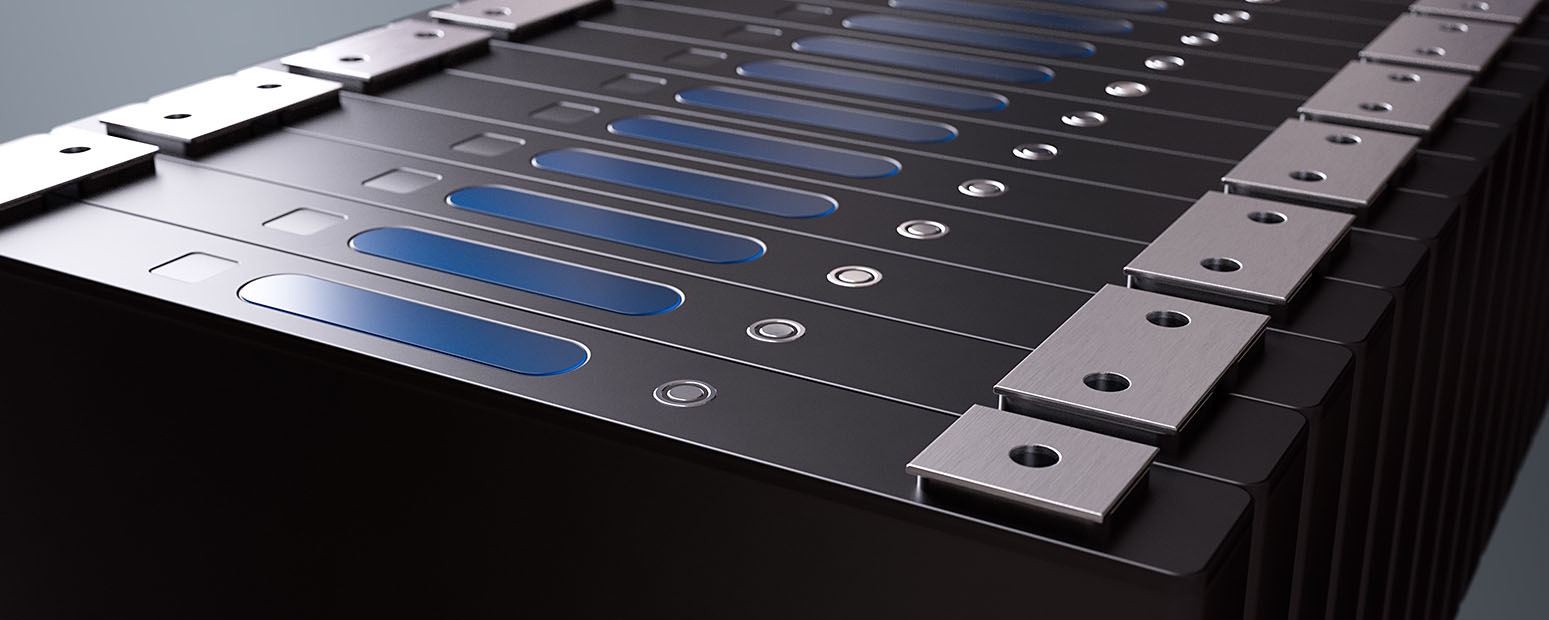
鋰電池生產的高效解決方案
在電極生產中,電池由交替的陽極箔和陰極箔層組成。它們由所謂的分隔層分隔開。然後將箔片堆疊起來,裝入金屬外殼中,然後將電池牢固地焊接起來。
我們的品質控制系統用於眾多製程步驟,以確保電池單元的高效生產。例如,這包括測量電極箔厚度、檢查切割毛邊以及雷射焊接箔層(箔到極耳)和帶有蓋子的外殼(蓋到罐)。
這裡明確的客戶要求是精度:< 1 微米。我們的感測器滿足這項要求,並針對電池的生產環境(即所謂的捲對捲應用)進行了最佳化:
• 高網路速度
• 振動電極箔
• 亮面和黑色表面。
在雷射技術中,蓋到罐雷射焊接是一個重要的應用。這裡的目的是檢測針孔,或充其量是完全避免針孔。我們專門針對這些應用優化了我們的產品和光學元件,並開發了創新的解決方案。
電極生產製造步驟的解決方案
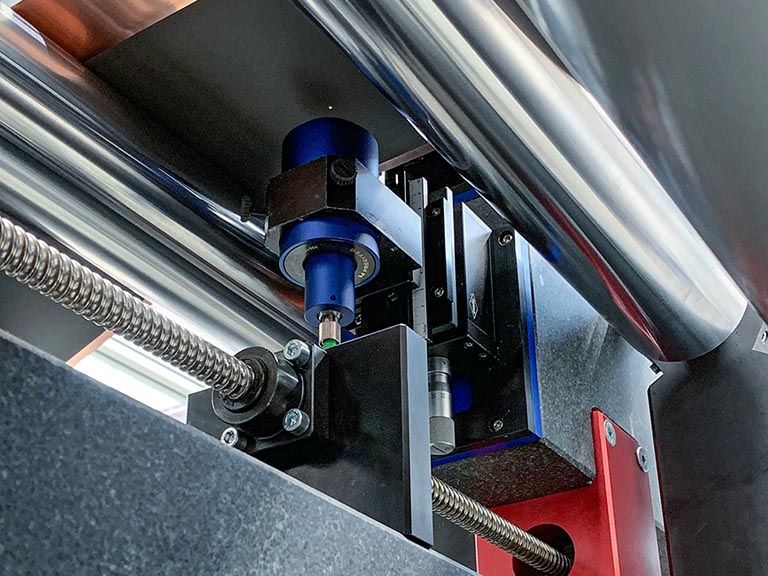
電極箔塗層厚度對電池的性能和壽命有重大影響,因此,塗層厚度的準確性很關鍵。在生產過程中,先將漿料連續或間歇地塗覆在載體膜上,然後在乾燥通道中去除塗層中的溶劑。
在乾燥過程前後分別進行厚度測量。塗層可以處於乾燥或潮濕狀態,也就是說,無論表面是反光、黑色還是多孔,我們的測量總是準確的。震動和皮帶速度的影響會得到補償。膜的波紋度和厚度經過精確分析後,會顯示結果。目前的市場要求是:絕對精度 < 1 µm,重復精度 ± 0.5 µm。
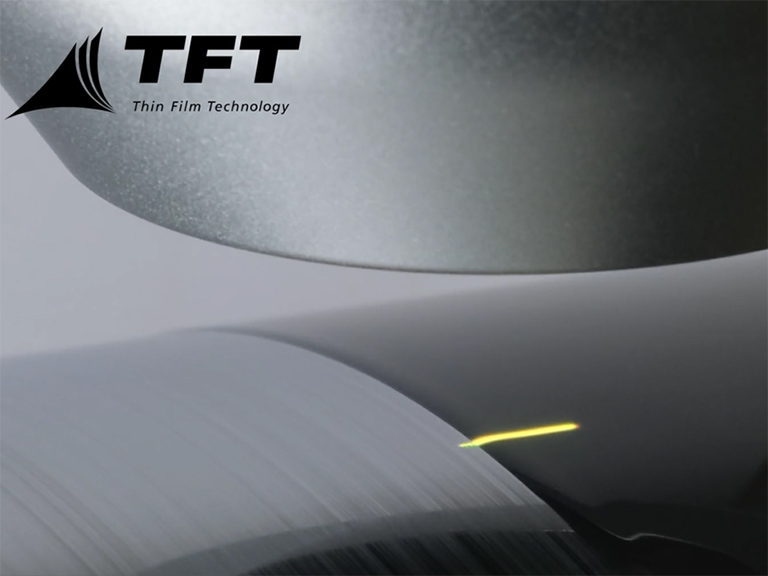
