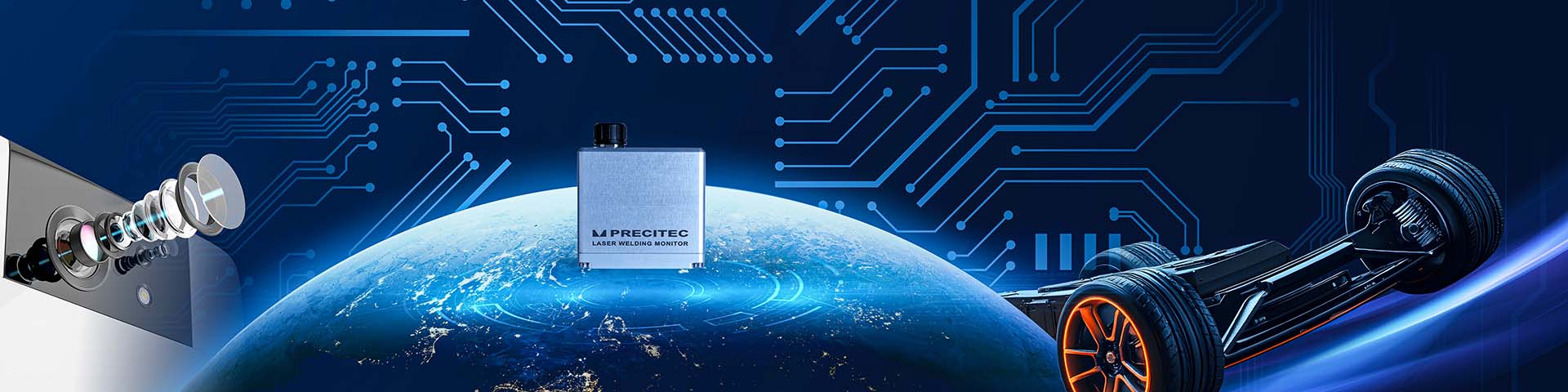
Quality control of your laser welding processes in real time
The Laser Welding Monitor LWM is used for online process monitoring in industrial production in 24/7 operation.
In series production, it records and documents quality and productivity-relevant process data for laser welding seams for all relevant laser welding processes, such as heat conduction welding or laser welding with keyhole. The high dynamic range of the sensors enables the monitoring of high-performance welding applications through to micro welding applications.
Quality fluctuations caused by component tolerances, contamination or wear are reliably detected and monitored. The system is simple and intuitive to operate and can be flexibly integrated into almost any customer application, facility and infrastructure.
The combination of comprehensive quality control, flexibility and precision makes the Laser Welding Monitor LWM an indispensable tool for maximum quality and efficiency in modern laser welding production.
Discover process monitoring for laser welding of battery cells:
Your advantages at a glance
Increasing output
The Laser Welding Monitor LWM increases productivity through precise real-time monitoring of the laser welding process. It detects deviations in welding parameters and seam quality by comparing the process fingerprint with the current process data. This identifies faulty welds in real time, minimizes rework and rejects and reduces downtimes.
100% traceability and transparency
All process data is consistently stored and documented for each component. In combination with online backups, the system enables 100% traceability and transparency of your laser welding processes.
Intelligent adaptation of fault detection
New material batches can lead to systematic, abrupt shifts in the process signals. These shifts can be detected by the intelligent software package and the parameterization can be adapted automatically - without the need for a new teach-in.
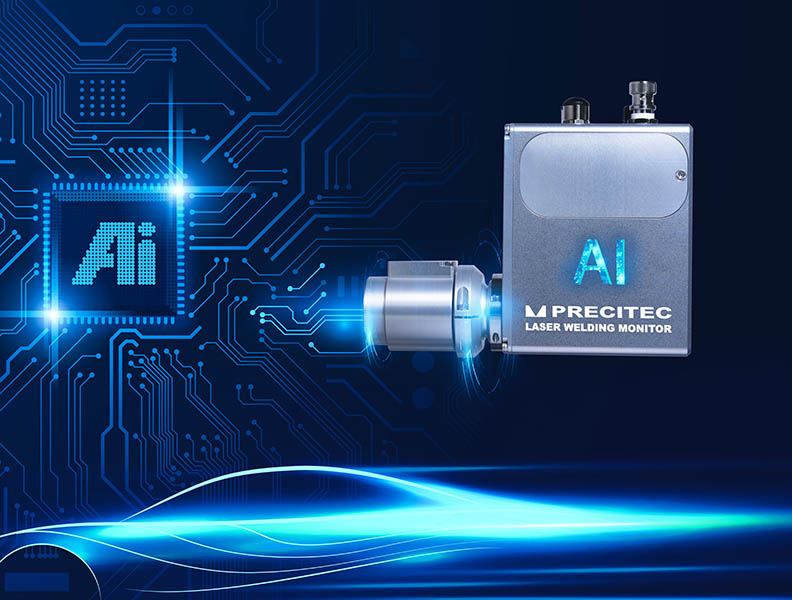
Optimized quality monitoring with artificial intelligence
Battery contacting with AI
The demands placed on production processes are constantly evolving and require innovative solutions. Artificial intelligence opens up completely new possibilities for increasing efficiency and quality. With the LWM AI, Precitec is setting new standards and enabling the clear classification of process errors and the precise prediction of physical properties of laser weld seams. The result: an objective and quantifiable analysis of welding quality - perfect for meeting even the highest quality requirements.
