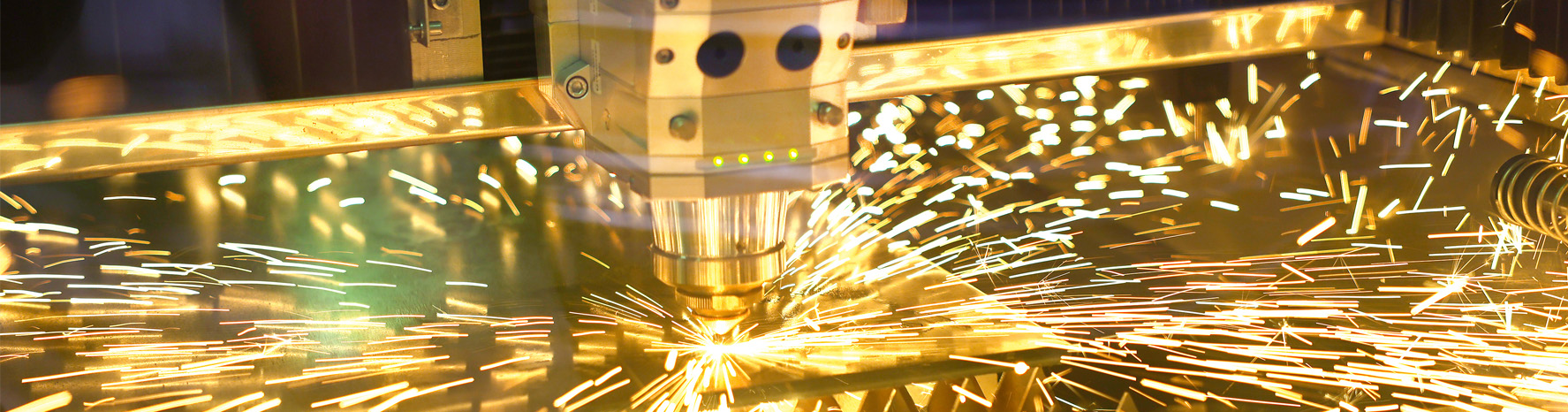
How does high power in laser cutting shape the future of metal fabrication?
Imagine a tool so precise that it can cut through metal with the finesse of a skilled artisan, yet with the force of thousands of watts. This isn't a scene from a futuristic movie; it's the reality of fiber laser technology in metal cutting today. The journey began with fiber lasers capable of modestly slicing through 3 mm thick metal sheets, a feat that heralded a new era in manufacturing efficiency and versatility.
As technology progressed, the natural progression was to ramp up the power. The move from hundreds of watts to kilowatts wasn't just a numerical jump; it was a leap toward transforming metal cutting. Initially, machines boasting 1 to 2 kW power significantly enhanced the thickness of metal they could handle, promising a direct correlation between power and productivity. Yet, as we ventured beyond 20 kW, an intriguing phenomenon emerged: the increase in power no longer translated linearly to efficiency or the capacity to cut thicker materials.
It's crucial to understand that a laser's power isn't the sole determinant of its cutting capability. Real-world applications, varying from laboratory settings to the gritty reality of industrial environments, reveal the nuanced dance between power output and cutting quality. Choosing a laser for metal fabrication involves considering a 'power reserve'- essentially, opting for more power than you might think necessary. This reserve is not about excess but about flexibility, allowing for high-quality cuts across a spectrum of materials and conditions.
The choice of gas - nitrogen, oxygen or even mixed gas - plays a pivotal role in the cutting process, especially when dealing with diverse metals like non-ferrous metals, stainless steel, or black iron sheets.
- Nitrogen facilitates swift, clean cuts in thinner metals, significantly outpacing oxygen in both speed and efficiency, this is because utilizing oxygen in the cutting process creates a notably larger kerf, resulting in a reduced cutting speed.
- Oxygen's slower pace is more suited to thicker black iron, where its lower cost can offset the reduced speed.
