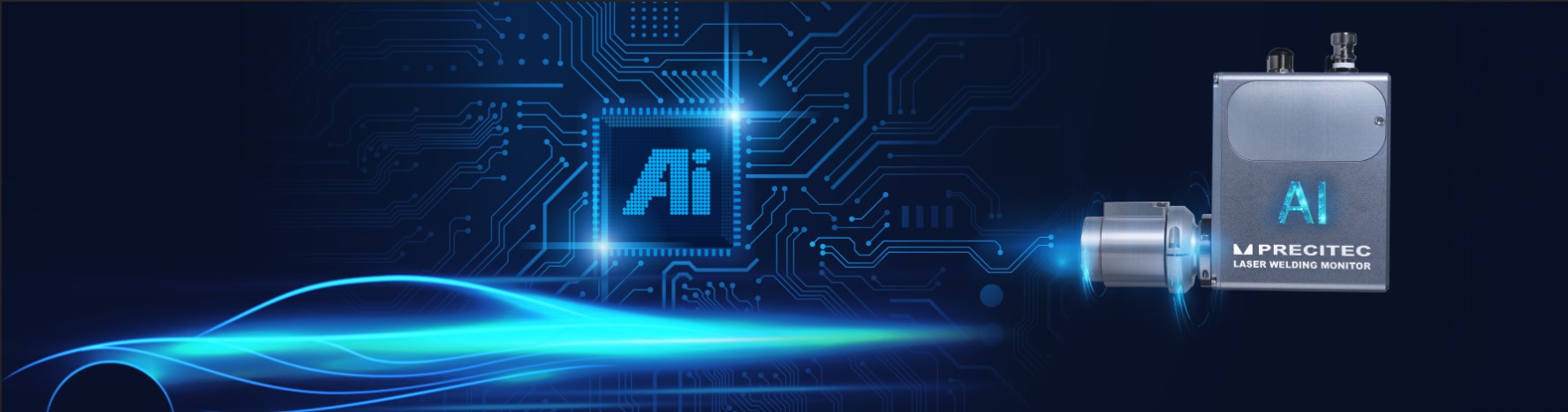
Optimized quality monitoring for your laser welding process with artificial intelligence
Modern production processes are subject to constant change and require innovative solutions. By using artificial intelligence, manufacturers can now control their welding processes even more efficiently and precisely.
The Laser Welding Monitor LWM with its latest AI function represents a breakthrough in the analysis of laser welding emissions.
- Prediction of weld strength - Physical properties, such as the maximum load capacity of the weld, can be precisely determined.
- Automatic defect classification - In the event of a faulty weld (NOK), the defect type is reliably detected and assigned. This increases the objectivity of the analysis and facilitates process optimization.
The Laser Welding Monitor LWM detects process deviations in fully automated production environments and ensures that your quality standards are met at all times. Every single laser weld is monitored, analyzed and documented to ensure complete traceability and consistent quality in series production.
Discover how our technology is successfully used in the mass production of battery contacts in the following video.
Prediction and lean processes
Prediction of physical properties of the laser weld seam by LWM AI
Automatic defect classification - detection of the defect type in the event of a bad weld
Inline data acquisition - takes place directly during laser welding and is cycle time-neutral
Valuation and calculation
Quantifiable results - LWM AI increases objectivity in quality assessment
Easy handling for the plant operator - automatic OK/NOK prediction incl. defect type detection
Adaptability and analysis
Valid results without retraining - even if the process parameters change within a defined range
Automatic defect classification - enables targeted rework strategies through AI-supported analysis of the defect type
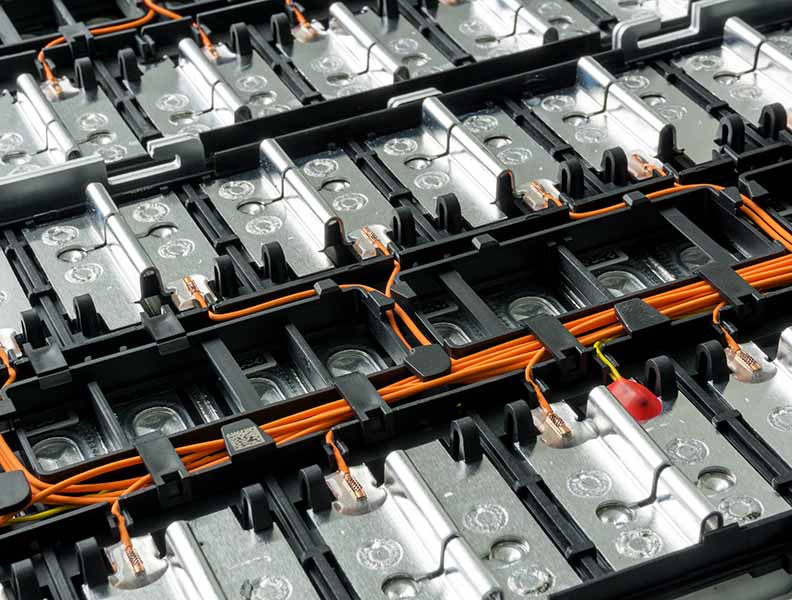
Contacting battery cells with artificial intelligence
The Laser Welding Monitor LWM with AI records emissions during laser welding inline and cycle time-neutral and evaluates them in real time. By using artificial intelligence, this data is used to precisely predict the physical properties of the weld seam.