邊緣超高發生在漿料塗覆部位的邊界處,會對電極的進一步加工產生負面影響,尤其是在捲繞過程中。它可能導致捲繞不對稱,從而引發大量的操作問題。
為了提高電池的性能,目前正在嘗試增加塗層厚度。然而,塗層增厚後也容易形成邊緣超高。
我們的線感測器能夠在製造過程中精確測量長達 20 mm 的邊緣。濕邊和幹邊均可檢測到。在此過程中,能計算箔片的震動情況。從反光金屬載體箔到黑色漿料的過渡也可準確顯示。
起始/終止邊緣出現在間歇塗布期間。在此過程中,在載體箔上交替塗上漿料,或者故意不塗。塗上這種類型的塗層後,起始/終止邊緣會很棘手,必須對其進行監控,以確保電池的長壽命和安全性。
使用我們的點感測器,可以精確測量形貌輪廓,從而及早、準確地發現塗層可能存在的缺陷。
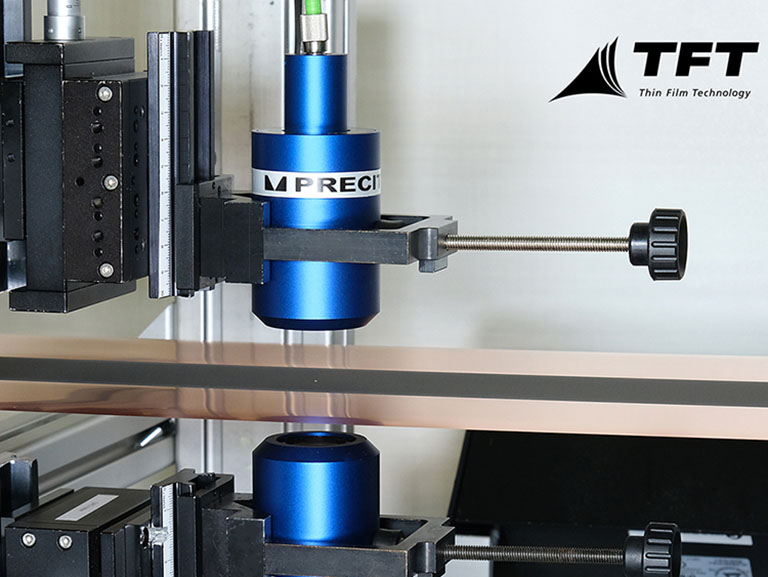
電極箔塗層厚度對電池的性能和壽命有重大影響,因此,塗層厚度的準確性很關鍵。在生產過程中,先將漿料連續塗覆在載體箔上,然後在乾燥通道中通過加熱去除塗層中的溶劑。為了保證漿料在載體膜上的高粘合強度,必須確定乾燥的 5 個階段。例如,必須防止粘合劑的遷移。為了優化乾燥過程,孔隙完全清空的時間也至關重要。
我們的感測器可以在乾燥過程中確認這些時間點。這樣可以縮短乾燥時間,優化塗層品質,降低能源成本。
在整個乾燥過程中,還可以進行精確的厚度測量。無論是濕層還是幹層、黑色還是多孔石墨或陰極活性材料,測量結果都非常準確。測量期間震動和皮帶速度的影響會得到補償。使用感測器可縮短乾燥時間、提高塗層品質,節省能源成本。