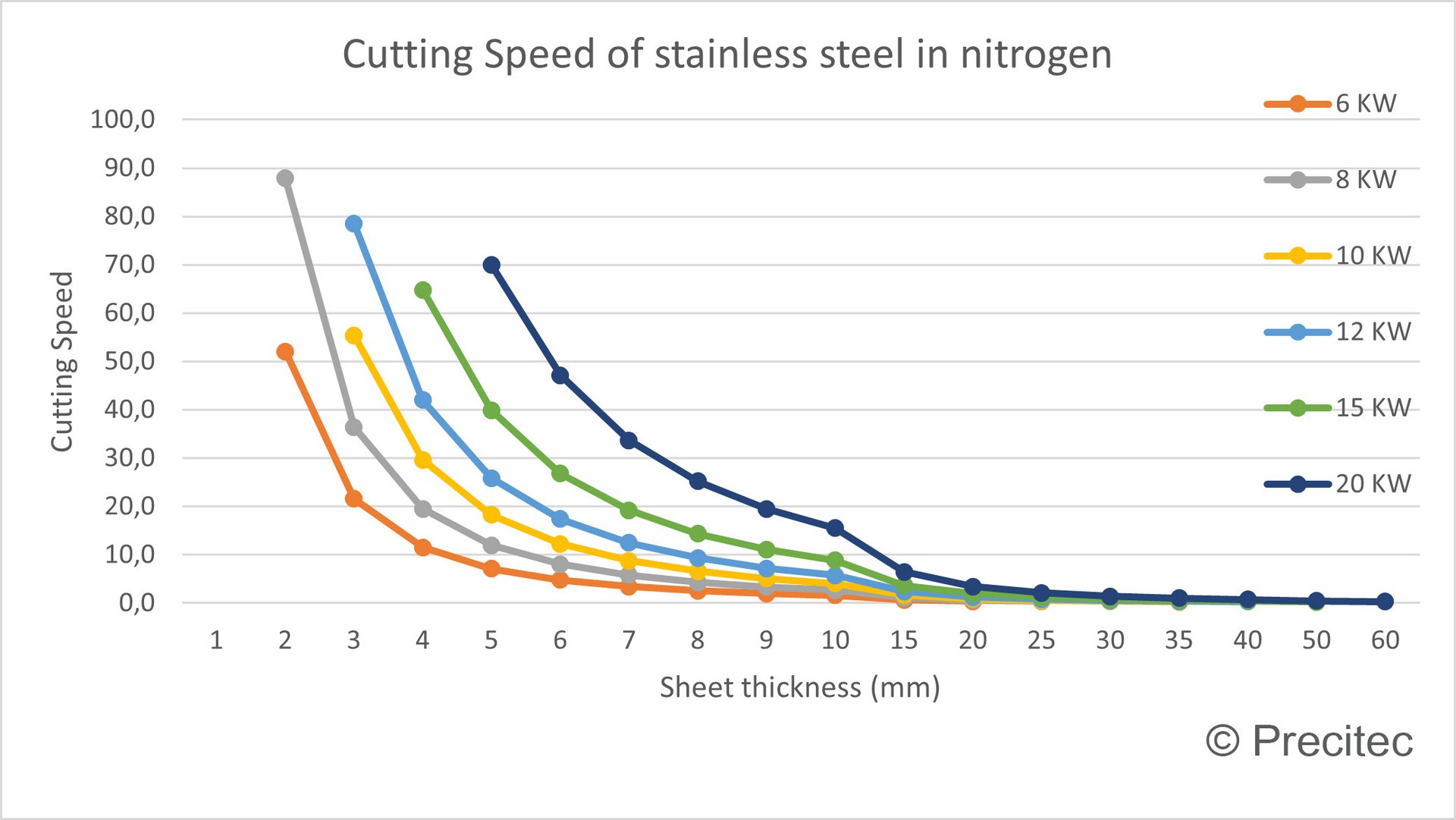
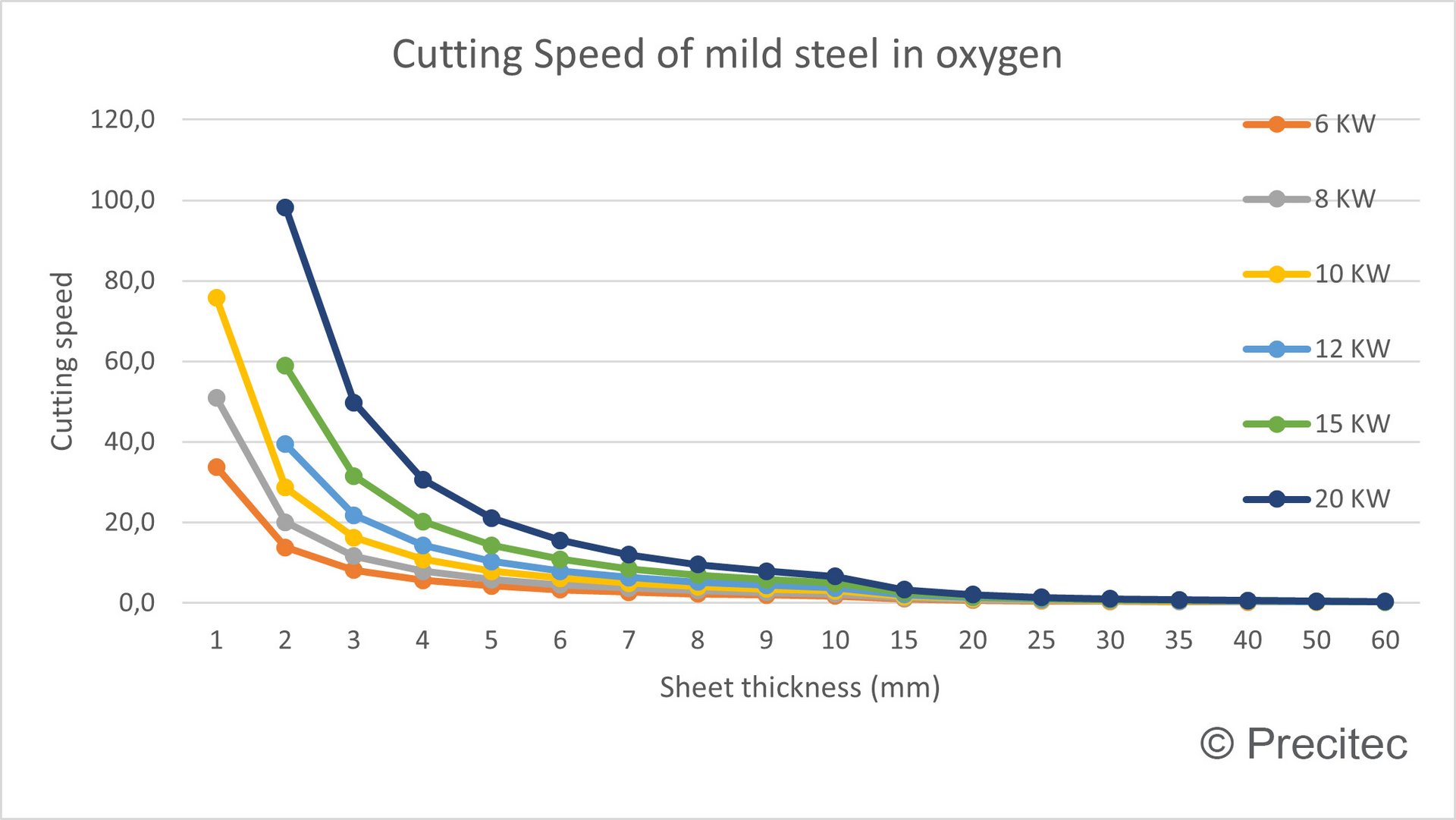
The graph illustrates that elevating the laser power for both stainless steel utilizing nitrogen and mild steel employing oxygen results in a significant enhancement of cutting speed at specified thickness levels, while also enabling the cutting of materials with increased thickness.