The technology has already been successfully tested for battery contacting and enables the prediction of:
- Maximum force of the weld seam
- Gap size between the components
- Weld depth
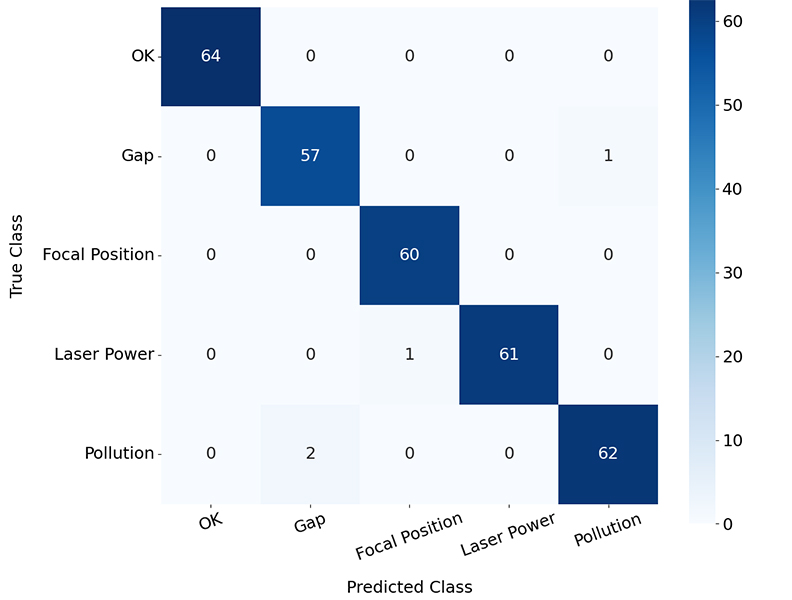
The advantages for the user?
In the past, machine operators had to interpret the sensor signals themselves - today, the AI provides physical values directly, e.g. 1,234 N welding force. This makes it much easier to distinguish between good and faulty welds and to derive targeted measures.
Possible sources of error can also be identified: If the AI detects a gap of 345 micrometers, for example, a faulty clamping device could be the cause.
AI-supported process monitoring gives manufacturers greater process reliability, improved quality assurance and more efficient production processes.
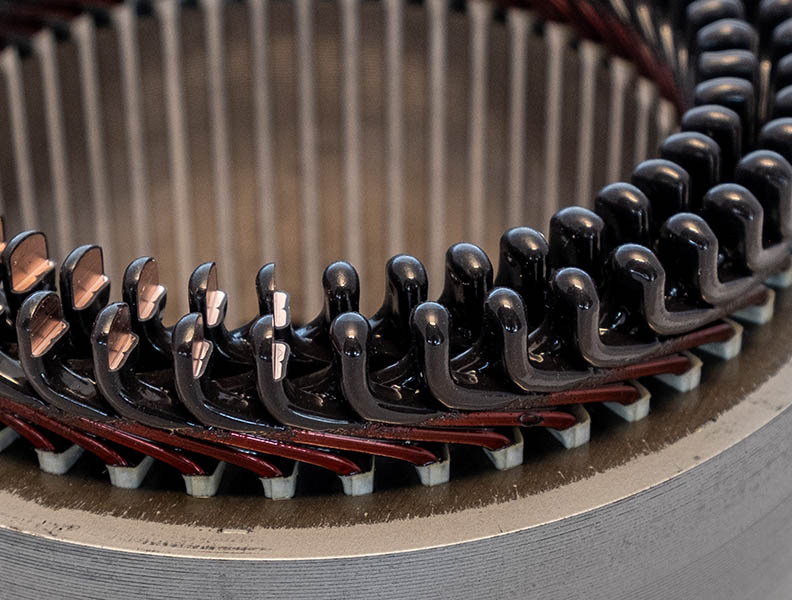
Laser welding of hairpins with artificial intelligence
Another successful example of the use of artificial intelligence in laser welding can be found in stator production, particularly in hairpin welding.