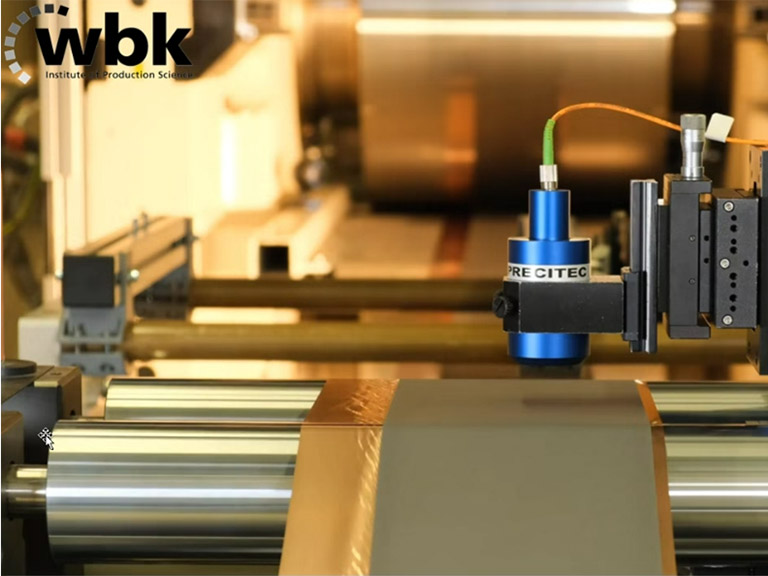
壓延是電極生產的最後一個工序,將基本確定塗層的最終厚度和孔隙率。除了單位面積重量之外,最終厚度和孔隙率也是電池性能和安全性的決定性特徵。
我們的感測器可以全面測量壓延過程,包括壓延前後的電極厚度、壓延輥的同心度和皺褶。皺褶是基底塗層邊緣的皺褶。我們的感測器會補償箔片的震動,然後計算波紋度。這意味著即使皮帶速度高達 100 - 150 m/min,也可以隨時進行精確測量。
壓延輥是直徑大於 1 米的實心鋼輥。鏡面表面經過精確研磨,可確保軋製的電極達到最高品質。軋製表面的缺陷以及同心度的微小偏差會直接影響電極箔的厚度和狀態。因此,監測壓延輥表面的磨損以及同心度至關重要。
我們的感測器可以記錄這些品質特徵,檢測同心度的微小偏差以及輥表面的最小劃痕。
由於軋製力以及塗層和箔材料的膨脹程度不同,軋製後會產生皺褶,尤其是在導電箔至塗層的邊緣處。皺褶會明顯增加後續生產過程的復雜程度,甚至令生產無法進行。
使用我們的感測器技術,可以檢測皺褶並測量其大小。如果皺褶太大,材料會被拒。通過調整軋製參數也可以減少皺褶的形成。
隔離膜將兩個電極箔(即陽極和陰極)分開,以防短路。隔離膜必須具有電絕緣性,因此通常由多孔塑膠(有時是多層塑膠)組成,例如聚丙烯或聚乙烯。這些薄膜的厚度在 15-25 µm 之間,並且不得被異物顆粒損壞。如果隔離膜被刺穿,就會造成短路且著火的風險很高(熱失控)。
有了我們的感測器,可以測量隔離膜的厚度和完整性,並辨析各個膜層的厚度。
