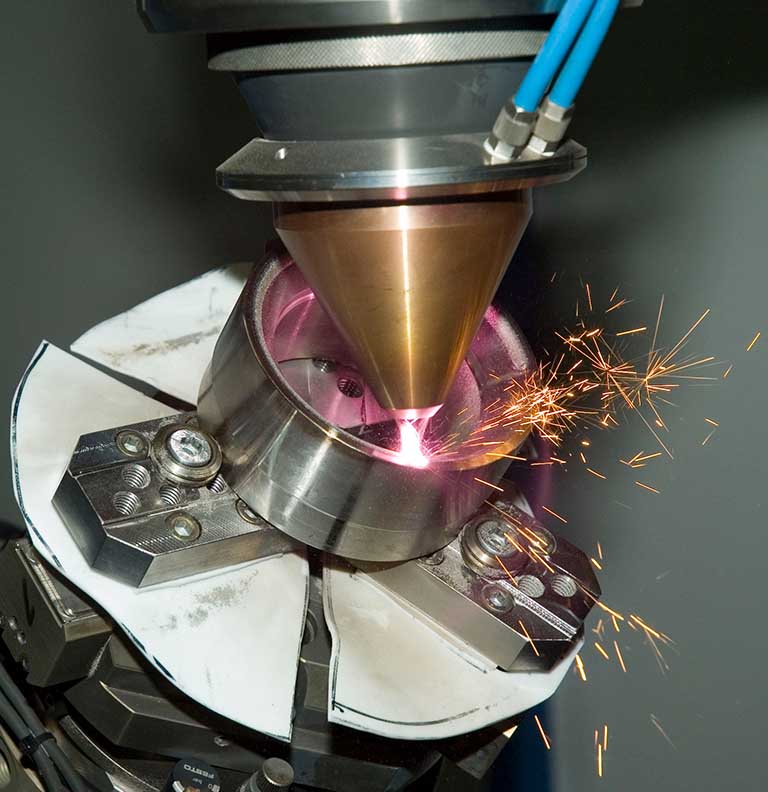
Reinforcement by laser deposition welding
Local functional layers for longer life
Laser deposition welding is a coating process that is used in modern production and maintenance. In aerospace, shipbuilding, power generation, and tool and die industries buildup, welding is used to optimize or repair the highly stressed surface of a component.
By applying a function-optimized layer, the component is reinforced exactly where the highest stress is expected. In this way, service life can be extended and costs saved. Furthermore, depending on the alloy of the layer material, such properties as corrosion resistance and strength can be improved.
The repair of high-quality components or expensive tools is another important area of deposition welding. In this process, the surface of the material is heated locally with the laser and at the same time material is added. The component geometry and its properties are restored and the component can once again perform its full function.
The processing head YC52 combines efficiency and flexibility in laser deposition welding with powder and enable you to cover a wide range of applications. Almost pore-free layers with a long service life can be produced completely independent of direction. The Precitec IDM is able to measure the height of the applied layer during the laser weld deposition.
Precitec offers the CoaxPrinter for laser deposition welding with wire. The innovative beam shaping enables a true coaxial wire feed into the process. This enables a completely direction-independent process control even with different materials. Additive processes with wire offer easy handling and better effieciency as the wire is used completely utilized. The results are often accompanied by high productivity and clean post-process surface conditions.