AI-supported analysis can be used to reliably predict key quality parameters:
- Welding seam contact area
- Electrical resistance
In addition, the AI even enables root cause analysis for defective weld seams to a certain extent, for example by recognizing whether there is insufficient laser power or an incorrect focus position (defect type classification). Once the defect type has been identified, the end user can apply an adapted post-processing strategy in a targeted manner.
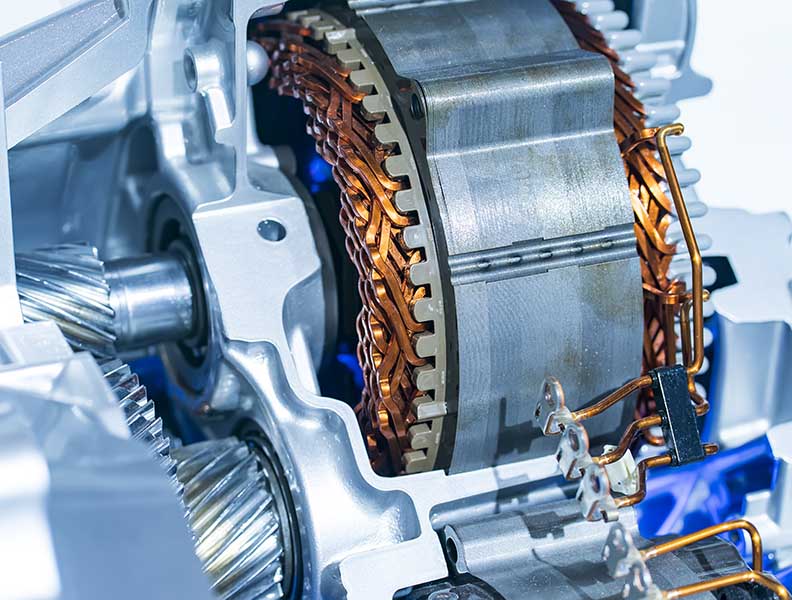
The advantages for the customer?
Predicting the electrical resistance and the bonding area is essential for assessing the quality of a hairpin weld. Our AI now provides clear, physical values, eliminating the need to interpret sensor signal curves. This makes quality assessment much easier and offers greater process reliability for the system operator.
Technical data
- Prediction of several physical parameters in real time
- Application area solid-state lasers: for IR / blue / green lasers and CW or pulsed mode
- Possible applications: Consumer electronics, battery and stator production for the e-mobility sector
We need your consent to load the form!
We use Marketing Cloud Account Engagement (Pardot) Forms to embed content that may collect data about your activity. Please review the details and click in the Pardot box to accept the service and see the content. If the form is not displayed correctly, please click once more on Download the data sheet now.
Do you still have any questions or would you like an offer? Then contact us!
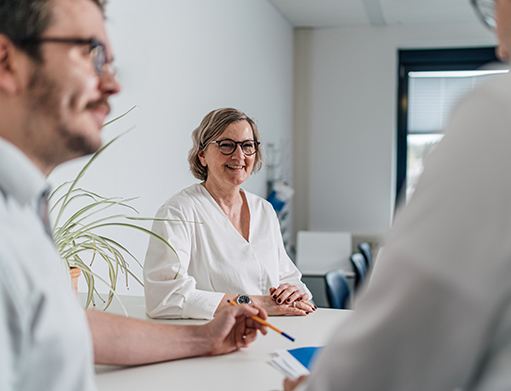