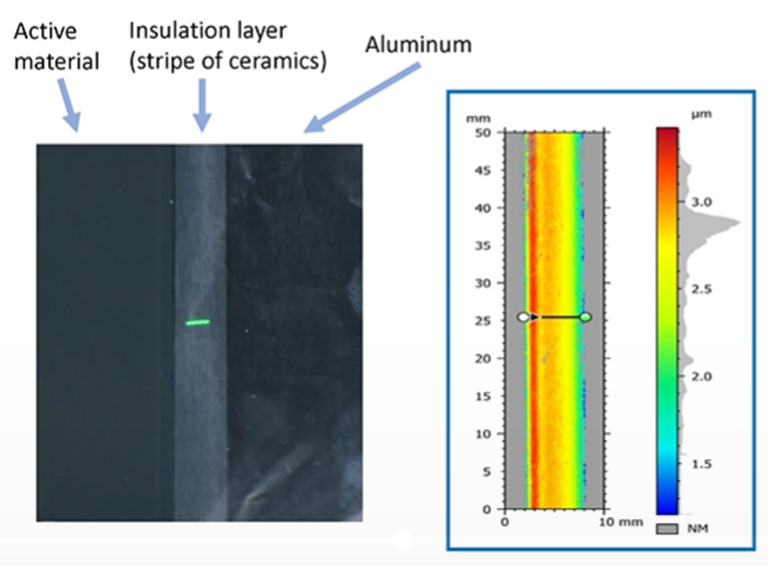
為了提高電池單元的安全性,有時會在電極上施加絕緣層。它由貼在活性材料旁邊的陶瓷條組成。
原因是聚丙烯隔膜在 110°C 的溫度下會收縮,甚至在 150°C 及以上的溫度下會融化。陶瓷條可防止陰極和陽極之間發生短路的潛在風險,從而提高電池的安全性。
絕緣層的標準市場厚度在 3 至 10 µm 之間。為了獲得最佳品質和高效生產,即使在高達 150 m/min 的帶材速度下,也可以在卷對卷製程中進行線上測量。例如,可以顯示氧化鋁 (Al2O3) 的厚度輪廓並檢測缺陷。檢測到活性材料和陶瓷條之間可能存在的間隙,並且還可以看到陶瓷在活性材料上的重疊。
適用於電池生產中製造步驟的解決方案
為了實現電極箔的直線切割,Precitec 開發了所謂的「基於開槽滾筒的氣體輔助雷射切割」解決方案。這項創新技術在切割過程中能精確引導箔材並將振動降至最低,從而確保始終如一的高切割品質。透過在滾筒上直接進行切割,不僅能有效縮小雷射光斑尺寸,還能降低平均雷射功率,顯著減少熱影響區(HAZ),進一步提升整體切割效果。
氣體輔助雷射切割同時提供更潔淨、更高效的加工過程。切割過程中產生的粒子與殘渣會被引導至開槽滾筒內,並透過整合的抽取系統安全排出,有效防止雷射切割系統受到污染。
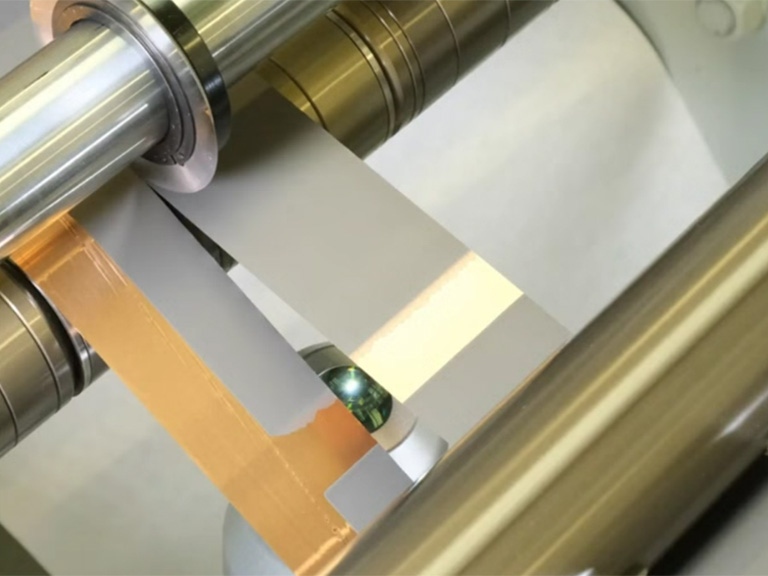
如果隔膜被刺穿,就會造成短路且著火的風險很高(熱失控)。隔膜厚度通常約為 20 µm。因此,檢測到約 10 µm 的切削毛邊極至關重要。