Detection of typical welding defects
- Change in laser power and focus position: Fluctuations in laser power or an incorrect focus position (focus shift) can lead to uneven weld seams or insufficiently welded joints. Quality monitoring detects these changes and helps to continuously optimize the process parameters.
- Gap between top and bottom sheet: If the gap between the components to be welded is too large, the connection cross-section may be insufficient or, in extreme cases, there may be no connection at all (“false friend”). In contrast to a visual inspection or a camera inspection, this defect can be reliably detected with the Laser Welding Monitor quality assurance system.
- Contaminated components: Surface contaminants such as oil, dust or rust can impair the welding quality and lead to unsafe welded joints. Quality monitoring can be used to determine whether the components are clean enough to enable an error-free welding process.
- Spatter: Contamination can cause spatter, which can lead to problems in some applications. The high sampling rate of the Laser Welding Monitor quality monitoring system can detect this spatter, which often occurs quickly and spontaneously.
- Visible pores: Material ejections (spatter) can lead to visible pores or continuous holes in the laser weld seam.
The detection of these typical defects by the Laser Welding Monitor LWM ensures that consistently high quality is achieved in production. Real-time detection also enables targeted reworking in the production plant. This effectively reduces production costs and increases production efficiency.
Applications in which we are strong
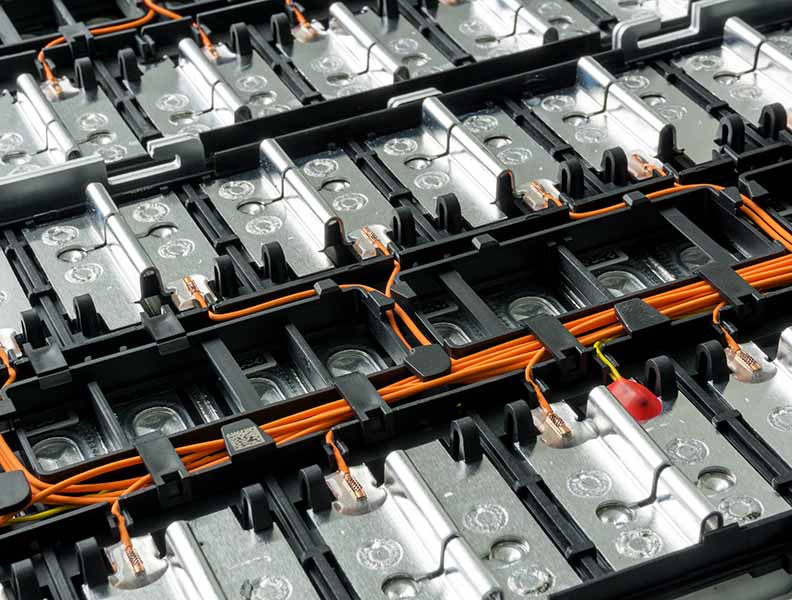
Production of battery cells
The Laser Welding Monitor LWM offers precise and innovative quality monitoring in real time, including for the welding of battery cells, battery modules and electric motors in the field of e-mobility, such as the laser welding of foil-to-tab, cap-to-can and connection contacts.
With the help of LWM AI's machine learning algorithms, physical properties such as the load capacity of the weld seam can be precisely predicted. The AI analyzes each welding process, detects process deviations and clearly classifies them.