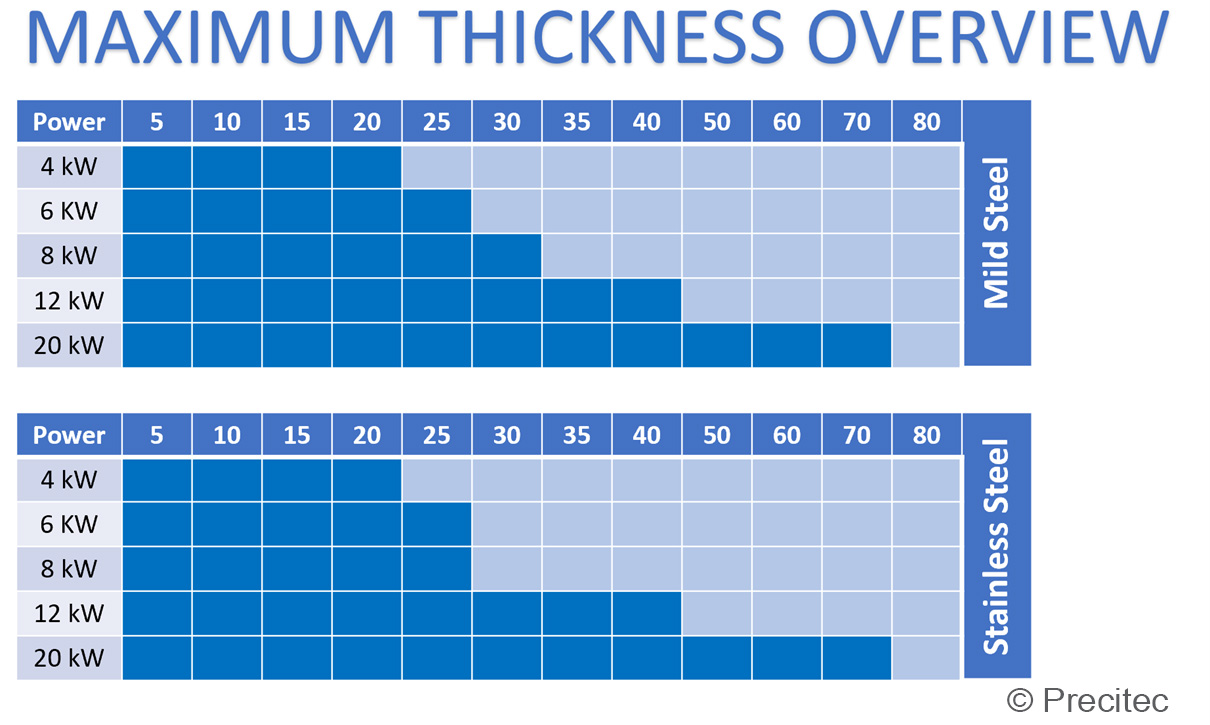
The chart underscores the critical role of selecting the appropriate support gas for laser cutting: oxygen enhances the cutting speed and capability of mild steel, while nitrogen ensures oxidation-free, clean cuts in stainless steel. The choice between nitrogen and oxygen transcends mere cutting speed, embodying a balance of efficiency, cost, and environmental considerations.
Although nitrogen cutting offers quicker speeds and cleaner edges, it demands higher gas pressure, leading to increased operational costs. Nevertheless, the advantages of enhanced efficiency and the relatively lower cost of nitrogen can outweigh these expenses, rendering it the favoured option for a broad spectrum of applications.
The chart serves as a reminder of the nuanced considerations that go into efficient and quality of laser cutting, such as
- the type of steel
- the thickness
- the laser power
- the choice of support gas
The data is clear: higher power outputs bring substantial benefits to the table, from cutting thicker materials to achieving speeds previously deemed impossible. A 3kW laser might navigate through a 15mm thick plate, but doubling the power to 6kW can extend this capability further, enhancing both the thickness and speed of cutting. A similar phenomenon can be observed with a further increase in power.
As we stand on the brink of further advancements in laser technology, the focus isn't just on power. It's about understanding the entire ecosystem of laser cutting, from material properties and cutting gases to operational efficiency and environmental impact. The future of metal fabrication lies in investing not just in higher power outputs but in smarter, more sustainable technologies that push the boundaries of what's possible.