對毛邊進行測量可以顯示出金屬箔的幾何構造和外形以及塗層(包括下層金屬箔)的形貌結構。根據任務和要求的不同,可採用不同的技術從下方或側面對毛邊進行測量。與卷對卷系統集成後,我們可以進行確切的毛邊檢測,從而提供有關縱切機(預測性維護)或雷射切割品質的資訊。
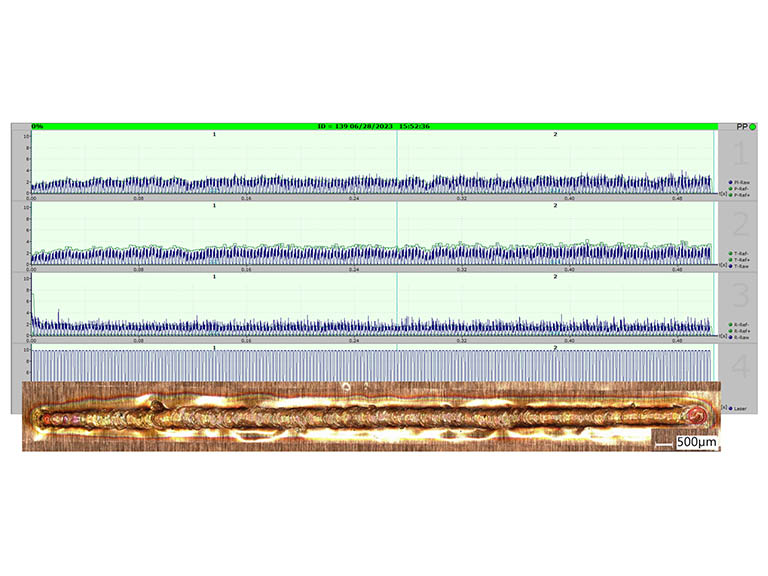
電芯由多層薄銅箔和鋁箔 (5 - 10 µm) 組成,必須將它們焊接在一起才能形成穩定且強大的電池。在此過程中,通常的做法是將 60 - 100 個箔片焊接在一起。然後,根據電池所需的容量和性能,將多層箔片堆疊起來。
在焊接堆疊起來的箔片時,除了要精確夾緊箔片之外,智慧焊接策略的作用也很重要。這樣做可以讓第一層膜到最後一層膜之間實現安全連接,且變形很小,沒有燒穿現象。通過使用過程監控系統,可以檢測到焊接異常和最小偏差,從而確保焊縫品質和可靠性。最終,這將帶來更高的產量和更好的產品品質。
瞭解更多
蓋帽到罐體的雷射焊接是將金屬蓋(蓋帽)焊接到金屬容器(罐體)上。這種類型的雷射焊接常用於電池生產,目的是讓電解質與外界隔絕,防止液體洩漏。這裡使用的材料是鋁或鍍鎳鋼。
蓋帽到罐體的雷射焊接不僅可用於圓柱形電池,也可用於棱柱形電池。在這兩種情況下,焊接品質對於電池的性能和可靠性至關重要。
對於 4680 等大型電池,罐體的圓度並非總是 100%。但是,必須沿著罐體的輪廓引導雷射波束,這對於焊接的緊密性非常重要。使用 ScanMaster 可以準確、快速地測出真實輪廓,並且可以相應地調整雷射波束。如此可避免焊接到電池裡,以獲得高品質焊縫。