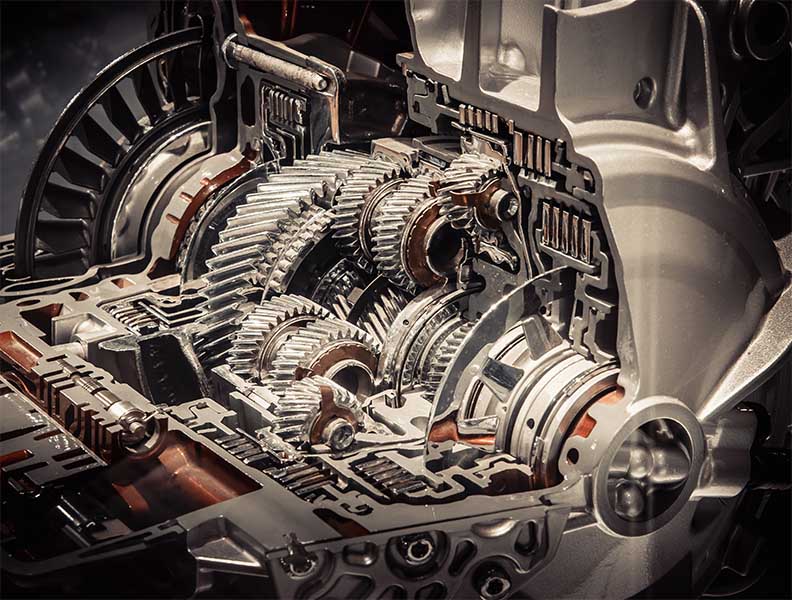
Traditional automobile construction
Quality monitoring with the Laser Welding Monitor LWM supports the efficient production of car bodies and structural components made of materials such as steel and aluminum. Real-time monitoring guarantees that every welded part meets the highest standards of accuracy and strength and minimizes reject rates.
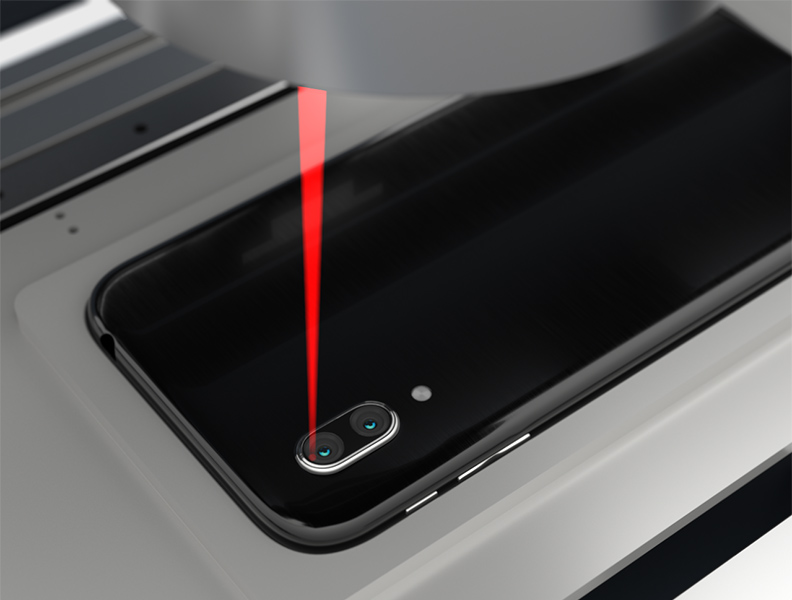
Consumer Electronics
Monitor the production of consumer electronics such as smartphones, tablets and laptops with the Laser Welding Monitor LWM. Our systems enable precise inline inspection of weld seams, ensuring the highest quality and transparency throughout the entire production process.
Technical data
- Solid-state laser application: for IR / blue / green laser and CW or pulsed mode
- Installation options: possible in laser welding optics, scanner optics or directly in the laser source
- Deep penetration welding, heat conduction welding or high-speed welding
- Flexible interfaces: TCP/IP, fieldbus, digital I/O
We need your consent to load the form!
We use Marketing Cloud Account Engagement (Pardot) Forms to embed content that may collect data about your activity. Please review the details and click in the Pardot box to accept the service and see the content. If the form is not displayed correctly, please click once more on Download the data sheet now.
Do you still have any questions or would you like an offer? Then contact us!
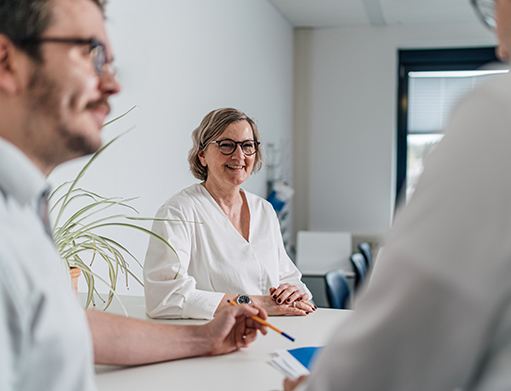