蓋帽到罐體的雷射焊接有一個典型缺陷,那就是針孔,它會導致焊接接頭發生洩漏。雷射焊接監視器會將大針孔檢測為焊接異常情況。在後處理過程中,會通過測量焊縫的形貌結構來檢測焊縫上的最小缺陷。這樣就可以對電池進行返工,減少廢料產生。
在組裝電池單元的過程中,電解質會均勻、完全地填充並分佈到電池中,以確保電池達到最佳性能。電池外部的電解質殘留會影響產品安全。生產的電池越多,就越迫切需要在生產線上對電池單元充液側的污染區域進行自動檢測和清除。在隨後的密封銷焊接過程中,圓柱形或棱柱形電池的充液口將採用雷射密封焊接。電解質殘留會影響焊縫的品質,並可能導致洩漏或者因焊接飛濺造成嚴重污染。這樣,電池就會發生洩漏,從而成為廢品。
向電池單元注入電解質後,用蓋子封閉充液口並採用雷射緊密焊接。這樣可以密封電池,防止電解質逸出。電池就這樣被密封住了。
電芯焊接是一個關鍵的工序,因為它是一種緊密焊接。如果電池發生洩漏,就會報廢。雜質或飛濺物可能會導致焊縫出現微小洩漏。因此,對密封銷進行精確點焊對於確保電池密封性且電解質不洩漏具有非常重要的作用。我們的目標是以較低且局部有限的熱輸入做出無變形的緊密焊縫。每個焊縫都可以在線監控、評估和記錄。我們的系統可以檢測出不規則和有缺陷的焊縫。確保流程 100% 可追溯且透明。
瞭解更多
針對不同應用的各種電池類型
電動車通常使用的鋰離子電池有三種。這些電池工作的功能原理相同,具有高能量密度,可確保長距離行駛。使用軟包電池、圓柱形電池和棱柱形電池時,將它們連接起來形成電池模組,能夠提供所需的電力。但這幾種電池有什麼不同?